Operate the machine like a smartphone
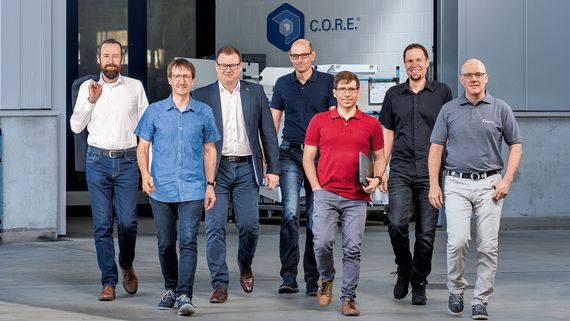
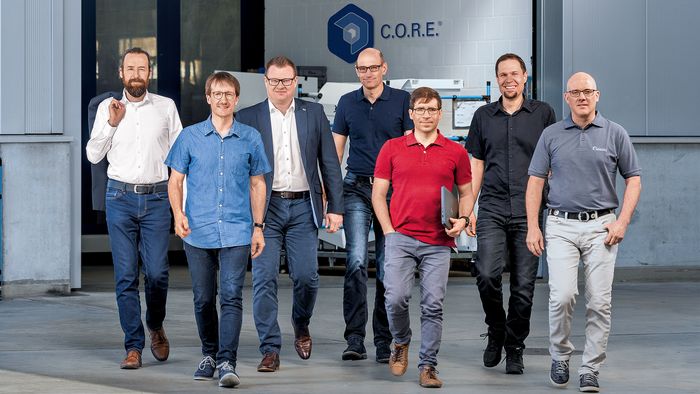
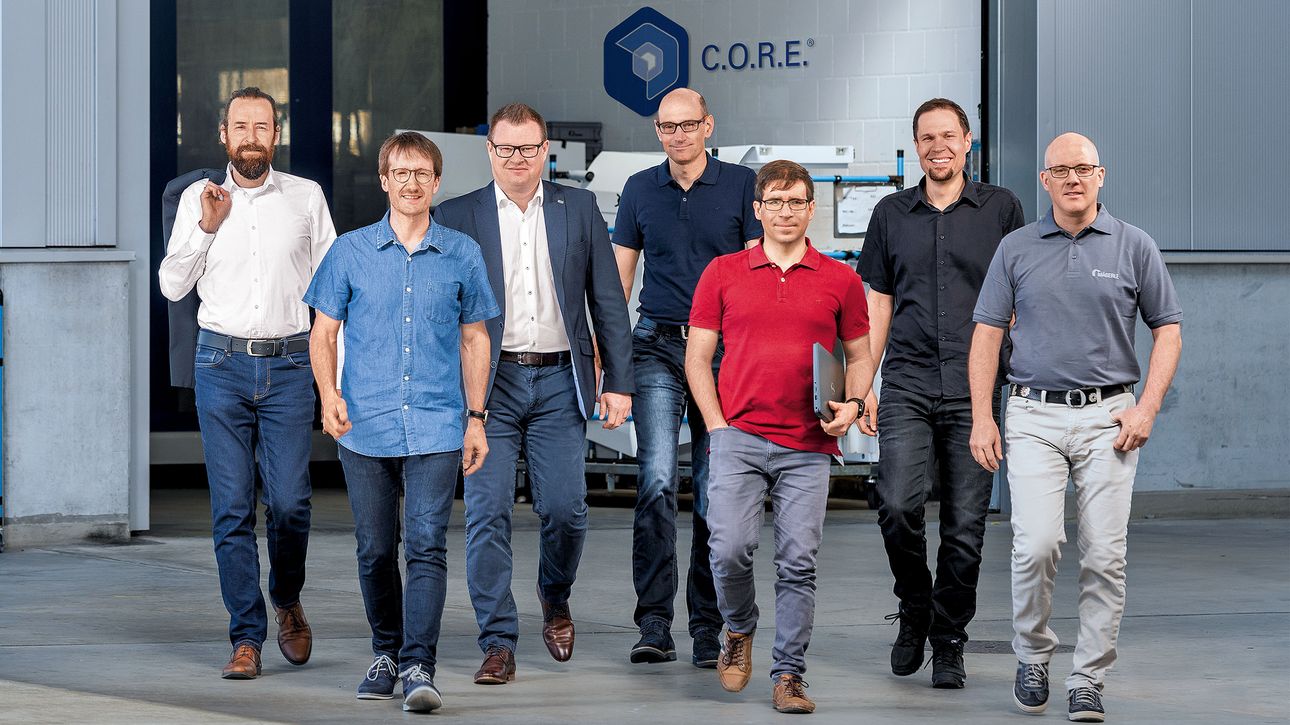
FINGERS QUICKLY GLIDE over the control panel of the grinding machine, access the job list, and activate the desired machining program on the next screen. What follows is, with the only physical touch of a button in the process, the program start. And the parameters of the current production cycle, from the spindle load display to the axis speed, are immediately displayed clearly on various tiles.
The new multi-touch panel is the visible element of the C.O.R.E. program of the UNITED GRINDING Group. C.O.R.E. does not only refer to the core of the machine itself. It is also an acronym for Customer Oriented REvolution. Or, as Marcus Köhnlein, Head of Digital Business, puts it: “C.O.R.E. is the future of software.” Does this make sense? No? Then let‘s start from the beginning.
Project start 2015
“C.O.R.E. dates back to 2015,” says Christoph Plüss. The Chief Technology Officer is the driving force behind the project. As Industry 4.0 became more and more popular in public debate, the question arose as to how the corporate group intends to deal withit. “That was easy to answer at first: definitely together.” That is how the idea of a groupwide operating system came about, following the uniform machine design introduced in 2013.
Developing a machine operating system together with eight company brands from two countries and three different technology groups was a complex process that occupied the group of companies for several years. Before the Corona year 2020 slowed down the development, the brand and multi-country teams had been working 2019 very intensively on C.O.R.E. using the agile Scrum method. “A significant part of the research and development budget went into the project that year,” explains Plüss.
Sharing the burden
Teamwork between the brands was not only a challenge, but also an opportunity. “Nowadays it is hardly possible for a company to develop software on its own – except for large corporations,” emphasizes Stefan Aebi, Head of Software Development at EWAG and the project's Scrum Master. “With C.O.R.E. we are dividing this task between all the brands, and everyone benefits.” And after machines were presented for the first time at EMO 2019 in Hanover, which delivered data to a central data hub via the umati interface – a preliminary stage to C.O.R.E., the first next-generation machines with C.O.R.E. will now be presented at the upcoming metalworking trade show 2021 in Milan.
These machines are externally recognizable by a C.O.R.E. sticker and the new control panel. The 24-inch full-HD multi-touch display is not only an eye-catcher, but also a major innovation itself. “Much more than a classic operating unit, it is an intelligent, clear command center for the respective operator,” explains Christian Josi, who is responsible for hardware. “This will prepare us for the digital natives,” emphasizes Marcus Köhnlein. The intuitive design of the elements and the almost exclusive operation via touch represent a completely new way of controlling the machines. “The operating experience is state-of-the-art, I can practically operate the machine like a smartphone,” adds Christoph Plüss. The CTO also sees this as a necessary investment in the future: “The next generation of machine operators, are our children.” And they grow up with smart devices.
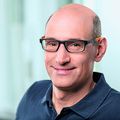
Sustainably expandable
Orientation towards the operator’s experience was always at the forefront of development. Feedback was provided by customers and their own application engineers. “The user experience was central from the start, everything else was secondary to it,” explains Michael Schwitter, Application Engineer at STUDER and Project Architect at C.O.R.E. In addition to the control element, a high-performance industrial PC is the other hardware component. This local digital platform expands the classic IT (Information Technology) to the OT (Operational Technology) and establishes a secure connection from the customer’s network to the inner workings of the machine.
In the background of the pure operating software, a so-called middleware runs on the PC, which establishes the connection to the existing applications that are still working in the background. “In the subsequent releases, we will then standardize these between all brands,” says Köhnlein. And at the very bottom of the software architecture, the individual machine controls run, depending on the Siemens or Fanuc brand.
This phased structure not only enabled a release at this point in time. “Flexible and sustainable expandability is also a great advantage. New features will be added on an ongoing basis,” explains Christian Josi, Head of Digital Engineering at UNITED GRINDING Group.
Stored roles
User roles are stored in the operating software, according to which the panel is individually configured: machine operators, setters, maintenance personnel, service technicians. The machine operator, for example, then only sees the processing programs, the maintenance personnel sees the diagnostic programs. This reduces complexity for the individual, simplifies handling, and thus reduces the susceptibility to errors.
In addition to the new operating experience, C.O.R.E. introduces many other advantages. The training costs are reduced – anyone who can operate a machine from the UNITED GRINDING Group can also operate all others. This even helps to counteract the growing shortage of specialists.
The same applies to the application service. “If the customer needs support with software maintenance, the brand makes no difference,” summarizes Joel Amstutz, Software Developer at MÄGERLE.
In addition, the standardized hardware helps to reduce the number of spare parts required. The UNITED GRINDING Group also offers numerous advantages: “We have an easier-to-maintain system here,” explains Marcus Köhnlein, “and we can respond more quickly to customer requirements during development.”
All C.O.R.E. machines are equipped with umati interfaces. This improved connectivity – also with third-party machines – in turn opens up a wealth of optimization possibilities by means of more efficiency in the process and more transparency in production. Comprehensive predictive maintenance is also possible. This means that planned maintenance and repairs can be carried out, where the spare parts are already available and you don‘t have to wait long for them.
And of course, UNITED GRINDING Digital Solutions™, such as the Production Monitor or the Service Monitor, can also be easily integrated.
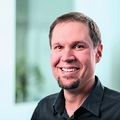
New releases every year
From EMO 2021, C.O.R.E. will first of all be launched with basic functionalities. “This will create a basis that we will build on in the future,” explains Köhnlein about the vision of C.O.R.E. “Development continues steadily, there are always new releases.” These are also developed on the basis of customer feedback.
When it comes to the other digital possibilities that C.O.R.E. offered, CTO Christoph Plüss and Head of Digital Business Marcus Köhnlein rave about it. The possibilities range from camera-supported facial recognition, which identifies people on the machine and automatically sets their role in the system, to further support in the cooperation between man and machine, the so-called Human Machine Teaming. Artificial intelligence in the machine could enable features such as a virtual assistant or a self-optimizing machine, in which the system itself takes over operation and maintenance support, as well as process control tasks.
“And the central interface to the customer could be a customer portal,” outlines Plüss. Not only could this be used to record and maintain the master data of the machines. An app store could also be integrated to allow customers to easily download updates or upgrades without wasting time. With the next version of C.O.R.E. it probably doesn't exist yet, but there are still several releases to follow. “Our journey”, emphasizes the CTO, “has just begun.”
Benefits of C.O.R.E.
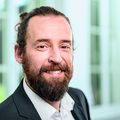