Fundamentals: Grinding trials
In this Motion Blog, we provide you with the fundamentals for preparing and completing successful grinding trials.
Step 1: Checklist

Having the workpiece blank available is crucial for a successful grinding trial. If there are no blanks of the actual part available, the grinding trial must replicate the form, surface finish, and cycle times with the same or similar material as the actual part.
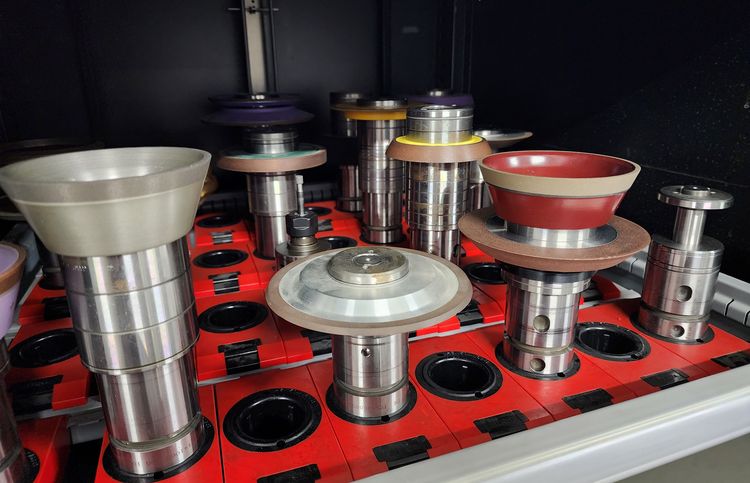
The material to be ground directly influences the choice of the grinding wheel. Factors, such as material hardness, surface quality requirements, amount of material to be removed, and cycle time requirements determine the composition, shape, and dimensions of the grinding wheel.
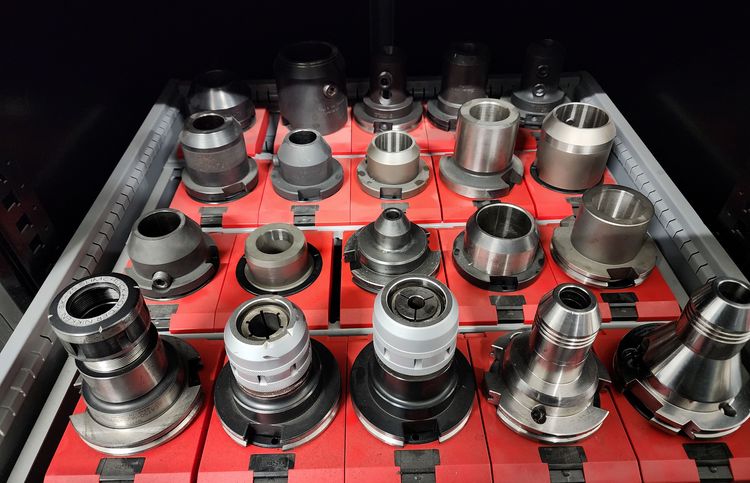
Does your part need to be moved along several axes to machine complex curvatures or other geometrical forms? Can it be clamped between centers or is a chuck or collet system required to keep the workpiece stable during the grinding process? A successful grinding trial requires the correct clamping system, which will also used in the production process, to achieve the best results.
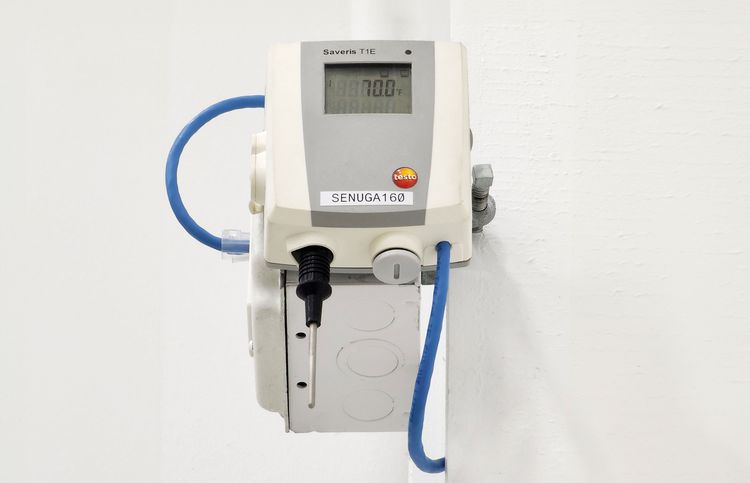
When grinding with tolerances in the micron range, especially in a high-level production environment, temperature stability is essential. Even the slightest variation in temperature can cause the part to be out of tolerance due to thermal deformation. A temperature-controlled environment for the measurement of the part and a stable thermal system in the grinding machine are crucial factors for a successful grinding trial.
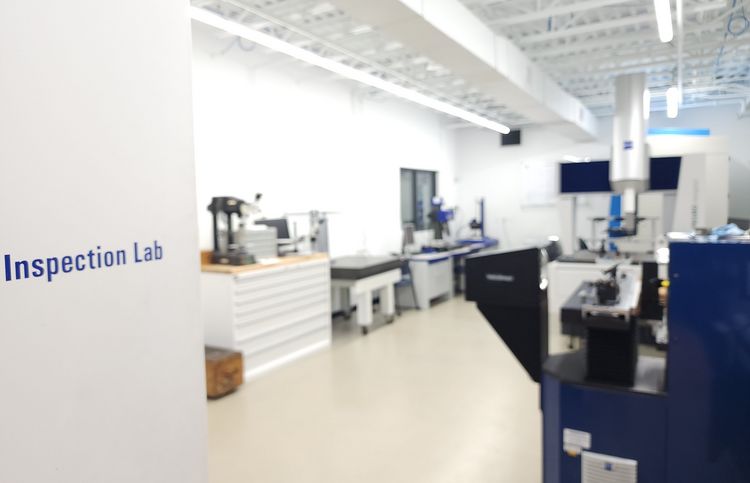
Depending on the size of the workpiece, even holding the finished part in your hands can transfer enough heat to cause the part to go out of specification due to thermal expansion. When doing a grinding trial on a workpiece with tight tolerances, use special measuring systems to measure the ground part as accurately as possible.
Other Items on Your Checklist
- Coolant management systems: The correct use of coolant is essential for every successful grinding trial. Coolant management includes coolant selection, coolant supply, filtration, and cooling of the coolant. Different grinding machines and processes require optimized amounts of coolant to achieve the desired results.
- “Finished” part sample: A sample of the finished part within tolerance is not necessary but is helpful to compare the part produced in the grinding trial with the part identified as “in specification”.
Step 2: Communication and Defining Targets
Open and direct communication between you and the application engineers performing the grinding trial is essential. Detailed questions can always arise even if they have been informed about the project in advance. Transparency and agreement on the goal of the grinding trial are also important. Can the machine grind the part within the specified cycle time and tolerance and maintain the repetition accuracy?
Step 3: Implementation of the Trial
If steps 1 and 2 have been carried out correctly the grinding trial usually runs smoothly. Our application engineers collect all the necessary information and data during the grinding trial to evaluate the result. Accurately measuring the parts is a crucial factor.
At our sites where grinding trials are performed, we have inspection laboratories with sophisticated measuring equipment and air-conditioned rooms for accurate measurements.
Step 4: Completion
Once your grinding trial has been completed and the measurements recorded, we will return your finished parts within specification, so that you can run additional tests or measurements if required.
We are happy to assist you.
Contact us if you are looking for a suitable machine for your grinding application. We are happy to assist you.