After a record year in 2018, Fritz Studer AG reported another very successful year in 2019. With the third best annual turnover in the company's history, the cylindrical grinding machine manufacturer increased its market share again, despite difficult market conditions. One reason for its success is the high proportion of new customers, at almost 40%.
STUDER increases its market share again in 2019
Once again more than 60 journalists from all over the world made their way to the Bernese Oberland for the Motion Meeting. Under the motto "The Art of Grinding." the company presented some of the things that make it one of the leading manufacturers of cylindrical grinding machines. "This claim requires us to overcome limitations and focuses concentration on barely perceptible details which ultimately make the difference, in order to achieve what initially appears impossible. At times like these there is a special focus on the efficiency and quality of our processes and products", says Jens Bleher, CEO of Fritz Studer AG.
Sales & machine portfolio
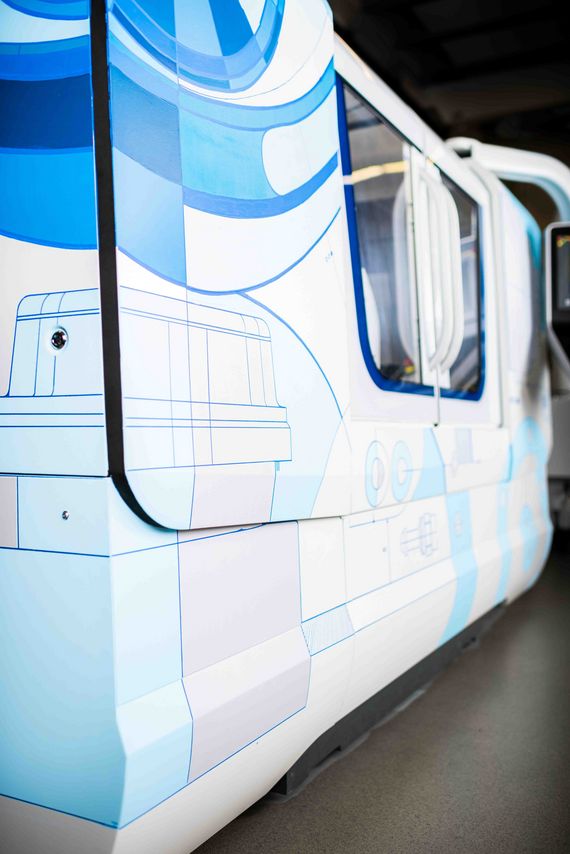
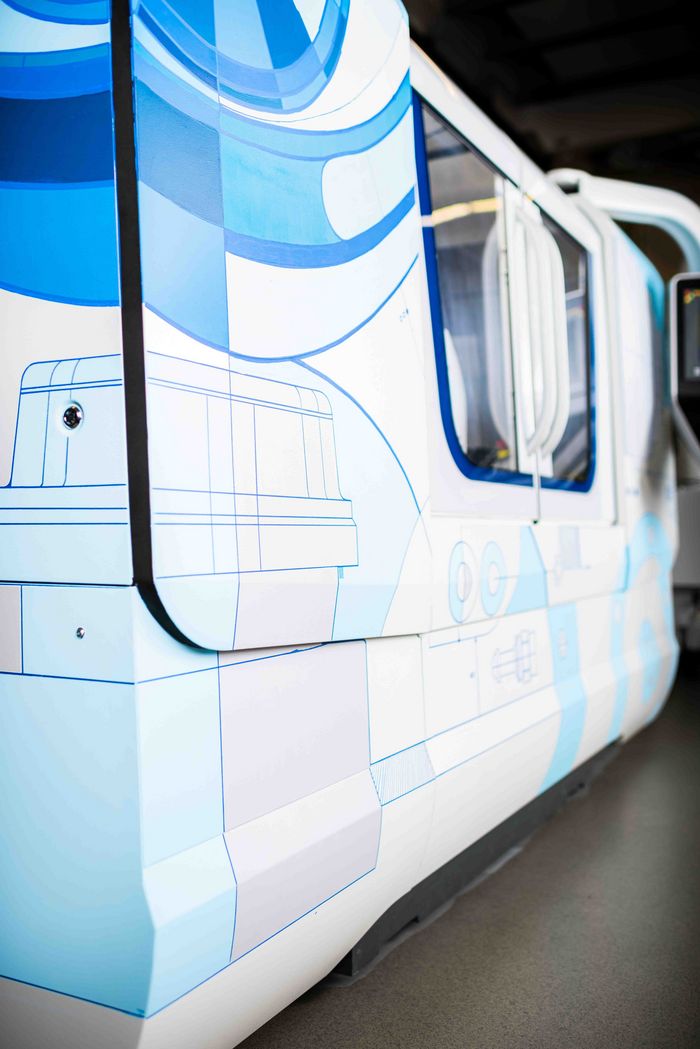
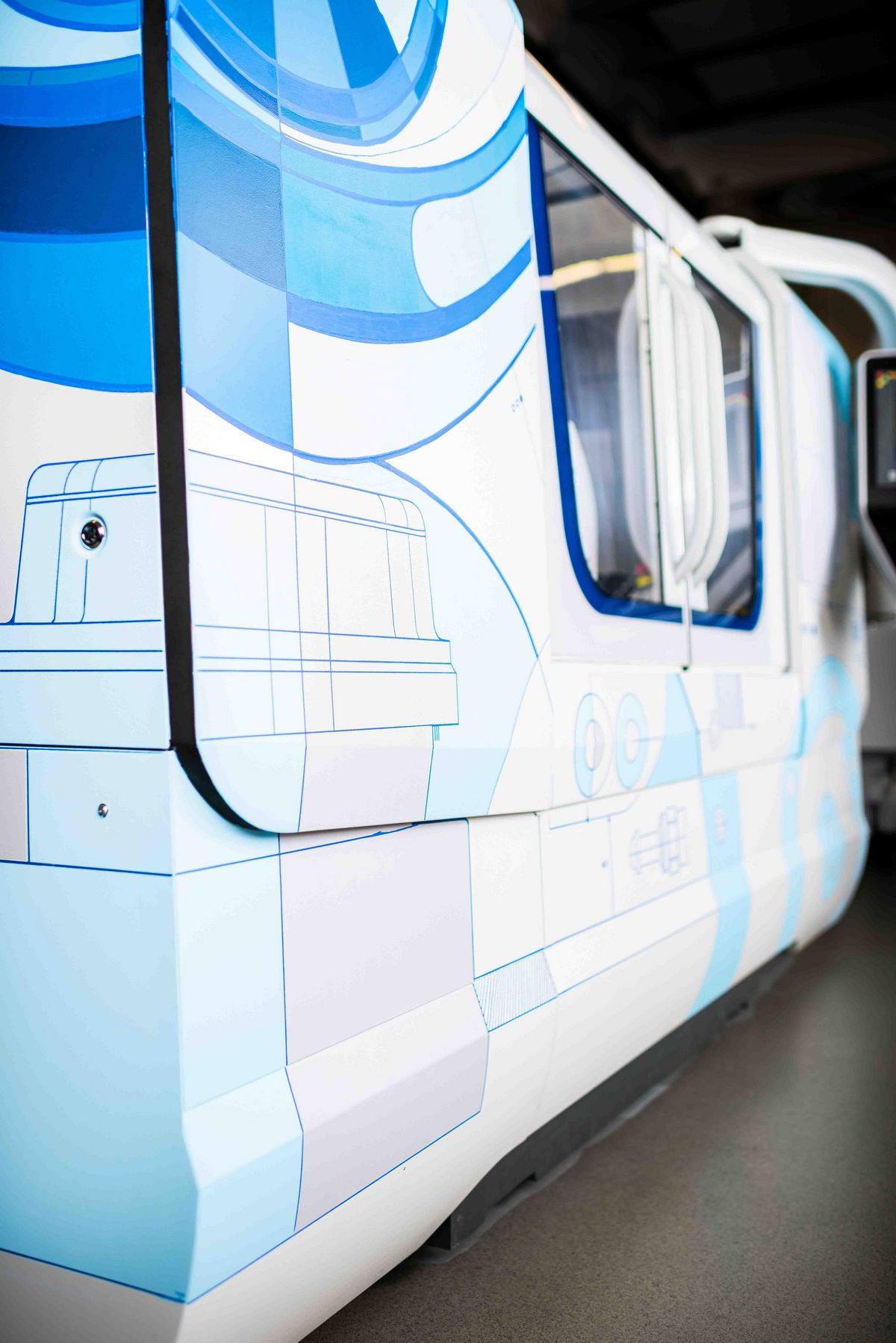
At the annual press conference Bleher reported a successful 2019, even if the economic situation has deteriorated significantly. "With the third best year in the company's history we were able to further increase our market shares", says Sandro Bottazzo, the company's CSO. STUDER recorded strong growth in North America in particular, where it achieved the second best result in the company's 100-year history. The company was also able to further increase its turnover with internal cylindrical grinding machines. "In the Asian region in particular we maintained incoming orders for internal cylindrical grinding machines at the high level of 2018", continues Bottazzo. Three machine types also achieved record incoming orders: the S121, the S141 and the S151, the flagship of internal cylindrical grinding machines. The new universal cylindrical grinding machines – the favorit, the S33 and the S31 – have also got off to a very successful start. "The launch of the new universal machines was both a feat of strength and a highlight", explains Bleher. The company didn't even need a year to sell around 100 of the new machines. Customers underscore the top quality and precision of the new machines. In America a longstanding STUDER customer, who had purchased a new S31, was delighted that he could achieve another increase in reliability and precision.
The customer segments developed very differently in 2019. In the automotive sector in particular, market conditions were much more challenging than in 2018. However, thanks to this broad diversification Fritz Studer AG was able to offset weaker market segments with stronger ones. For example, the aviation industry was one of the segments that flourished in 2019. "Our company has also been very well positioned in the aerospace customer segment for many years and is a preferred supplier of many component suppliers", explains Bottazzo, when reviewing the past year. STUDER sees one key to its success in its global customer-focused sales and service organization. This is also one of the reasons why the proportion of new customers was almost 40% last year. Smaller markets, like Great Britain, also achieved a very good order intake in 2019. Finally, the market share was also increased in the company's home market of Switzerland.
Customer Care
Customer Care was further developed in 2019 and the organizational changes initiated in 2018 and 2019 were successfully completed. Fritz Studer AG also increased its number of service technicians again. "In Italy and France in particular we were able to employ more new service technicians last year, enabling us to provide even quicker and more competent on-site support", explains Bottazzo.
Machine overhauls and maintenance achieved a new record turnover. Both service areas enjoyed a double-digit increase once again. Sandro Bottazzo adds: "Machine overhauls are an important business area for us and ideally complement our new machine business. This means that our customers can have the complete range, from new machine through to machine overhaul, from a single source".
Exciting times for technology
2019 was also very exciting for STUDER's system division. Various new projects have been started, advanced and completed. For example, thanks to STUDER WireDress® it was possible to reduce the cycle time for an application from the medical sector by a whole 70%. A life cycle solution project was carried out in Biel, in which ceramic components for use in mass spectrometers were form-ground with high precision in several grinding trials with the customer.
"You can expect a new product from the STUDER company in a few months", promises Daniel Huber, CTO at Fritz Studer AG. This is a new hydraulic synchronous tailstock. "The hydraulics of the redesigned synchronous tailstock have been replaced by a servo drive with an electrical clamping function. The repeatability and accuracy of the clamping force have been increased to the exact gram. An even lower contact pressure can now also be selected", continues Huber.
The digital world of the UNITED GRINDING Group
Four fundamental priorities for the Group's digitalization strategy have been developed from a wide range of digital projects. "Connectivity, Usability, Monitoring and Productivity. These are the digital pillars of UNITED GRINDING Digital SolutionsTM", explains Huber. In the area of Connectivity, the umati standardized communication interface provides the long awaited possibility of simply connecting any machine, which is umati-capable, to the Production Monitor and monitoring its operating status. "Digitalization is also finding its way into production. As a user of our own machines we are the internal customer, so to speak, and support our developers with practical tests and suggestions for product improvements from the user's point of view", explains Stephan Stoll, COO of Fritz Studer AG.
Investments in the future
Further significant investments were also made at the Steffisburg location in 2019, underlining the commitment of the UNITED GRINDING Group to Switzerland as a workplace. A major project for modernization of the company's cubic production was successfully completed last year. "Technically harmonized milling centres allow automated, high-precision manufacturing of our key components", says Stephan Stoll. A further investment was also made in component production and implemented this year. This concerns the complete production of spindle shafts – a key component for the function and precision of the grinding machines. "We also want to maintain and develop our expertise and efficiency here and increase our internal value added. Naturally we will continue to use the latest production and process technology and a reasonable degree of automation", explains Stoll.
Further smart factory projects
Tool management in component production has also been updated. The entire life cycle of a tool is now digitally controlled and monitored. Each tool component has a digital marking by means of a chip or smart code and can be allocated to a preparation process, an order or a machine. The control cabinet design and assembly process chain also holds potential, which can be optimized with digital support. With the use of digital tools, the entire process chain from electrical engineering through to the assembly of a control cabinet can be carried out efficiently and partially automated. "Finally, digitalization is also finding its way into assembly", says Stoll.
Instead of using outdated drawings, the assembler drags the most recent data as a 3D representation directly onto the screen at the workstation and has optimal working documents. Via a chat function the employee can easily send questions and ideas for improvement to the relevant engineering department and create a short and direct feedback loop.
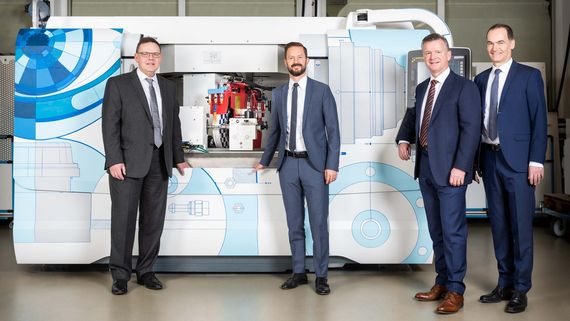
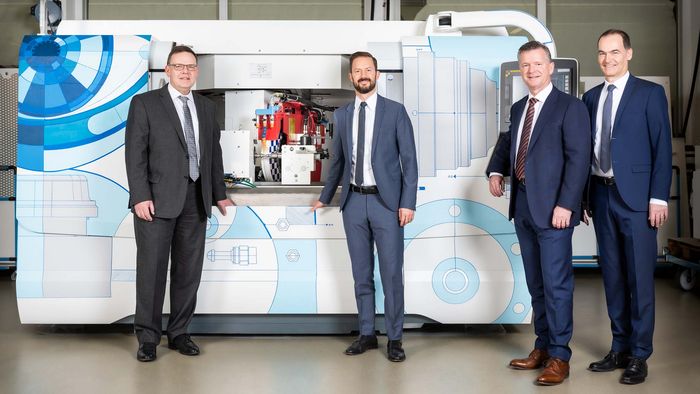
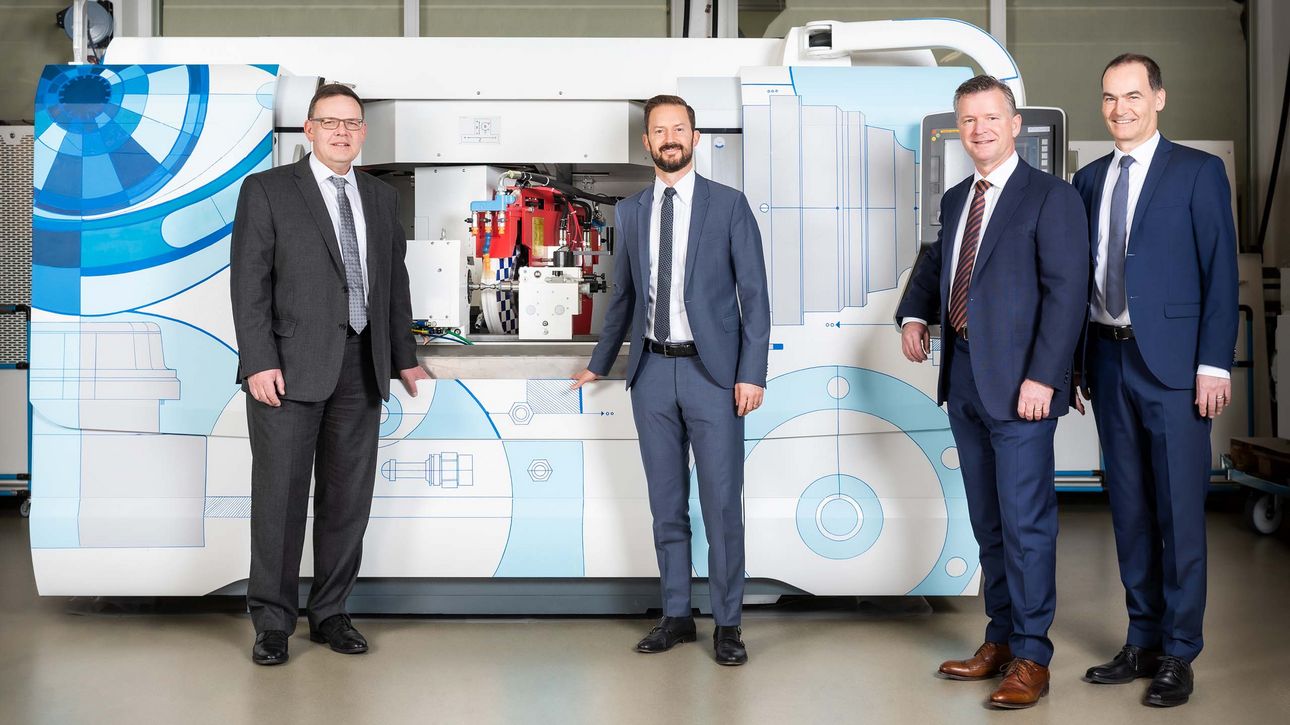
Stephan Stoll (COO), Sandro Bottazzo (CSO), Daniel Huber (CTO) and Jens Bleher (CEO)