How do we make the supply chain more resilient?
With the coronavirus pandemic and the Ukraine crisis, the resilience of supply chains has become a key competitive factor. Has supply chain management become supply chain risk management?
CEO Stephan Nell discusses the factors that can increase the supply chain’s resilience with Sebastian Fabel from thyssenkrupp and Michael Henke from the Fraunhofer Institute for Material Flow and Logistics
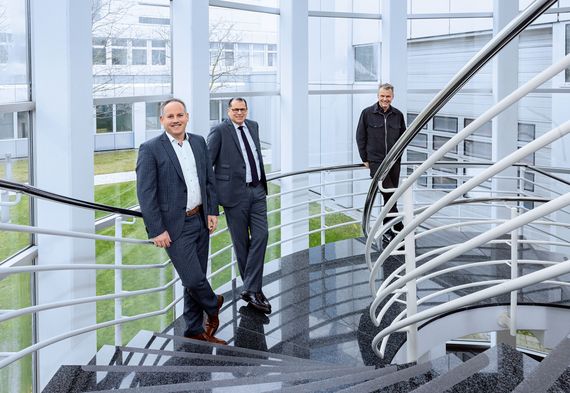
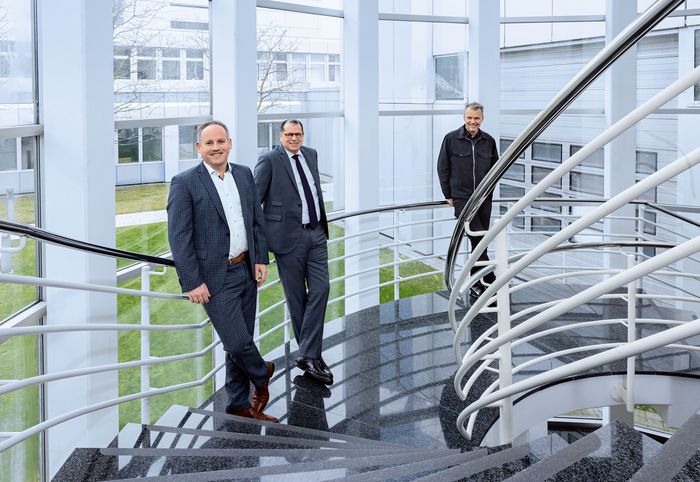
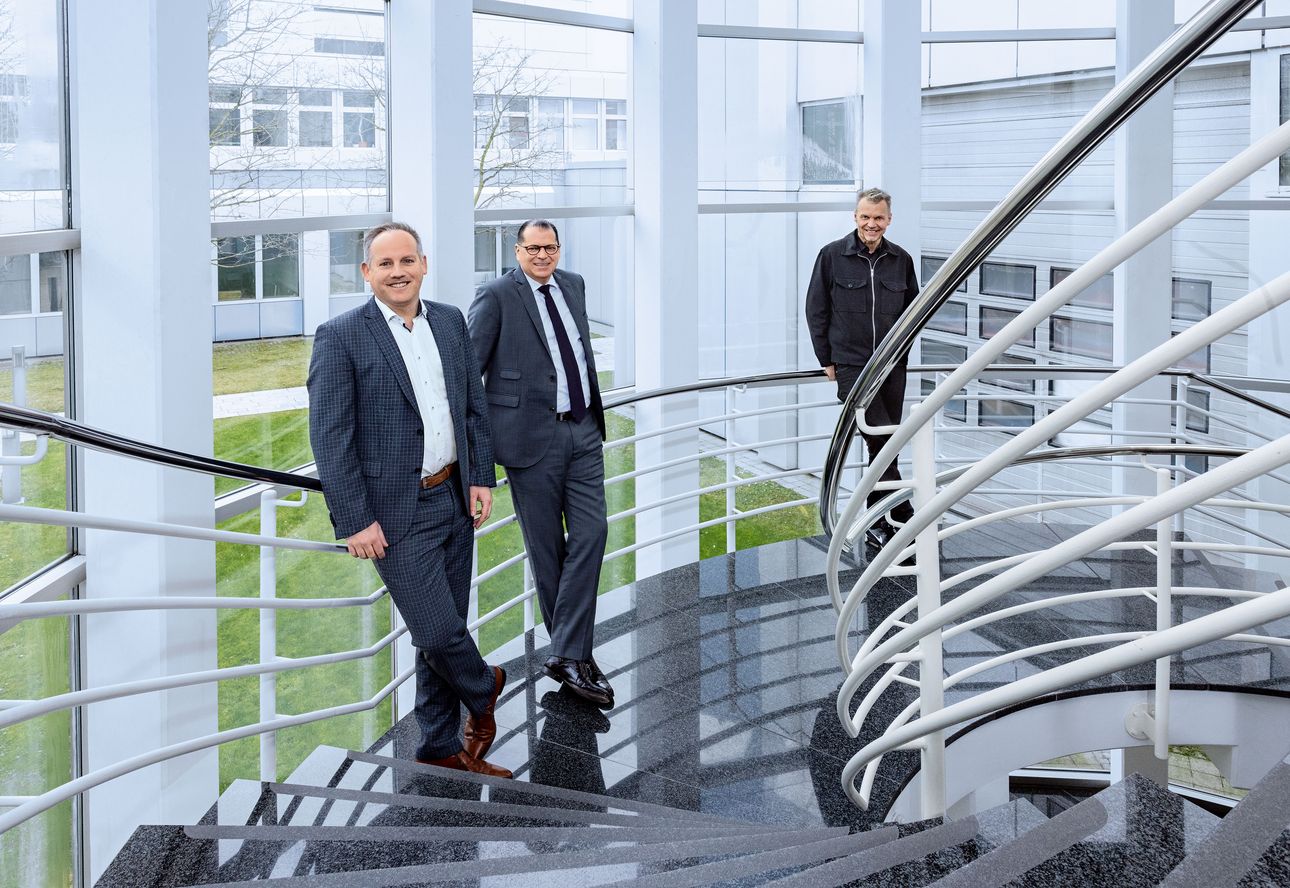
Mr. Fabel, just-in-time, that was once upon a time…
Sebastian Fabel: Supply chain risk management has become more important. In the past, just-in-time, it was assumed that the supply chain worked. I have minimal stock. We live in a well-established system. Suddenly that was over. The chips no longer came. Clearly, there are various technological aids, risk management tools, visibility software, etc. Expertise in dealing with this is crucial. The topic has moved to a different place in the strategic discussion.
Michael Henke: What many companies call risk management is more akin to crisis management. At the moment when supply chains are breaking away, the crisis is already here, the risk is virulent and therefore professional risk management is no longer possible. Pro-active risk management, on the other hand, tries to prevent the crisis situation as much as possible. Some companies achieved this very well, even during the coronavirus crisis. Obviously, they had the case of a serious pandemic on the risk radar even though it had not occurred in recent years and had emergency plans in the drawer.
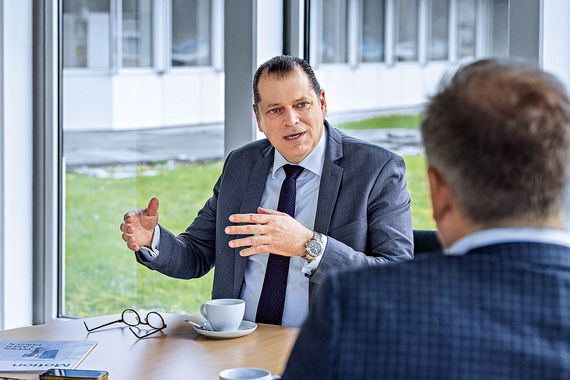
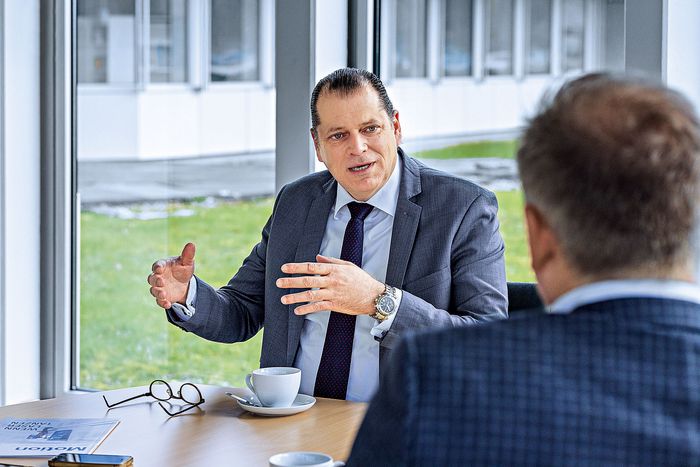
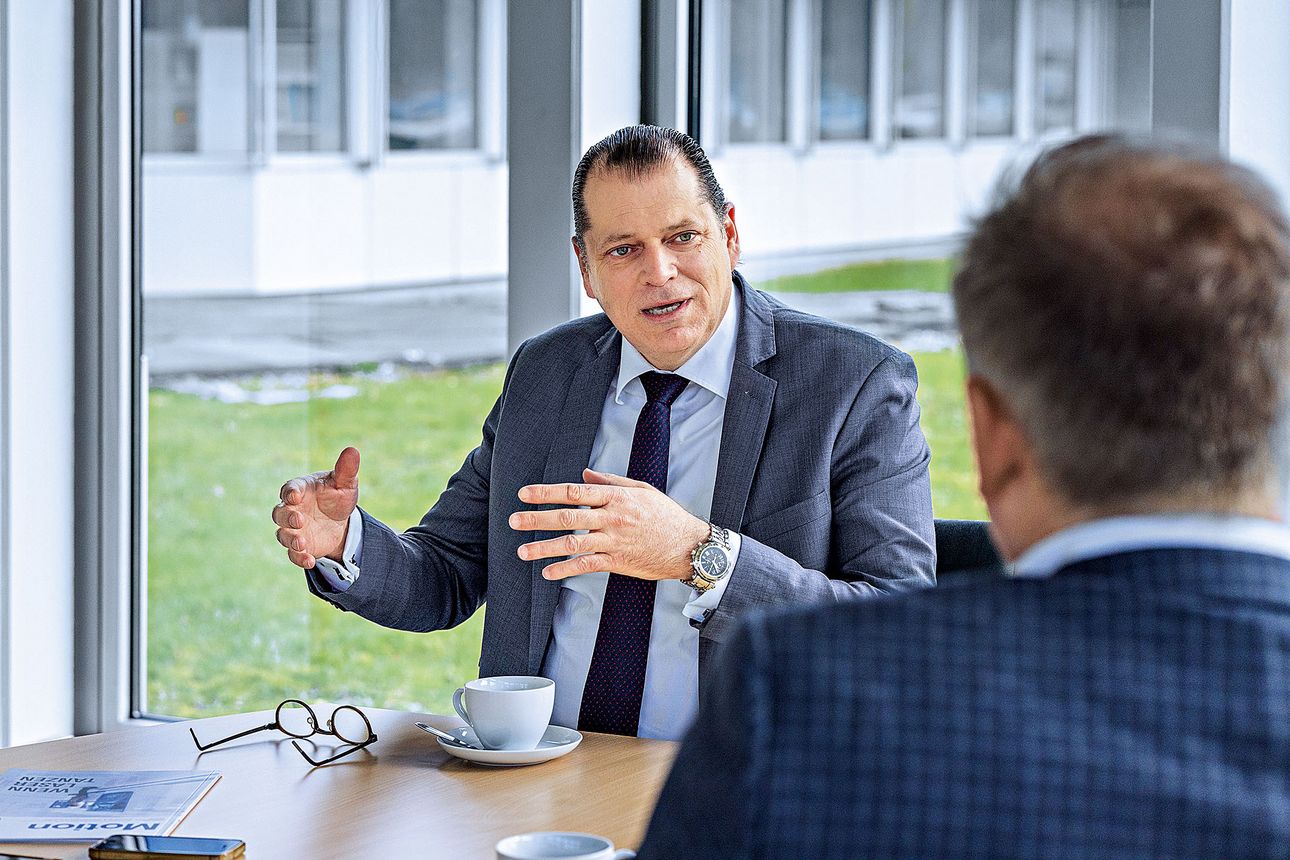
relatively robust in times of crisis
Mr. Nell, the supply chains of the UNITED GRINDING Group have proven to be relatively robust in the face of the upheavals. How did you do it?
Stephan Nell: One aspect is that we have never placed much focus on where the material can be obtained most cheaply. We often buy from a location close to our production. Another point is that we involve our suppliers early on. And also important: The UNITED GRINDING Group has a high real net output ratio. We often do not need the finished component, but only the raw material – which was easier to procure during the crisis.
Regardless, how severely were you affected?
Stephan Nell: We felt it. For a while, we spent about a third of our engineering capacity on examining how we can build the machines with other components while maintaining the same quality. This, combined with great commitment and flexibility in the operations department, enabled us to deliver about 40 percent faster than most competitors. However, the installation of other parts still has consequences for us as a machine manufacturer in that it affects us for the next 20 or 30 years – that is how long the parts need to be available for delivery as part of our service.
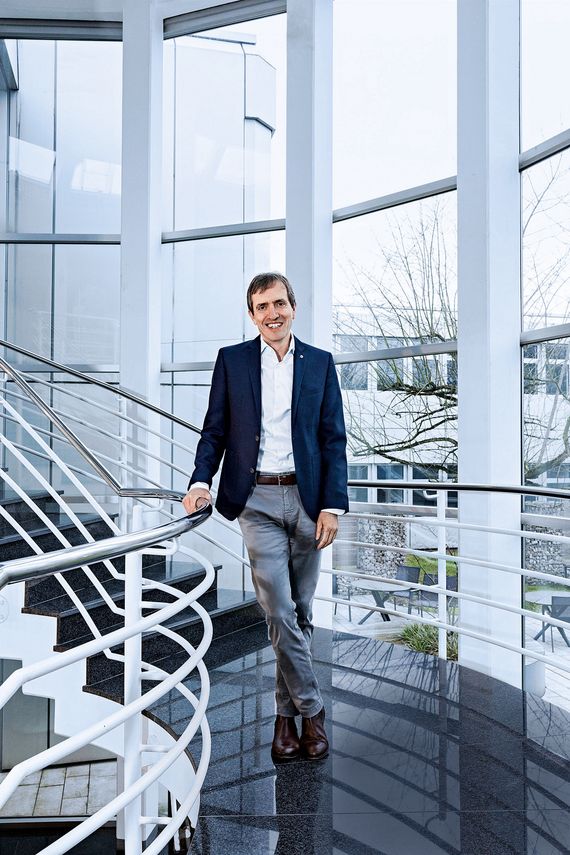
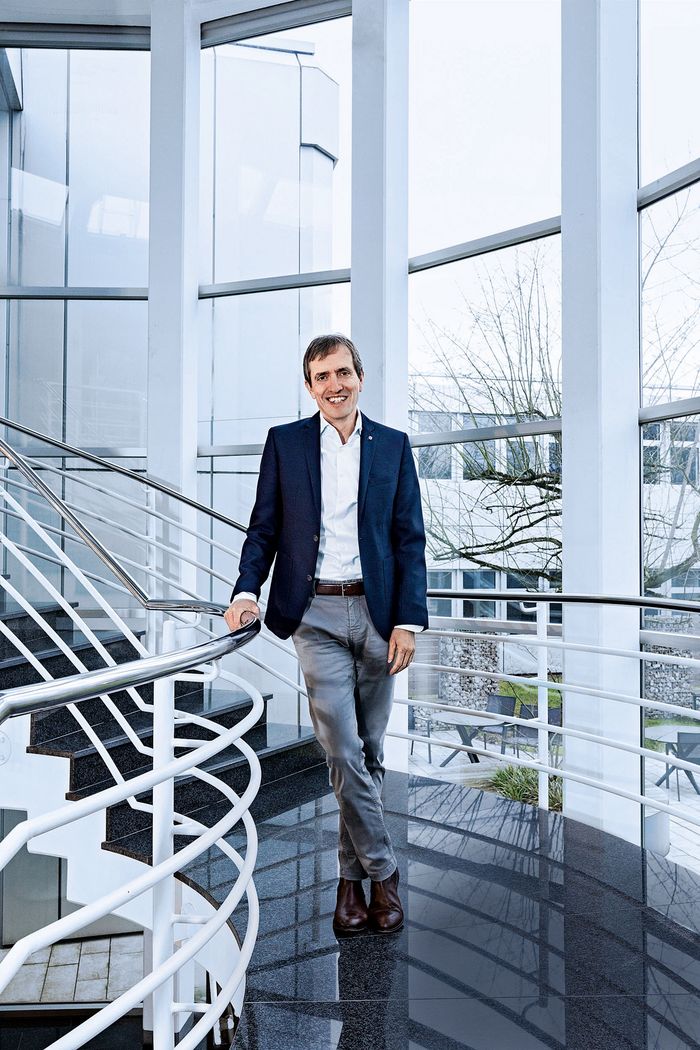
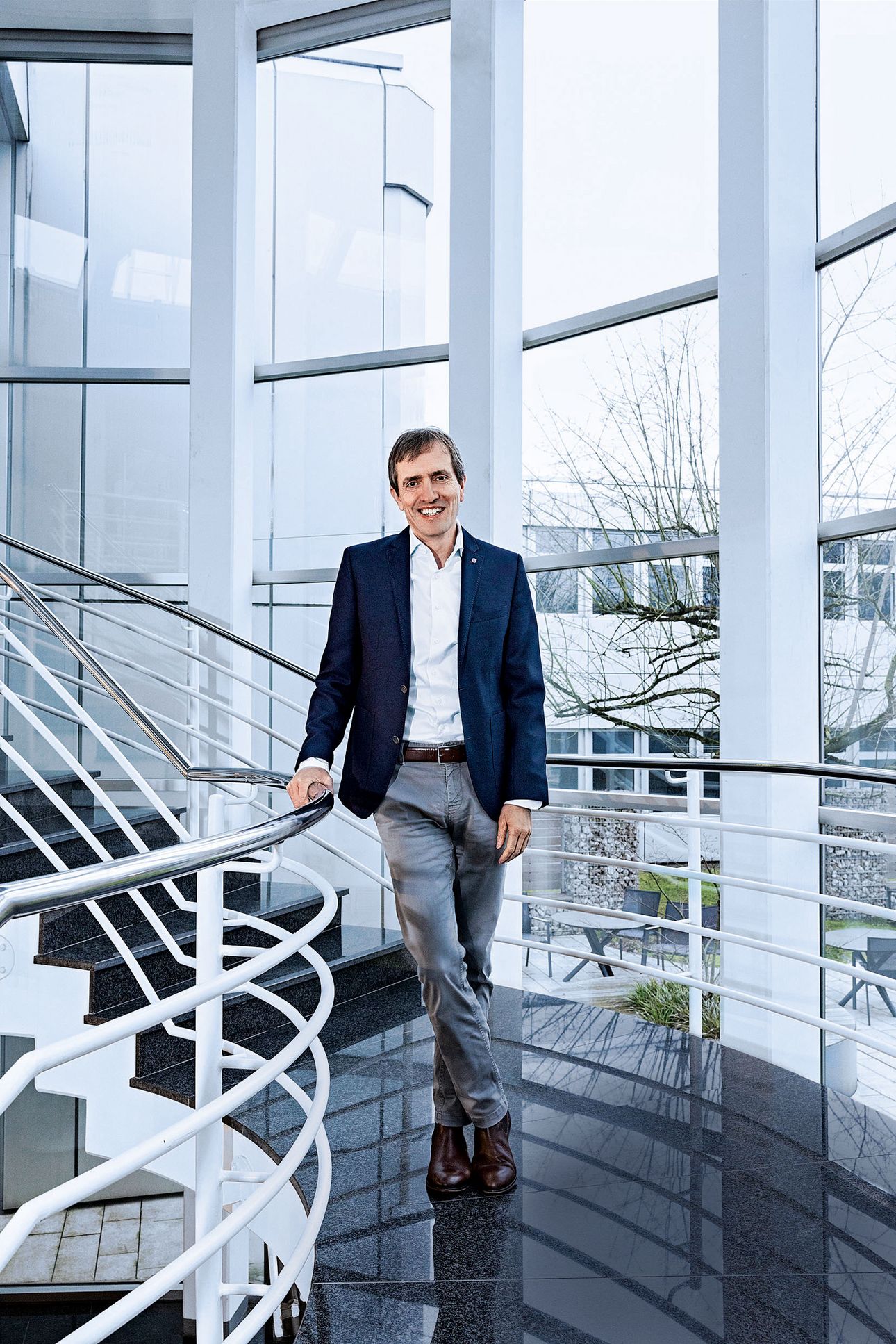
We often hear that the alignment of supply chain management in companies needs to change. from low stock levels to greater security of supply, placing slightly less focus on efficiency. Do you share that opinion?
Stephan Nell: Theoretically, yes, but in practice the problem isn’t usually that your stock levels are too low, you just have the wrong thing. And the art is actually having the right parts in stock. I don’t think it’s a good idea to build up huge inventories to be prepared for a crisis, which will certainly happen again at some point. If I build up stock levels today and the crisis comes in five years’ time, I’m guaranteed to have the wrong thing.
Sebastian Fabel: It is certainly not about increasing inventories beyond measure. We also see how capital commitment costs, interest rates, and inflation are developing. There is still a need to keep working capital as low as possible.
Stephan Nell: We are currently testing a kind of early warning system. Software scans the information in the world that is relevant for a smooth supply. Using this should then make it possible to derive whether there is an impact on a component that we have to buy in six months or three months. Maybe it helps, maybe not.
Michael Henke: Limiting supply chain disruptions and delivery process delays as much as possible primarily requires one thing: Transparency. The sooner and more clearly I see what I’ll be facing in terms of the supply chain, the sooner, more flexibly, and affordably I can successfully prevent disruptions and delays, or at least reduce their effects. At the same time, I am building a foundation for sustainability and flexibility. The more clearly I see, the more sustainable and flexible my management becomes.
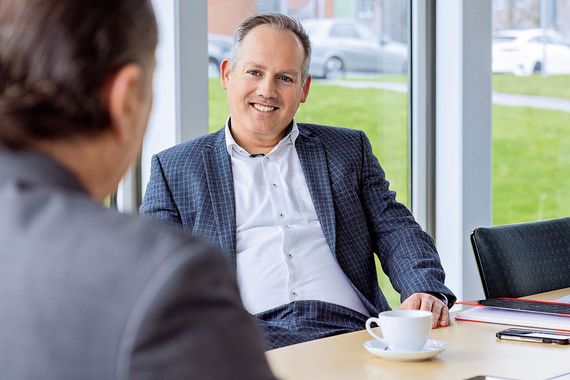
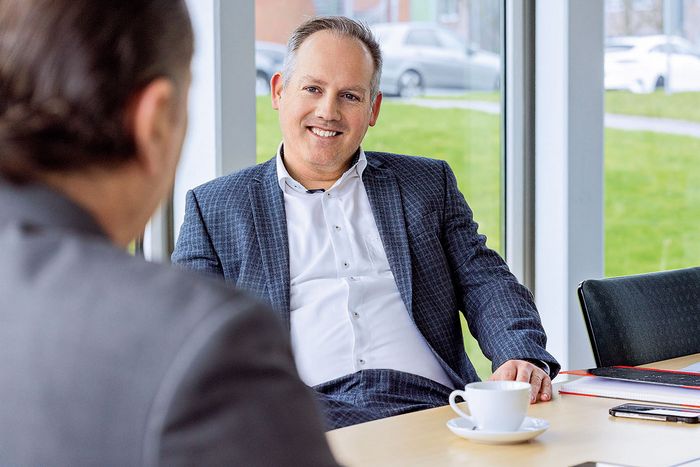
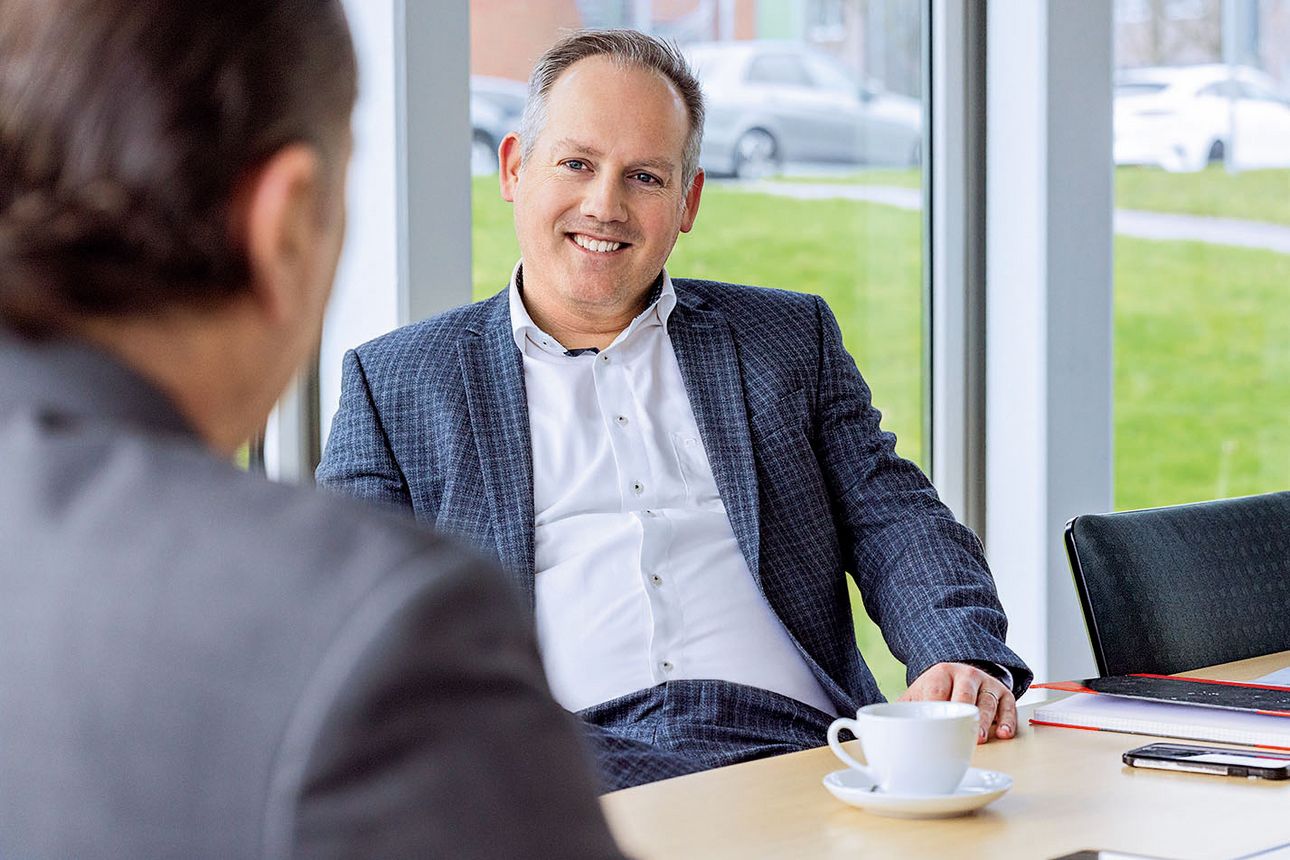
Dr. Fabel, with 250,000 customers around the world, thyssenkrupp has become an intermediary in supply chains with the “Materials-as-a-Service” strategy. What does that mean?
Sebastian Fabel: thyssenkrupp itself has a lot of in-house expertise to manage sites, products and supply chain networks. Against the backdrop of increasing challenges in the supply chain, we use this expertise as part of our “Materials-as-a-Service” strategy by supporting our customers with innovative services such as demand forecasting, or the optimization of complete supply chains.
Mr. Nell, are there any connecting factors here?
Stephan Nell: It always depends on where you stand. A few years ago, we networked all plants in an SAP system and plan across all plants in one system. This helped us in the situation because we were able to access it on all continents. If you have a customer who isn't at that point yet, implementing that type of project is quite time-consuming – so your services are surely useful.
Would everyone in the group sign off on the sentence: The higher the level of digitalization in the supply chain, the smarter it is?
Sebastian Fabel: No.
Stephan Nell: No.
Michael Henke: Yes and no.
Wow, that was fast!
Sebastian Fabel: Digitalizing a bad process simply makes it a bad digital process, but still not a good one. Digitalization is not an end in itself. It must be done intelligently in order to add value. This is where data-based intelligence comes into play. The information processing alone that goes along with it!
Whether it has to do with exchange rates or political risks, inquiries or prices. It creates a completely different basis for making decisions. This helps with forecast quality, visibility and responsiveness.
Stephan Nell: The prerequisites are the right processes. We can then digitalize them, but the process has to be right first. During the crisis, we also had promises from suppliers, which were revised a few hours later. Then they said that AI was now doing the allocation. I prefer to have people on the phone rather than an AI that calculates my updated needs every 24 hours and thinks it knows what we sell. All of this needs to be further developed.
Michael Henke: No one can achieve the level of transparency required today with paper trails and clipboards. This was already apparent even before COVID and the Ukraine invasion, duing crises like the financial crisis or Fukushima. Instead of that, we need to use all the state-of-the-art hardware and Nellsoftware we already possess, but especially blockchain technology. If widely used. this can actually provide excellent transparency about the companies using blockchain. At Fraunhofer IML, we have set ourselves the goal of developing the silicone economy to completely virtualize value creation processes end-to-end and then to automate and make them autonomous on this basis.
Stephan Nell: However, transparency must also be intentional. The more connected a system is, the more vulnerable it is. Is the efficiency gain so great that it is worth taking the risk that the machines will be completely at risk in the event of a cyber attack? We’ve experienced it for ourselves. We were attacked and we had to perform a hard shutdown of the systems. Our plants had different networking levels. A plant with systems that still had a certain degree of isolation came back online faster than fully automated ones — those took the longest.
It is often said that experiences during COVID taught us a lot. But what exactly? And can we use this to see into the future?
Michael Henke: Churchill said, “Never let a good crisis go to waste!” If we have learned one thing – times are not getting safer. Therefore, we need to learn more and faster from crises and further develop our value creation networks. When supply chain managers collect all the accessible and available data from a value creation network, they can – ideally via real-time monitoring – identify who in the supply chain is affected where and by what.
Is climate change also having an impact on supply chains now?
Sebastian Fabel: Climate change itself is not yet making itself felt, but rather the various preventive measures, such as the German Act on Corporate Due Diligence Obligations in Supply Chains, emissions reporting, and emission prevention strategies. And it is being felt within companies in their search for concepts that cut emissions and enable circular value creation.
Stephan Nell: In the UNITED GRINDING Group, there is one ecological aspect that is decisive when it comes to procurement. It doesn't make sense to transport components across the world’s oceans if I can purchase them on the same continent. In my opinion, transport is too cheap. It is worth transporting inexpensive components from A to B, because transport effectively costs nothing. I think the world could benefit from more nearshoring. We can already see this on the customer side. Not in Europe. But in Europe, we tend to talk about an issue for a very long time first. There are other countries in the world that simply started. This could lead to reduced transport volumes, which would certainly help the climate.
How difficult is it to meet societal and political demands on supply chains? Aren’t there often conflicting goals?
Sebastian Fabel: The Act on Corporate Due Diligence Obligations in Supply Chains will certainly lead to expenses, initially. However, we also see the opportunities in sustainable solutions. For example, we are currently working with a manufacturer of production equipment on a research project in which we improve visibility in the supply chain in order to reduce sheet metal waste in the supply chain and thus save material and CO2 .
Stephan Nell: For us as medium-sized companies, many things are very difficult to implement and impractical. When we purchase steel from the dealer, we often don't know which foundry it comes from, how much electricity was consumed during production, let alone how sustainably it was produced… European policy is struggling to find a measure for evaluating a machine’s energy consumption. It doesn't work the way it does for a washing machine. If it is possible to optimize the process and produce the part three times faster, the contribution to the climate is much higher than if the machine consumes a little less energy.
Sebastian Fabel: In our Swiss t-kontrol project, documents are digitalized in order to make the history of a product visible to the customer and, in the medium-term, to show the original mine that produced the ore in a product. This provides the customer with complete transparency and a paper trail. We are currently developing and testing this with our customers, who can also map and calculate the carbon balance.
Stephan Nell: They say they are in development. But we face the challenges today.
Sebastian Fabel: Yes, that’s precisely the question. How do I make the transition from the status quo and pilot projects to the target structure and scaling? When the Ever Given got stuck in the Suez Canal, everyone wanted real-time transparency to know which materials were where. But I think there were too many phone calls and Excel files to find out. The costs were then many billions of dollars.