Workpiece changeover with programmed acquisition
Anyone who has to grind a large number of different components and carry out the corresponding number of changeovers, knows how important it is to keep lost time to a minimum. The active positioning probe from STUDER fulfills many different tasks:
- Basic set-up and determination of reference of probe and grinding wheel to B-axis pivot point
- Manual workpiece changeover in set-up mode
- Length positioning
- Thread positioning
- Circumferential positioning
- Ø and length inspection
- Automatic acquisition with reference dimension Z
We would like to discuss the last point, the automatic acquisition of a new workpiece during cylindrical grinding on a STUDER-machine, in more detail below.
Automatic acquisition with reference dimension Z
The reference dimension Z is set once during set-up. A reference is set from the table scale to the probe. Put simply, we tell the machine at which length the probe should swivel in, in order to search for the workpiece from that point. Once this reference is created, the new length value and Ø-position of the new workpiece can be defined later in the program. The probe thus swivels in at the correct position and finds the zero point of the new workpiece without having to perform a new acquisition in set-up mode. The condition for this is that the machine is equipped with the Quick-Set option.
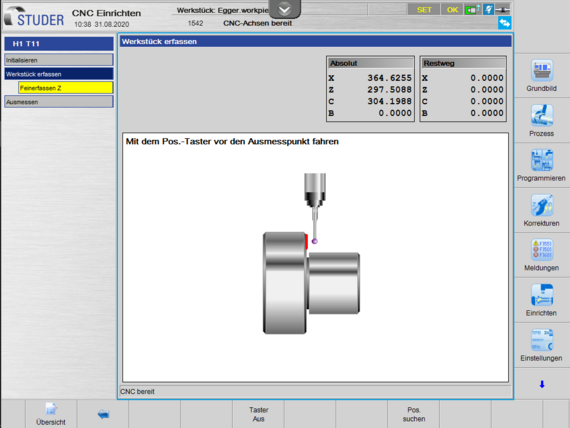
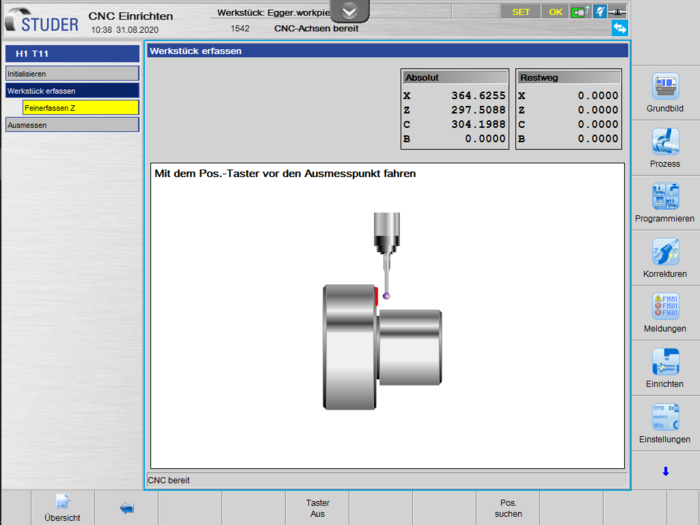
The set-up process is performed in the usual way.
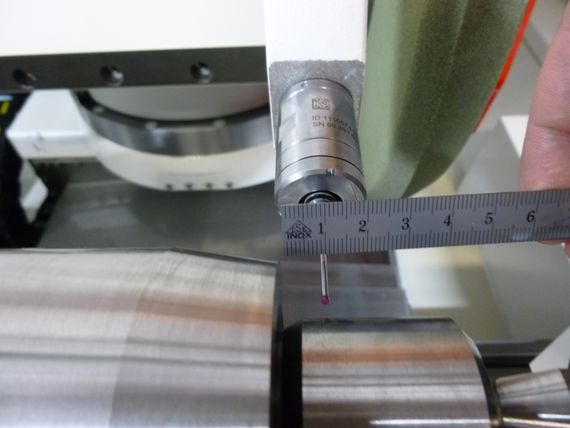
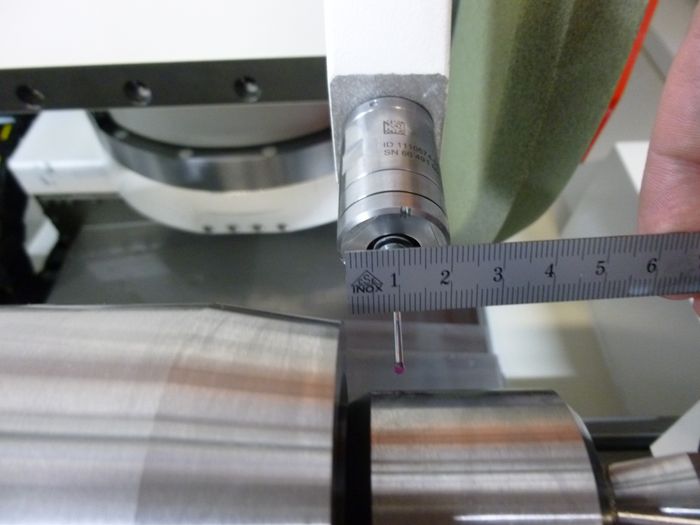
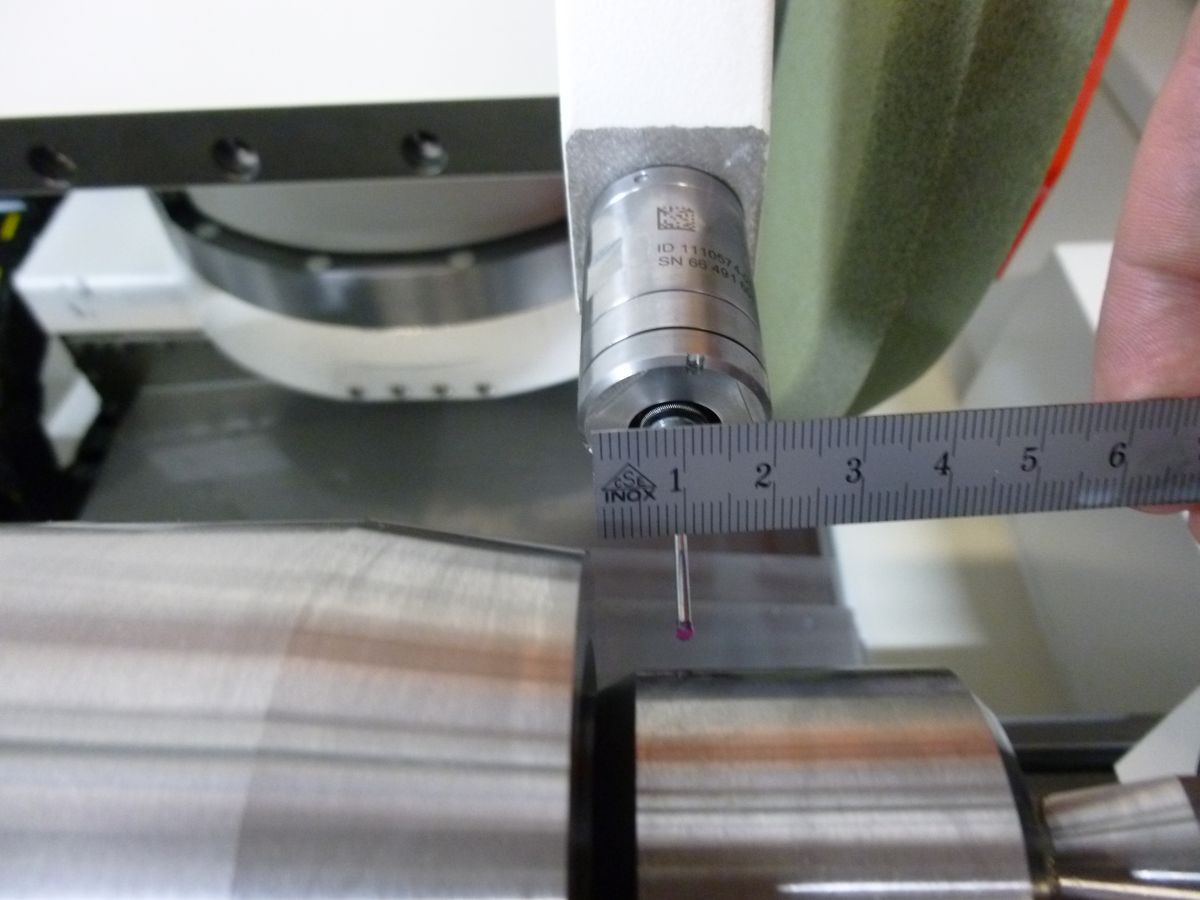
Manually move the probe approx. 10 mm in front of the shoulder to be probed. Make sure that the ball touches the shoulder and not the shaft of the probe (undercuts, height of shoulder).
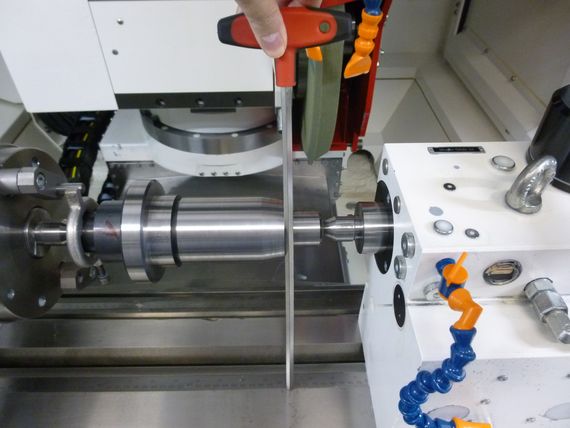
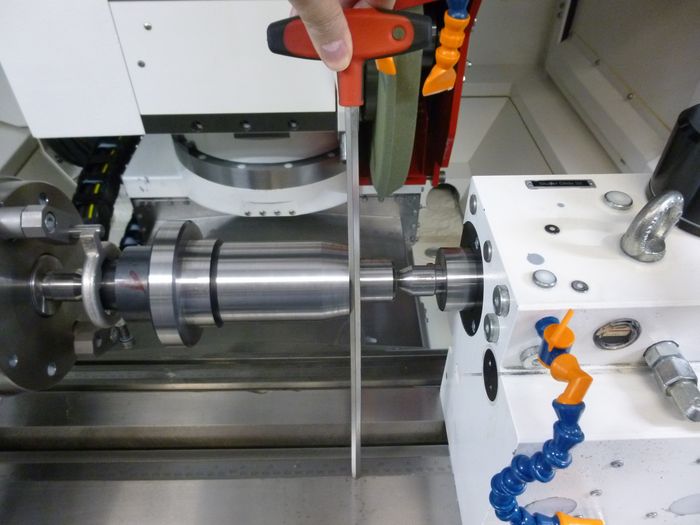
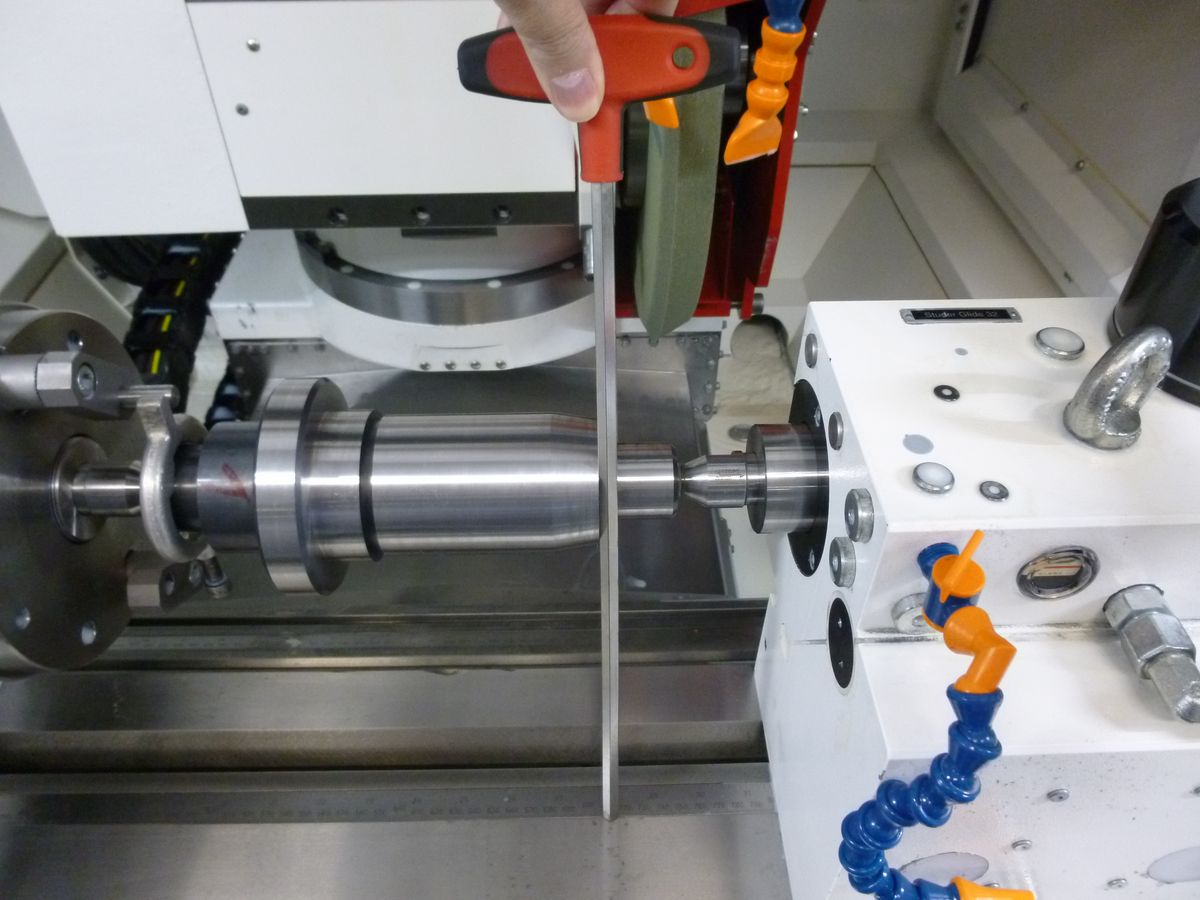
Now we find the vertical from the probe position down to the table scale. In our example this is done with a long tool. However, a large angle or a plumb bob can also be used.
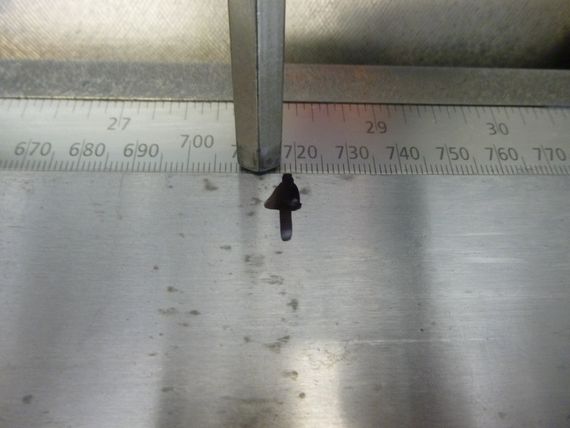
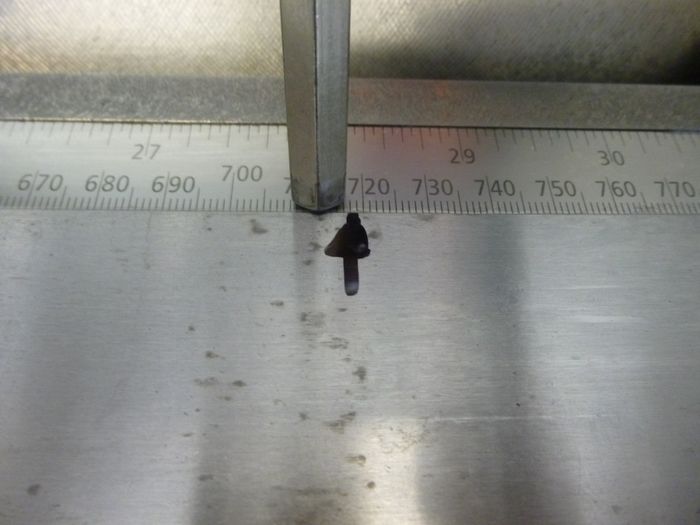
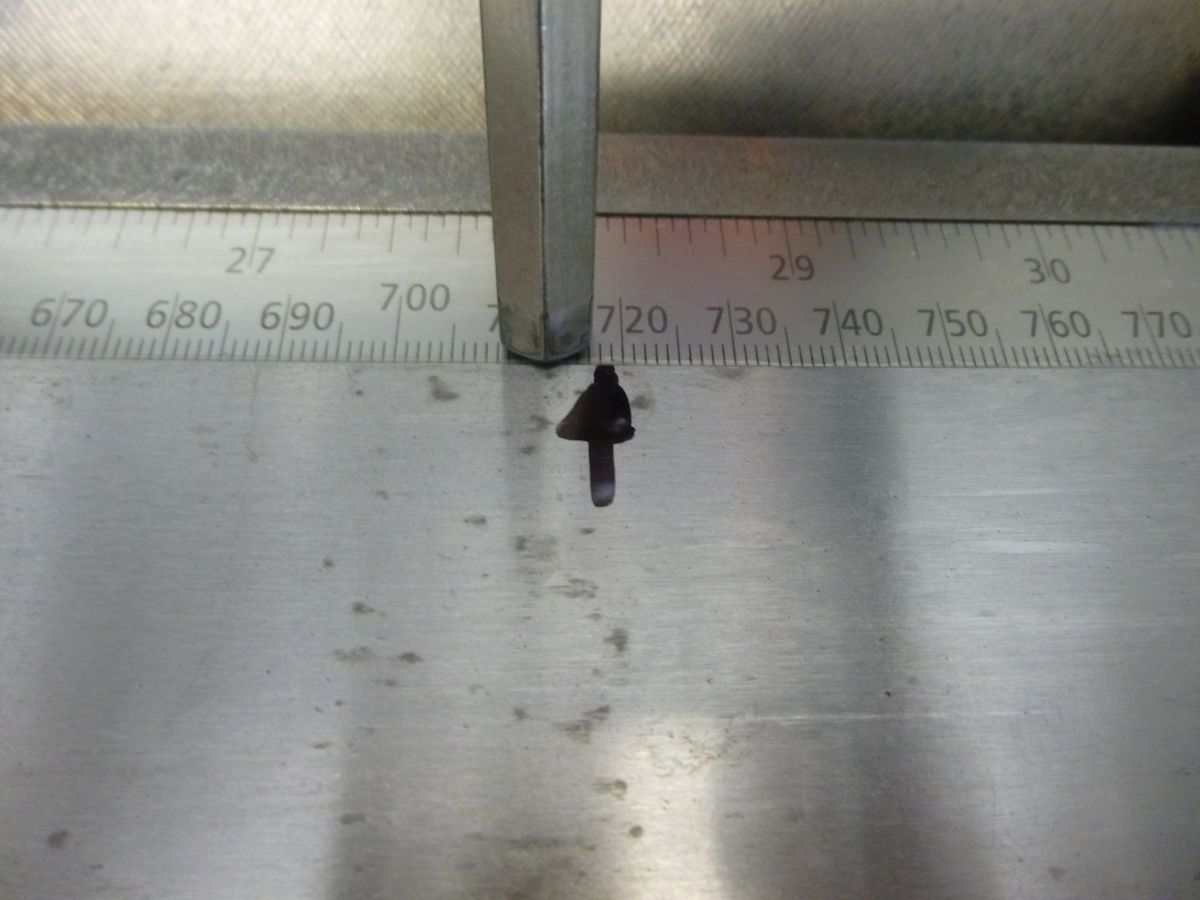
In our example we read 718 mm.
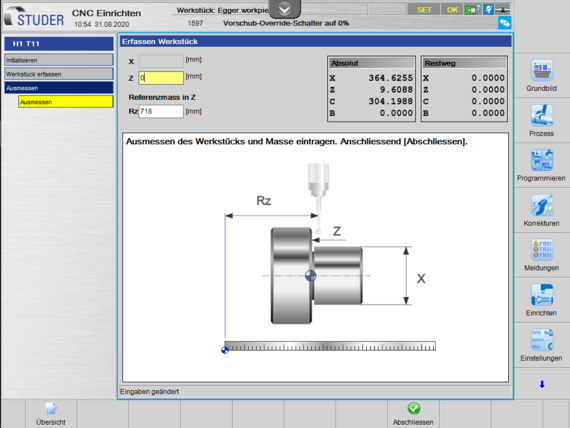
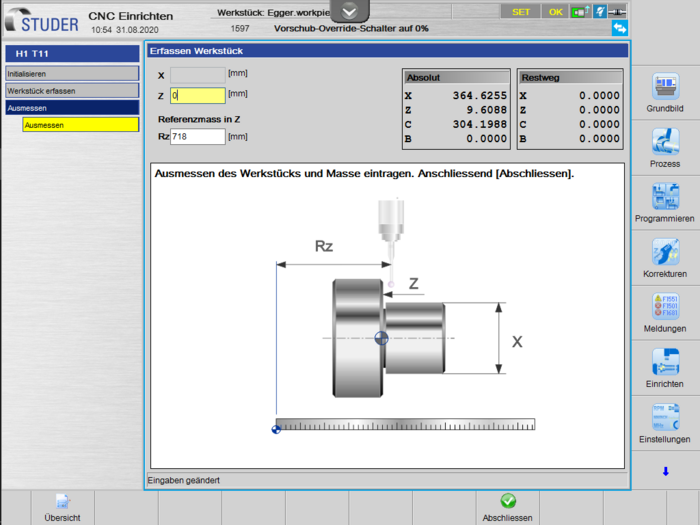
These 718 mm are now entered in the field Rz. 0 (zero) must also be entered in the field Z. The first acquisition must therefore be performed exactly at the workpiece zero point.
The workpiece zero point and the reference dimension Z are now set.

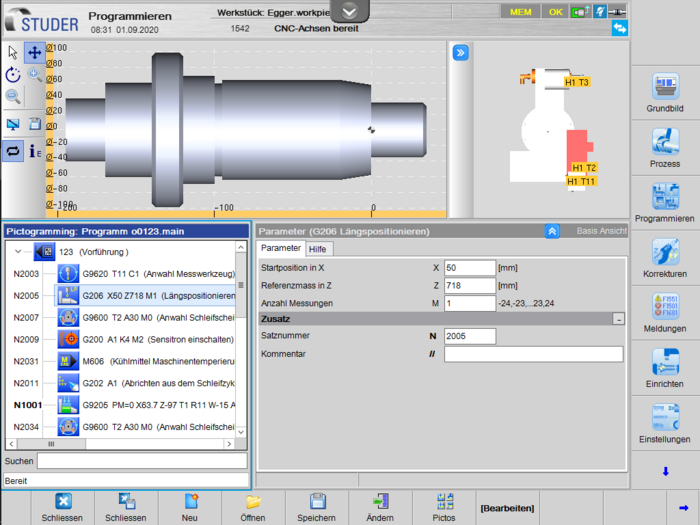
In the workpiece program, the values X & Z are now programmed accordingly in the length positioning cycle. In our case, the start position of the probe is 50 in X and the recorded 718 mm in Z.
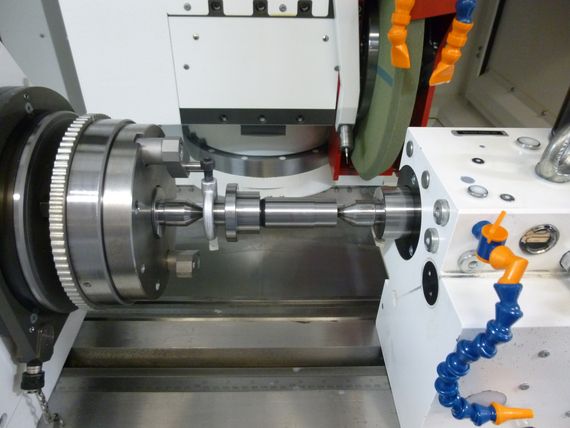
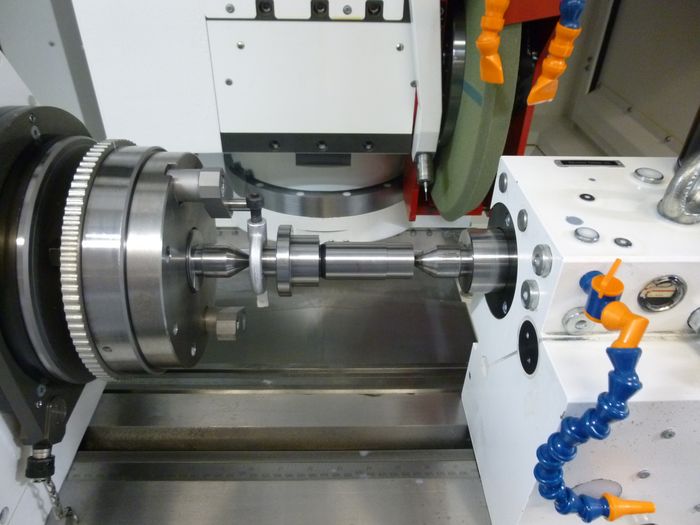
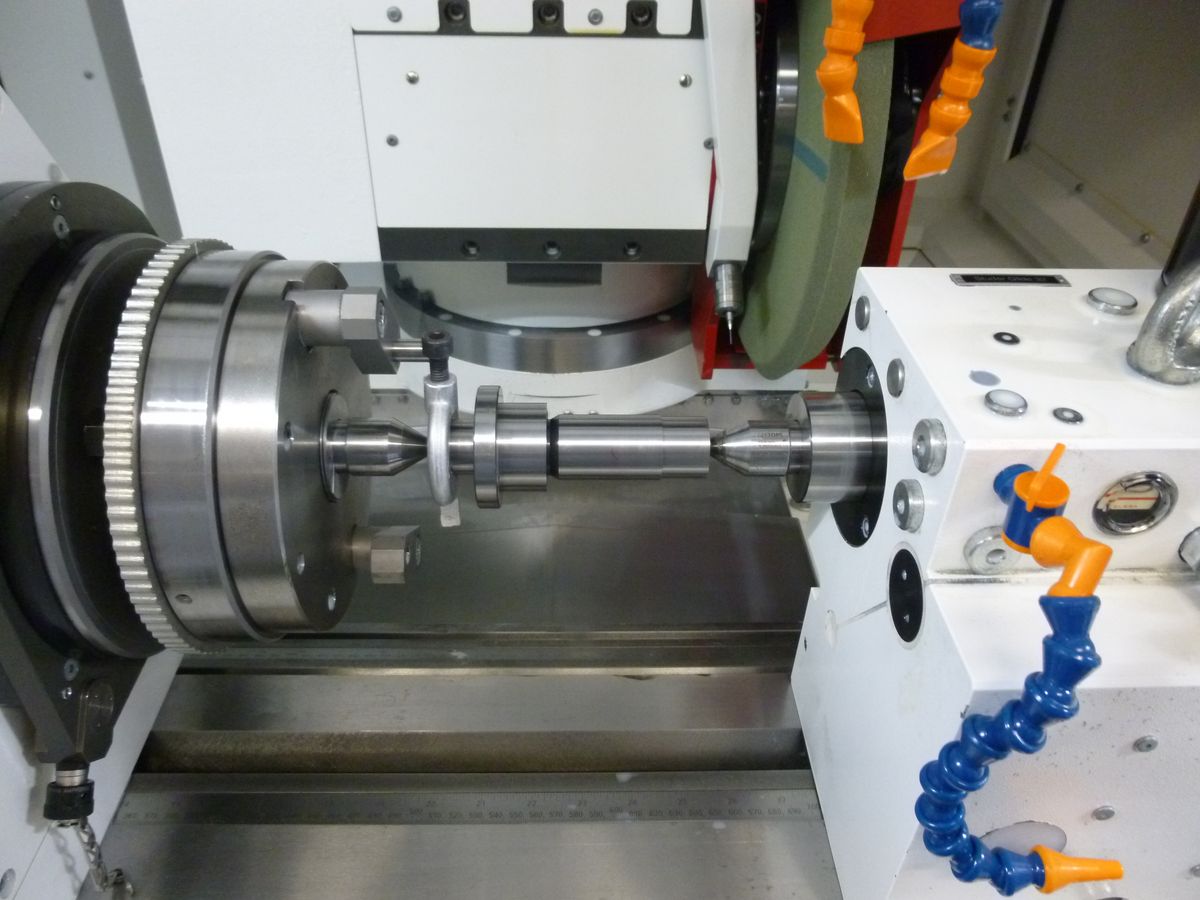
After this you can change to any other workpiece. You will see that very little effort is required to acquire the new workpiece zero point again. If other tools are required to grind this workpiece, these would of course also have to then be acquired.
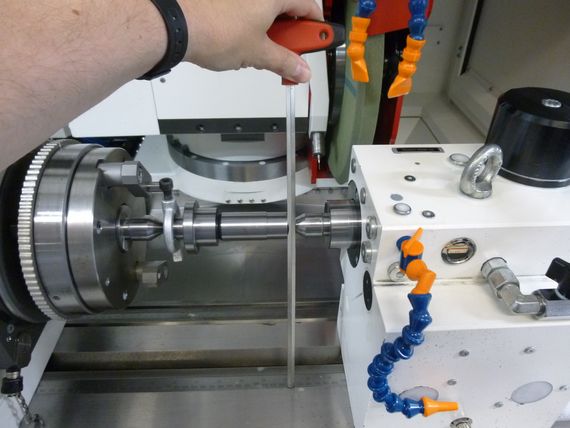
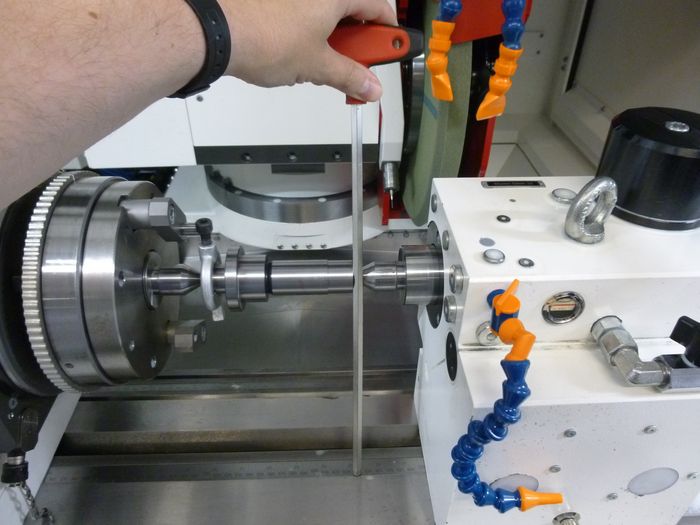
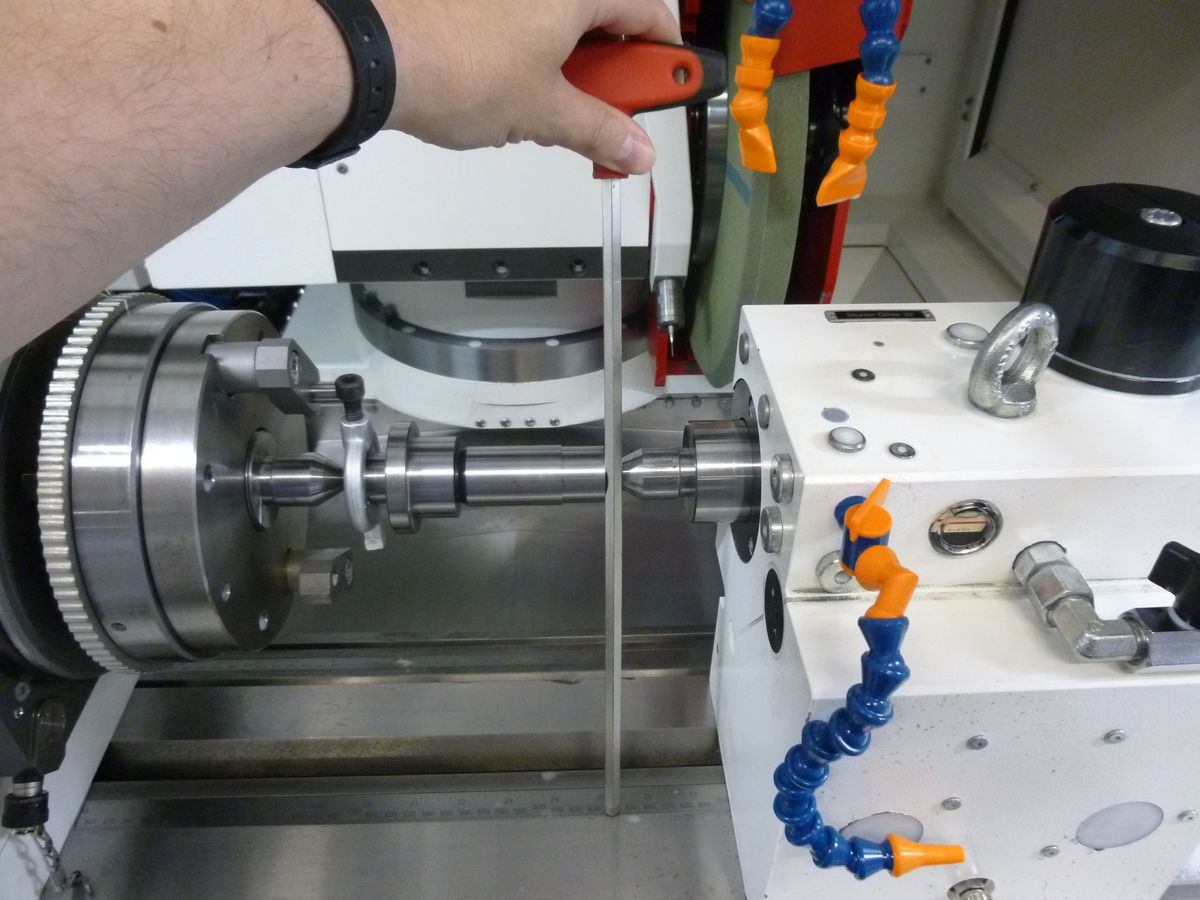
Re-determine the position for swiveling in the probe.
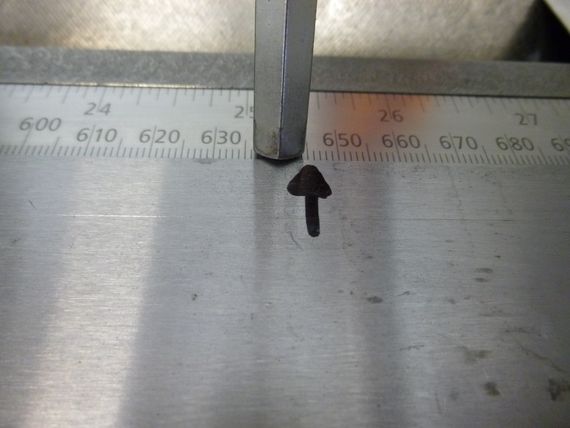
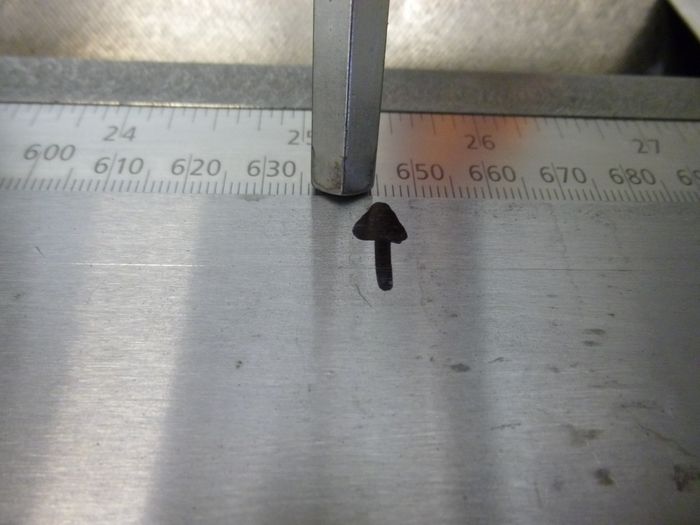
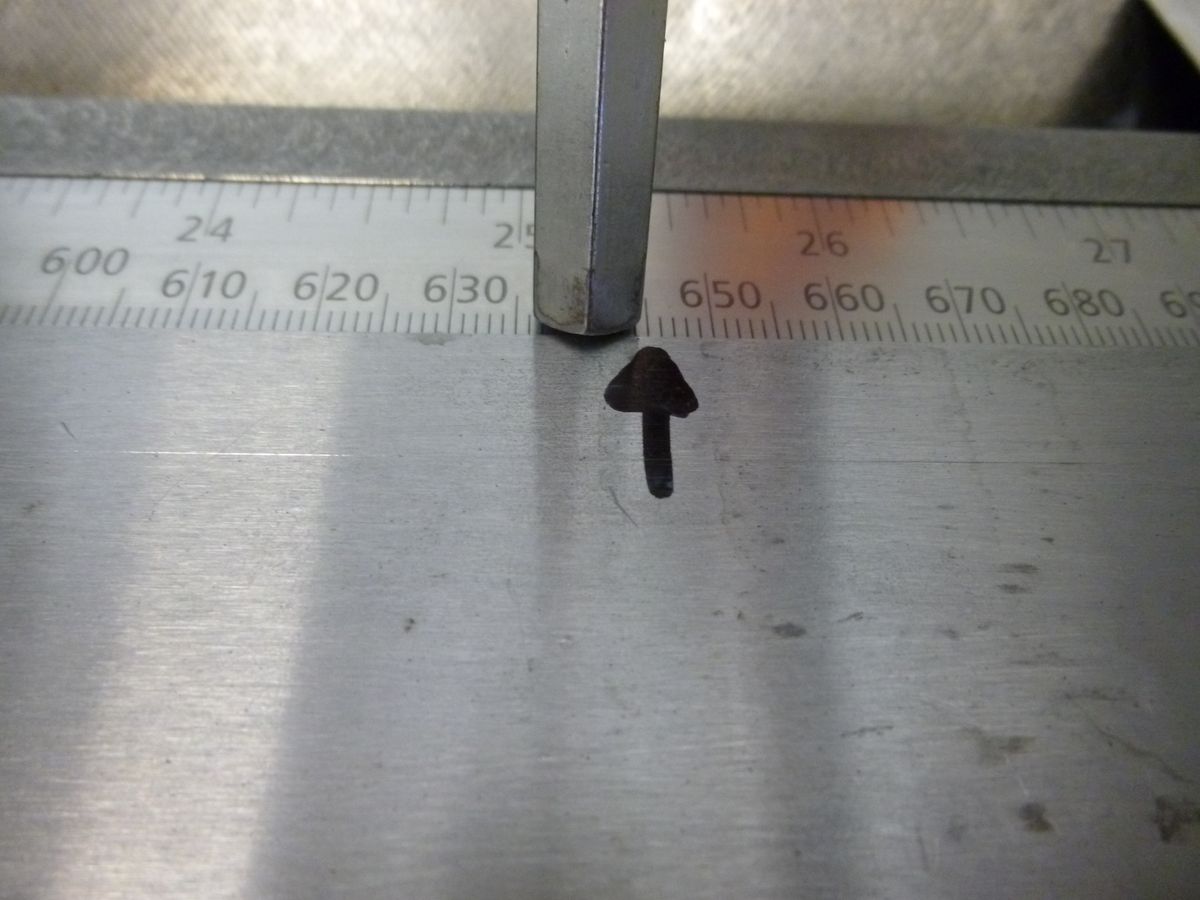
In our new case the table scale indicates 645 mm.
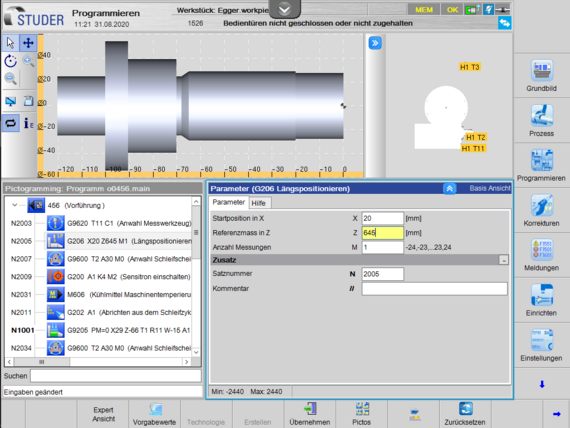
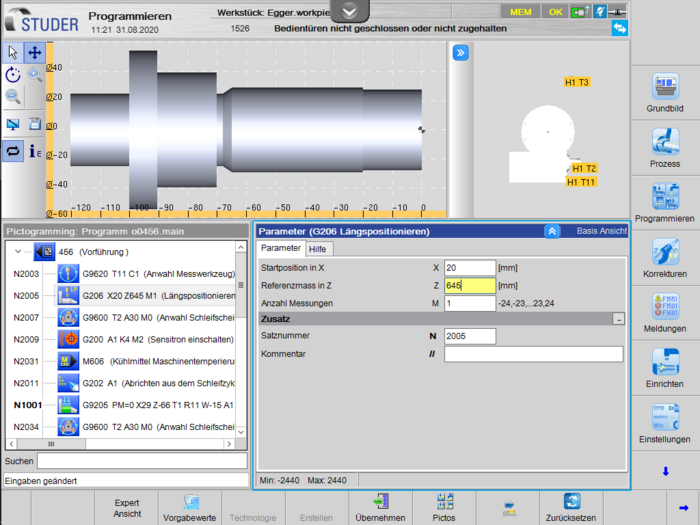
This value is once again entered in the length positioning cycle of the new workpiece program. X 20 and Z 645 mm.
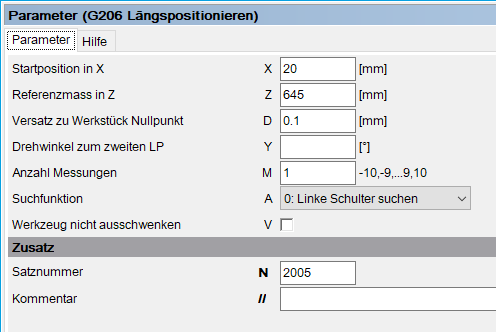
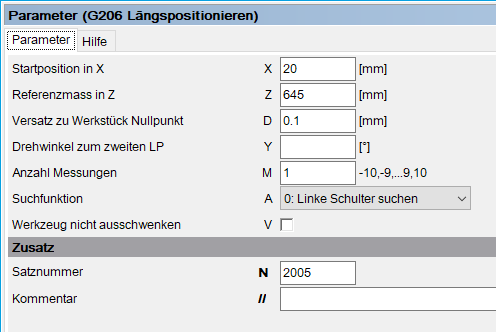
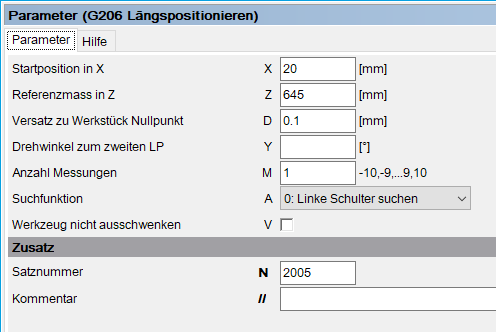
If 0 is not probed accurately to Z on the workpiece because of grinding allowance or other reasons, a corresponding offset can be programmed in parameter D under expert supervision.
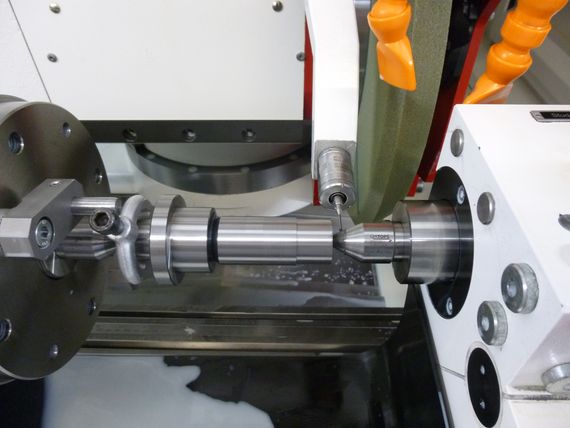
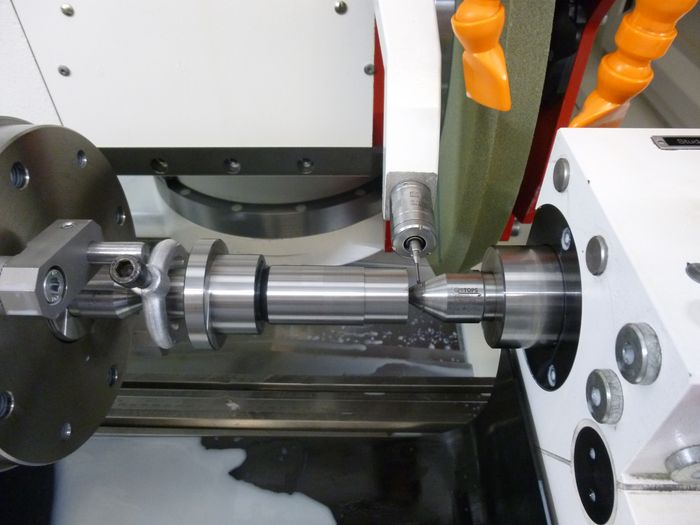
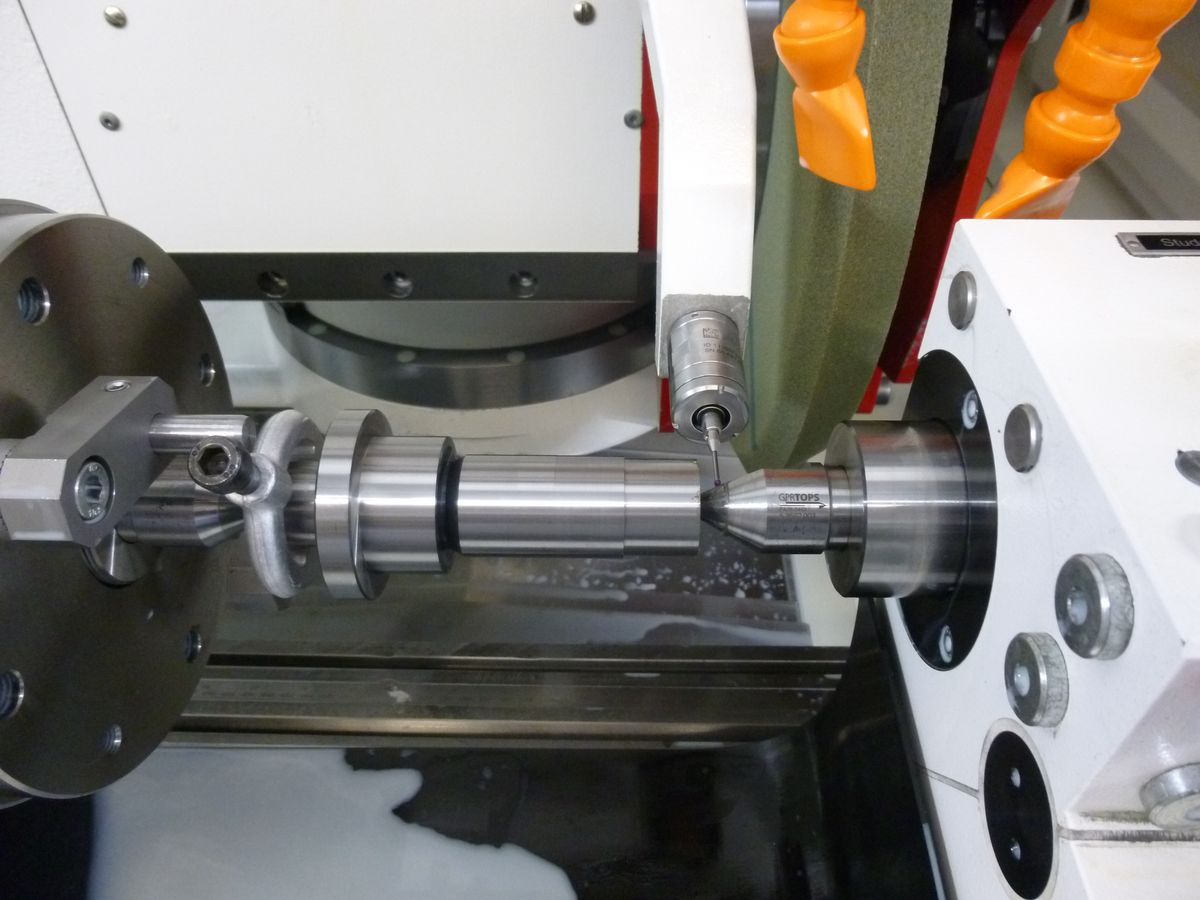
If the new program is now started, the machine moves with the probe to the relevant position and sets the new zero point there.