BLOHM Case Study - Rolls-Royce Oberursel
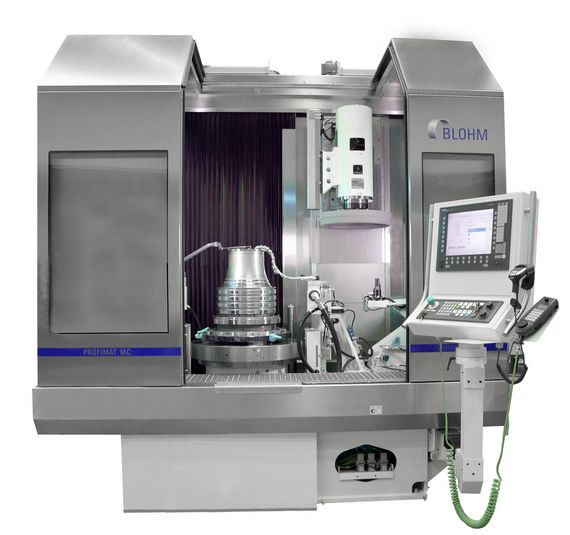
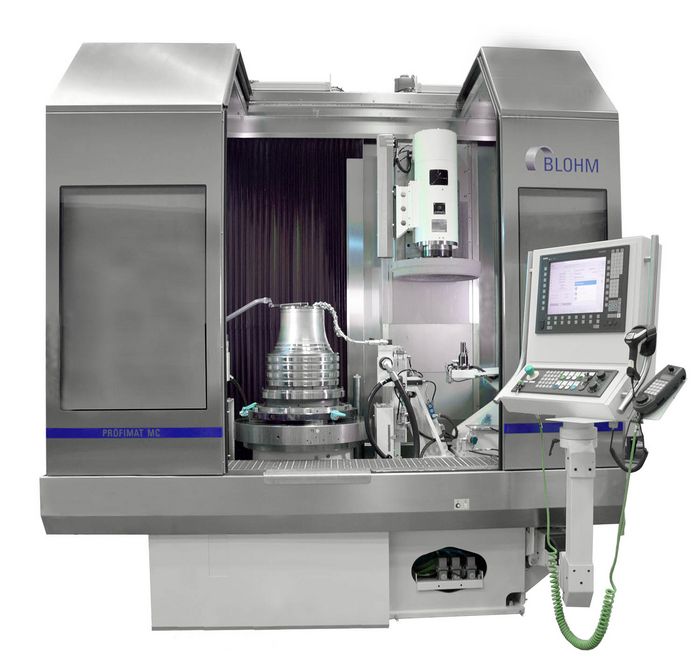
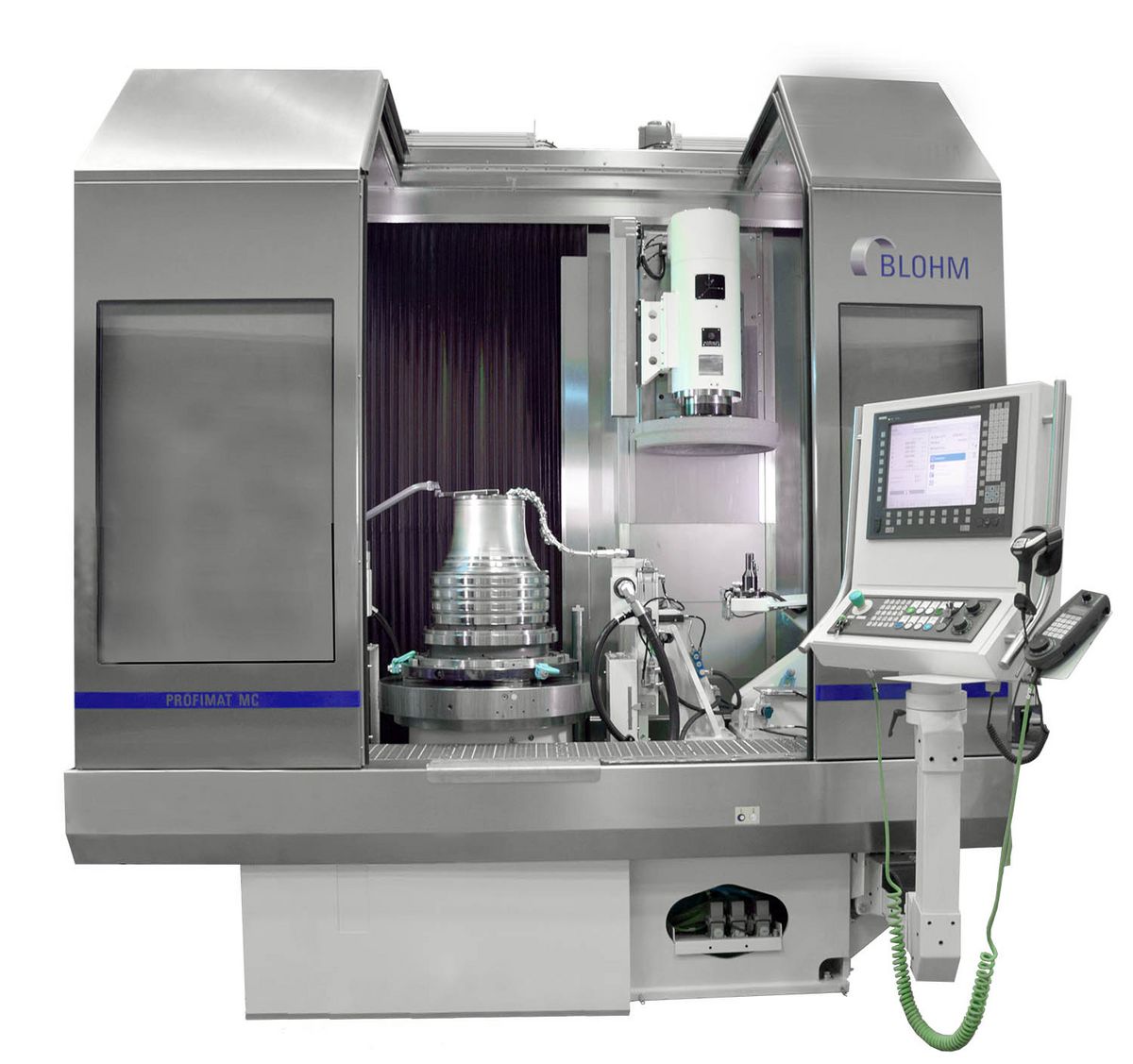
BLOHM PROFIMAT MC 610 VS Cuts Auxiliary Times by Half
Christoph Fedler, Project Director for Equipment Management at Rolls-Royce Germany, was facing a challenge: He needed to increase the available capacity of the prime discipline at the Oberursel facility, namely micrometer-precise grinding of Curvic couplings.
Rolls-Royce, active in the fields of "Civil Aviation," "Defense" and "Power Systems", employs roughly 10,000 employees at 11 locations in Germany. For Mr. Fedler's field, "Civil Aviation," the company is the largest producer of motors for large-scale airplanes, such as those from Boeing or Airbus. Aviation is an enormous growth market for Rolls-Royce, with order books full for the coming years. Rolls-Royce thus is under pressure to boost productivity, such as through investments in new technology.
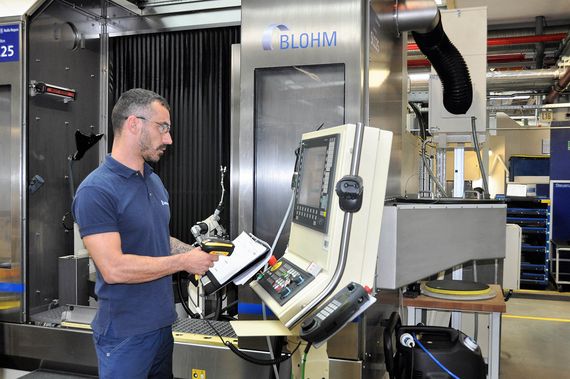
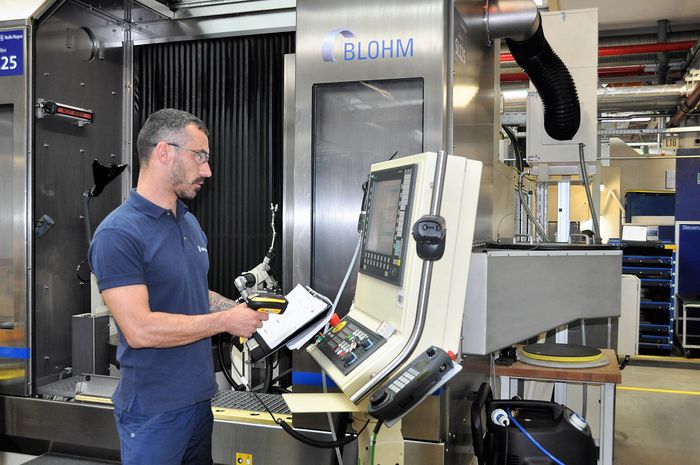
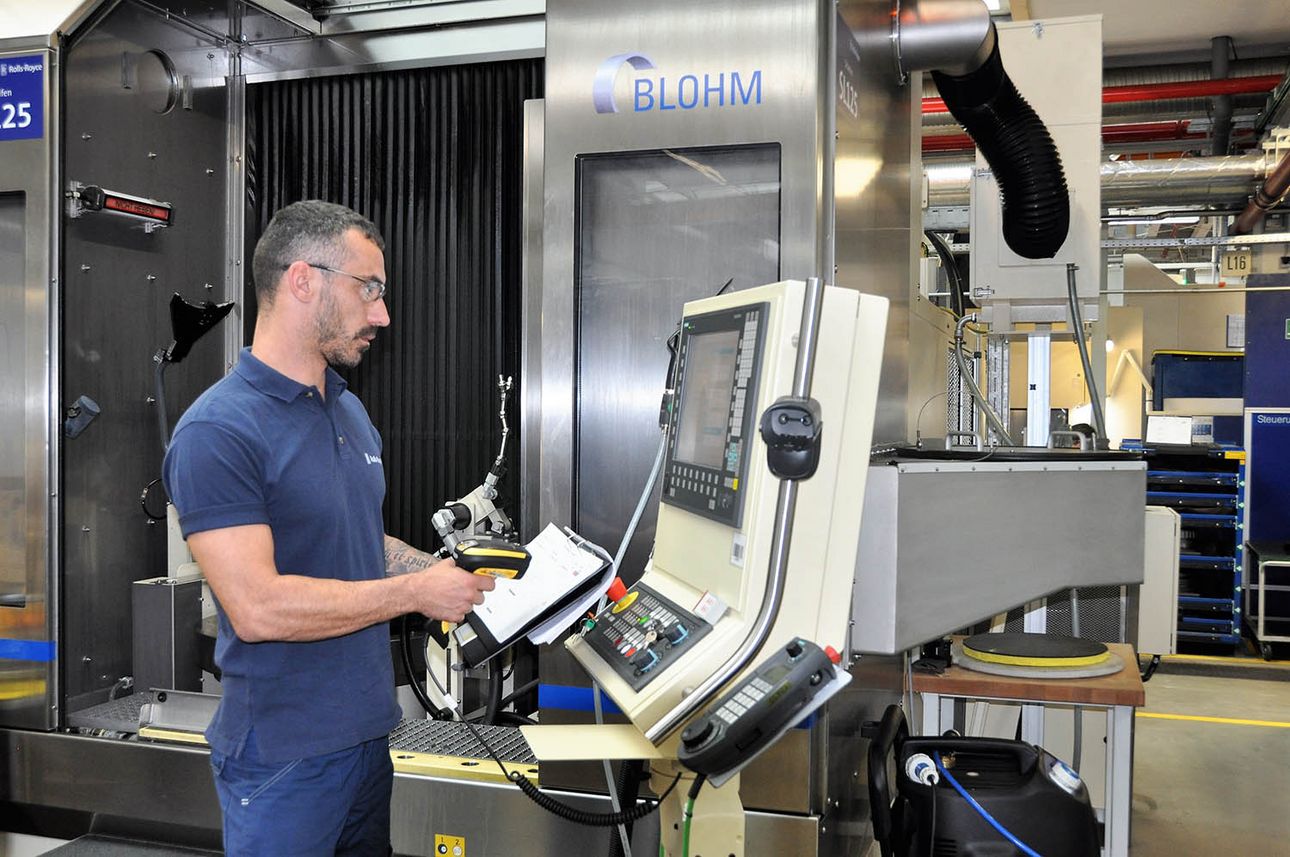
Diverse Requirements
Rolls-Royce identified five primary criteria for any new grinding machine: 1. Extreme production precision. 2. Repeatability and therefore process stability. After all, the drum on which the Curvic Coupling is ground is itself already manufactured to high level of precision. 3. The newly acquired grinding machine would need to demonstrate high technical availability. 4. The process would need to involve a change from oil to an emulsion-based cooling agent. 5. Simplification and associated time savings in preparing workpieces through use of a customer-specific upgrade station.
Complex project
In the first quarter of 2015, the team under Christoph Fedler gathered together the specifications for the new grinding machine. Over the course of one year, Rolls-Royce evaluated several suppliers and conducted technical/technological discussions. The contract was ultimately awarded to Blohm Jung GmbH in Hamburg and its BLOHM PROFIMAT MC 610VS. "The PROFIMAT is working at tolerance range a grade above that of the competition. Our experience with an existing BLOHM PROFIMAT MC also plays a very important role. It has been a reliable and precise worker for over ten years," says Christoph Fedler of the decision. Another year world pass until the BLOHM PROFIMAT MC was ready for commissioning. "It was a complex project with difficult requirements and the need to make many changes during the project management phase. The project management team at BLOHM always responded quickly and presented solutions, even if they were demanding," says Christopher Boll, Director of Equipment Management at Rolls-Royce. The new BLOHM PROFIMAT MC 610 VS went online shortly before the end of 2017 and from the start delivered positive results.
50% reduction in auxiliary times
For Rolls-Royce, the investment in the BLOHM PROFIMAT MC 610 VS has been more than worthwhile. "We have been able to reduce the auxiliary times by up to 50%," says Michael Lange, a components planner at Rolls-Royce. Thanks to this massive reduction, workpieces from other machines can now be handled by the new grinding machine from BLOHM as well. The new PROFIMAT MC has not only replaced the previous machine, but further expanded the available capacity as well. What other benefits did the machine bring? It is much easier to operate. This includes, for example, the customer-specific set-up unit. It allows the operator to begin preparing a new component outside the machine while a different workpiece is still being machined inside. The measuring probe
offers an enormous boost to process safety, as it measures based on pre-defined quality parameter while grinding is still ongoing.The data is sent online to the Rolls Royce quality assurance program. In addition, the PROFIMAT MC allows for the grinding of master parts. This means it is capable of producing workpieces of extraordinary precision that are then used as measuring means by the Production team.
The BLOHM PROFIMAT MC 610 VS
The PROFIMAT MC is a powerful grinding centre. This extremely compact traveling-column machine offers everything that modern production solutions require, with a machine width of just 2400 mm. Different spindle variants enable diverse applications. The five-axis CNC profile grinding machines in the series can optionally be equipped with a horizontal spindle for drive capacities up to 60 kW as well as a stationary or an NC-swiveling vertical spindle with grinding spindle speeds of up to 60,000 revolutions per minute. The traveling-column machine is suitable for both conventional grinding tasks and for CD, IPD and all CBN methods.
Customer-specific adaptation
The performance of the vertical spindle was adjusted to the customer's needs. In order to better control the Z-axis, BLOHM also installed two gantry drives. Specially for Rolls-Royce, the PROFIMAT MC was equipped with a 0-point tensioning system with four mold cavities. The machine's rotary table has a diameter of 800 mm. The stainless steel working space was extended laterally for the grinding wheel changing tool, making it easier to replace the cup wheel from the working space of the machine. Another new feature: The set-up station is also equipped with a rotary table outside the machine that is identical to the rotary table inside the machine. The workpiece is clamped on the rotary table and fixed directly on the 0 point tensioning system using the base plate. The operator can then rotate the rotary table and measure the workpiece to the desired tolerance in terms of the circular and axial run-out. The clamped workpiece is then inserted into the machine with the base plate and the grinding process can be started.
To further enhance quality, the shape of the coolant nozzles was customized and can also move into a vertical position (C axis). This ensures the workpieces are optimally cooled.
"One particular challenge posed on Blohm Jung GmbH was the vertical dressing unit. That was no easy task for their designers," Christoph Fedler says with admiration. The original machine is designed to handle a grinding wheel diameter of 400 mm. Rolls-Royce however needed a grinding wheel diameter of up to 560 mm. The cup wheel must be able to move into dressing as well as replacement position. Space for all these steps within the machinery space is extremely tight. "Our designers have really delivered a great deal of performance here," confirms Ulrich Haar, Project Manager at Blohm Jung GmbH.
Software
The user interface for the BLOHM software is based on Siemens 840 D Solution Line. The interface, which has been specifically adapted to the needs of Curvic grinding, is self explanatory and the operator can work intuitively. "The software is modular and clear," confirms Christoph Weber, team leader at Rolls-Royce. "That software is also our insurance: if the operator makes a false measurement or input, the software immediately recognizes this and gives an error message." He is also enthusiastic about the hand reader. It can read the barcode on each component, calling up the corresponding NC data automatically in the software so that the proper grinding parameters can be applied.
Always room to improve
"The machine is fantastic! The service is fantastic," says Christoph Weber succinctly. But nothing good comes easily: The machine was scheduled to be transported from Hamburg to Oberursel by special heavyweight truck. The permit for heavy transport did not come through in a timely manner, even though the old machine had already been dismantled. It was an external factor, but an impactful one nevertheless. Thankfully, the super-productive BLOHM PROFIMAT MC 610 VS quickly resolved the backlog once it was up and running.
With the first set of performance data already gathered from the new machine, it is time for optimization. The grinding wheel currently requires an excessive amount of dressing, a problem that will likely be solved by installing a grinding wheel with different specifications. Beyond this, the set-up station will also be simplified: "We've enjoyed the dedicated support from the BLOHM team and appreciate their innovative and respectful cooperation," Christoph Fedler commented.
About Rolls-Royce
Rolls-Royce is a world leader in drive systems and in Germany with its civil aerospace, defense and power systems businesses.
Germany has the second largest workforce in the Group, behind only the UK, with more than 10,000 employees in 11 locations. Rolls-Royce Germany has been present with its own sites since 1990 and is active in the aviation industry. Since August 2014, Rolls-Royce Power Systems has been a fully owned subsidiary of Rolls-Royce. The historical German company, based in Friedrichshafen, was previously called Tognum and supplies large motors, drive systems and decentralized energy installations.
www.rolls-royce.com
About Blohm Jung GmbH
Grinding machines from the brands BLOHM and JUNG have been used worldwide for decades, wherever productivity, performance and precision are required. They are developed in Hamburg and produced in a modern manufacturing facility to high quality standards. More than 15,000 delivered machines reflect the international recognition of the BLOHM and JUNG brands. It has gathered a remarkable trove of experience gained in the specialized fields of flat and profile grinding. Its range includes both standard machines for flat and profile grinding for individual and small-batch manufacturing as well as production machines that are adjusted customer-specific. The Blohm Jung GmbH is a part of UNITED GRINDING Group with its own subsidiaries for international markets in India, China, Russia and the USA .
www.blohmjung.com
UNITED GRINDING Group
With a turnover of around 700 million euros, the UNITED GRINDING Group is one of the world's leading manufacturers of precision machines for grinding, eroding, lasering, measuring and combination machining. With its eight company brands MÄGERLE, BLOHM, JUNG, STUDER, SCHAUDT, MIKROSA, WALTER and EWAG, UNITED GRINDING offers a broad application knowledge, an extensive product portfolio and a complete array of services for the international market. The Group employs around 2,500 employees and has more than 20 production, service and sales locations and sales/service agencies worldwide.
www.grinding.ch