Italian excellence in lasered PCD tools
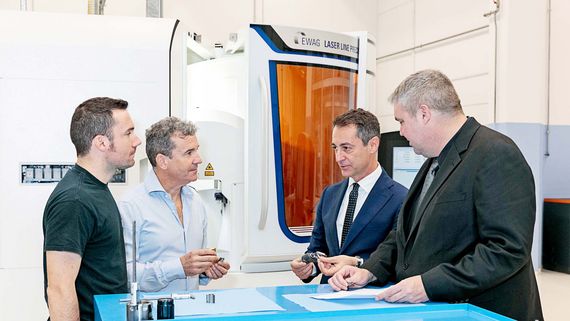
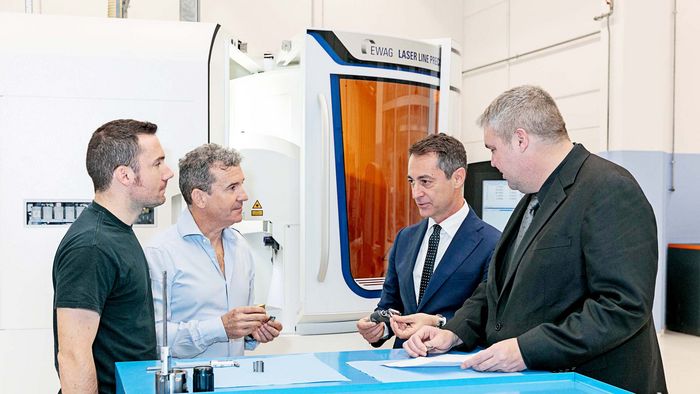
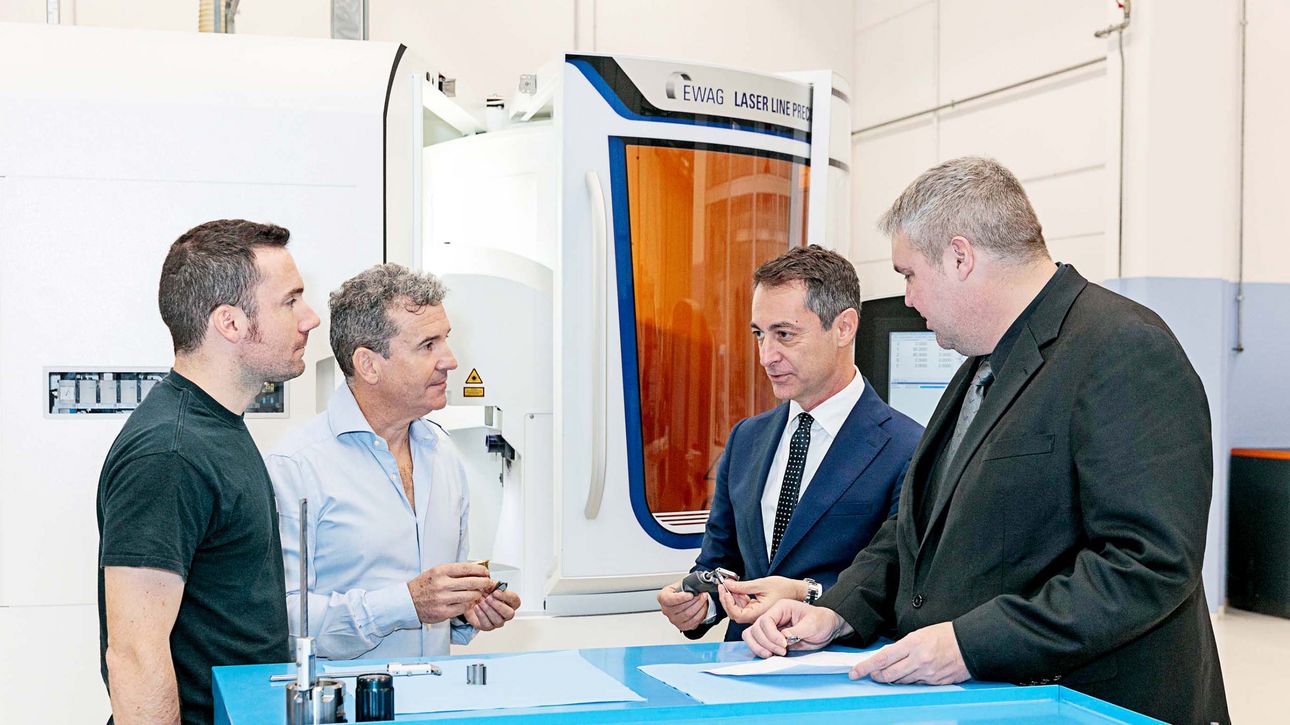
The company MICTU srl is located in Quero Vas, a town in northern Italy. Founded in 1986 by Antonello Collavo, MICTU counts today 14 employees. Their main focus is the eyewear, dental, aerospace and automotive industry. The extensive knowledge in manufacturing of tools using various manufacturing technologies got extended by laser technology, when a LASER LINE PRECISION machine from EWAG was installed.
Tool production
Especially for ultrahard materials, such as polycrystalline diamond (PCD) or chemical vapor deposited diamond (CVD-D) materials laser technology complements the tool range by flexibility in tool design, programming and fast lead times from design to production. Compared to other technologies e.g. grinding the low need of consumables such as grinding wheels, coolant, etc. gives the company a striking advantage.
MICTU’s tool range manufactured using laser technology consists mainly of form tools in a diameter range of 3 to 60 mm. Also special focus is placed on complex geometries (e.g. con-cave profiles) for eyewear industry, as depicted in the following images.
Laser technology enables the operator to cut, shape and even bring diamond to the desired form just by sending out a fine focused ray of light. In grinding wheels and coolant; in erosion wire and dielectric liquid needs to be provided to the machine. This enables MICTU to operate the machine multiple weeks by simply adding a new blank after a customer tool is finished. In addition, very short setup times can be realized, programming can be executed on a separate computer and the necessary files can be quickly transferred to the machine, minimizing the downtime between jobs. Therefore, small batch sizes are easily realized using laser technology.
The machining operator manages to program a tool in approximately 10 to 20minutes and produces the tool in another 10 to 20 minutes. This is realized by designing the tools in a perfect way for laser production and eliminating any unnecessary processing steps. Production times can be cut in half, while enhancing cutting edge quality, e.g. in roughness by a factor of three leading to better products for MICTU’s customers leading to a strong competitive advantage on the market. Tool design was adapted for optimal laser beam accessibility with respect to the tool body, in order to access the cutting edge in an ideal way. In terms of PCD grit size, MICTU is currently developing strategies to produce tools using larger diamond grains for higher tool lifetime. EWAG’s software LaserSoft integrated tool for automatic 3D model generation based on a simple DXF curve of the tool without modelling axial or radial angles is great, but usually MICTU’s operators prefer to work directly in 3D in order to give the tool the desired shape.
Think LASER!
The benefits of laser technology in tool manufacturing are demonstrated by MICTU’s excellence and knowledge in tool design and quick adaptability for novel tool manufacturing processes. Still new features, shapes and geometries are to be tested and long-time analysis of customer’s feedback is still to be awaited but the quality, ease of programming and fast lead times from design to manufacturing render the LASER LINE PRECISION by EWAG ideal for today’s and the future market in cutting tools.