Micro Cutting Tool Solutions for the Electronics Industry
Historically, sectors such as the electronics, medical and micromechanics industries have been pioneers in the area of miniaturisation. In the electronics industry, consumer goods such as flat screen TVs, wearables, mobile phones, drones and laptops are continuously being developed to be thinner, lightweight and energy efficient. With our LASER LINE ULTRA, we meet the demands of the electronics industry.
This machine specialises in the laser fabrication of cutting tools made of hard and ultrahard materials such as tungsten carbide (WC), polycrystalline diamond (PCD), chemical vapour deposition diamond (CVD-D) and cubic boron nitride (CBN). The capabilities of the machine includes cutting edge preparation, post-sharpening, fabrication of chip breakers and cylindrical margins as well as laser-modification of ground cutting tools.
Owing to its 8-axis kinematic concept and the use of an industrial laser source emitting pulses in the picosecond time regime, complex micro geometries can be machined. The following two examples prove this claim include cutting tools made by the EWAG Drill and Mill Module software options of the company's proprietary LaserSoft software.
Spiral Tools
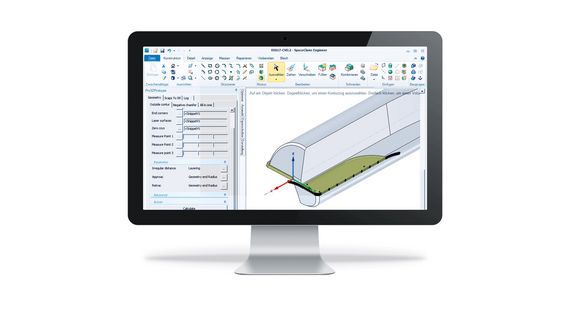
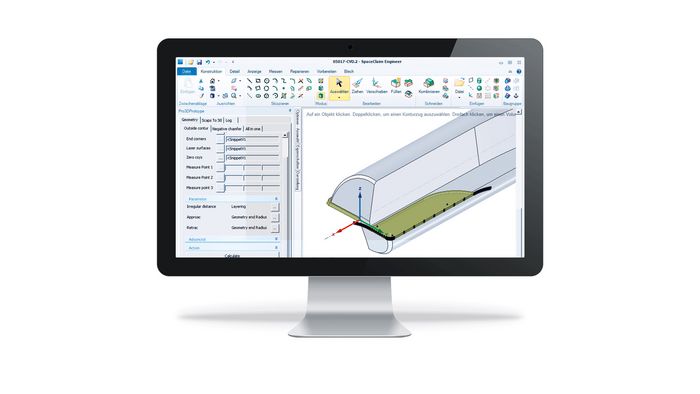
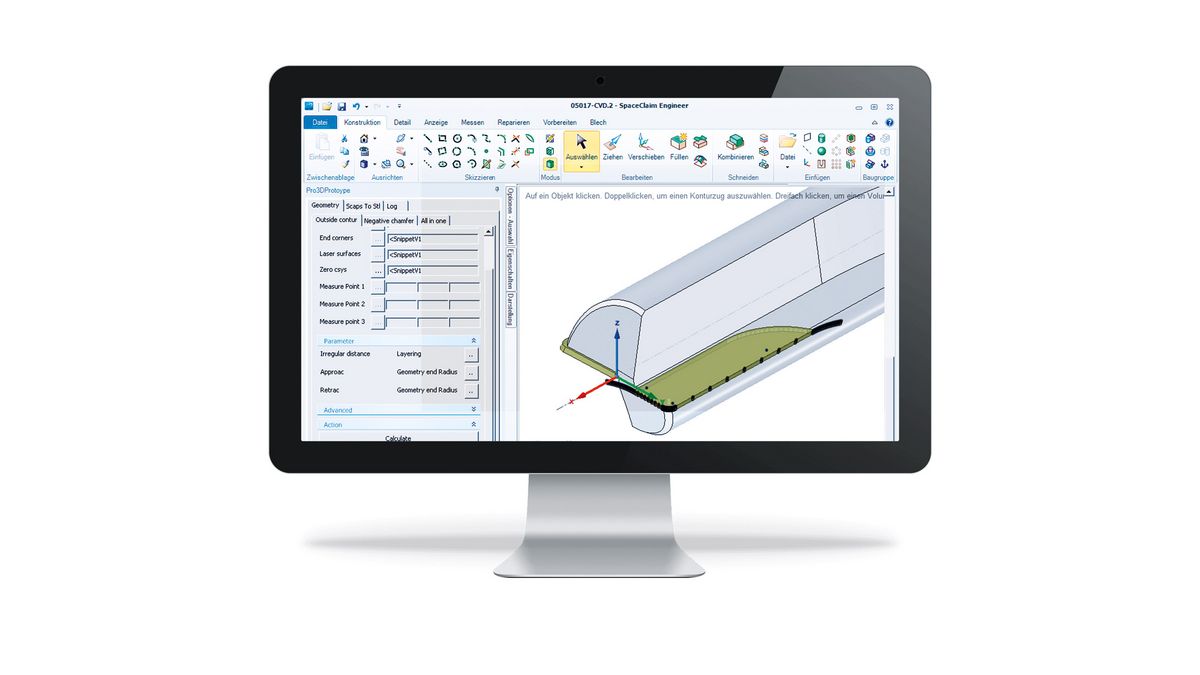
The EWAG Drill and Mill modules are software options which enables users of the LASER LINE ULTRA to fabricate spiral tools made of WC or PCD between Ø 0.4mm to Ø 3mm. Analog to TOOL STUDIO from our sister company Walter Maschinenbau GmbH in Tübingen, Germany, programming is parametric and recommended laser processing parameters are automatically determined enabling a significant ease of programming.
Micro Drill Bits
Applications of micro drill bits are manifold and include the drilling of gallium- or silicon-based wafers, sintered ceramic components, or multilayer composite printed circuit boards (PCBs). Since the electronics industry demands stringent wear-resistance to ensure homogenous hole quality, micro cutting tools made out of ultrahard materials is a must. By using ultrashort laser pulses and the EWAG Drill Module, the LASER LINE ULTRA can achieve this task with ease. The shown example below depicts a micro drill bit made out of a carbide body and a PCD tip which is completely lasered from a cylindrical blank.
The advantages of using laser technology compared to conventional techniques especially for micro cutting tools include:
- Diameter to length aspect ratios of up to 1:20
- Ability to process additional small features such as the tip thinning
- Owing to the force-free process, no waste from tool breakage occurs and no steady-rest support is necessary
- High degree of geometrical flexibility since brazed plate-based PCD tools and PCD spiral tools can be fabricated without any retooling
Laser processing removes material according to thermal-based mechanisms. However, by using ultrashort laser pulses and correct laser parameters, a phenomenon arises in which the pulse is so short that there is insufficient time for a significant amount of heat to conduct into the cutting tool. As a result, there is a negligible heat-affected zone. To prove this claim and to further demonstrate the flexibility of the LASER LINE ULTRA, carbide drill bits are laser-fabricated and are subsequently coated by the physical vapour deposition (PVD) process with a single layer of either a TiAlN- or an AlTiN-alloy. During PVD coating, the processing chain and processing recipe were not adapted, i.e. laser-fabricated cutting tools are treated equally to ground cutting tools. Results depicting the evolution of the micro drill bit, from a cylindrical blank to a coated micro drill bit are shown in the following image.
1.) Ø 0.5mm carbide blank
2.) Ø 0.45mm carbide drill bit after laser processing
3.) carbide drill bit after AlTiN-coating
4.) carbide drill bit after TiAlN-coating
EWAG has studied extensively the coatability of laser processed micro cutting tools and has worked closely with two of Switzerland’s biggest surface technology companies to ensure successful coating. To confirm that coating adhesion is comparable to ground tools, measurement methods such as optical microscopy, scanning electron microscopy, energy-dispersive x-ray spectroscopy, hardness indentation tests and destructive break tests were all used.
Micro End Mills
Applications of micro end mills are manifold and include profiling of PCBs, milling of enclosures such as mobile phone cases as well as the fabrication of moulds and dies for injection moulding. By using the EWAG Mill Module, the LASER LINE ULTRA is able to fabricate 4-flute PCD end mills from cylindrical blanks as depicted in the images below. Primary and secondary clearance faces are fabricated both at the tip and circumference, the corners at the edges are broken by a chamfer, and with all lasered spiral tools, a smooth uninterrupted interface between PCD-WC is observed.
Quality of Spiral Micro Tools
An important quantity which defines the quality and chip evacuation performance of spiral tools is the surface quality of the helix flute. In this case, white light interferometry and a 20x 0.4NA objective lens measure the surface roughness of the helix flute. Interestingly to notice, the lasered surfaces are homogenous and do not show any form of periodicity or directionality compared to the ground surface. Furthermore, the surface quality of the lasered WC surfaces is 20 % better than the ground WC drill bit. For lasered PCD surfaces, an excellent surface quality is also achieved, however, results are typically not comparable to that of WC. In general, lasered spiral tool surfaces, regardless of material, exhibit surface roughness values for Ra and Rz of <0.25µm and <1.5µm respectively. Additionally, cutting edge radii are typically ≤5µm and are symmetric with a K-factor typically equal to 1±0.2.
The LASER LINE ULTRA provides an excellent basis to fabricate complex micro cutting tool geometries independent of their hardness and with negligible heat-affected zone. The presented examples would otherwise be difficult or impossible to fabricate by conventional manufacturing techniques or even nanosecond laser pulses. With continuous improvements to the laser process and software, EWAG is actively developing in areas such as the ability to process materials other than PCD or WC, additional spiral tool types and additional tool features.