JUSQU’AU MOIS DE MARS
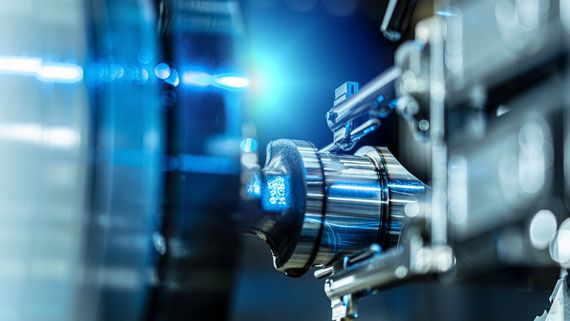
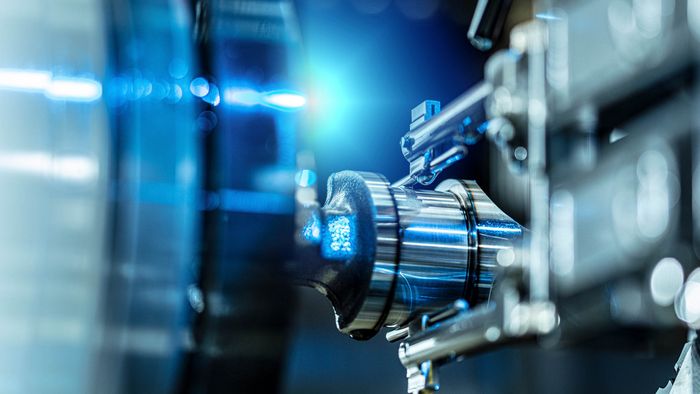
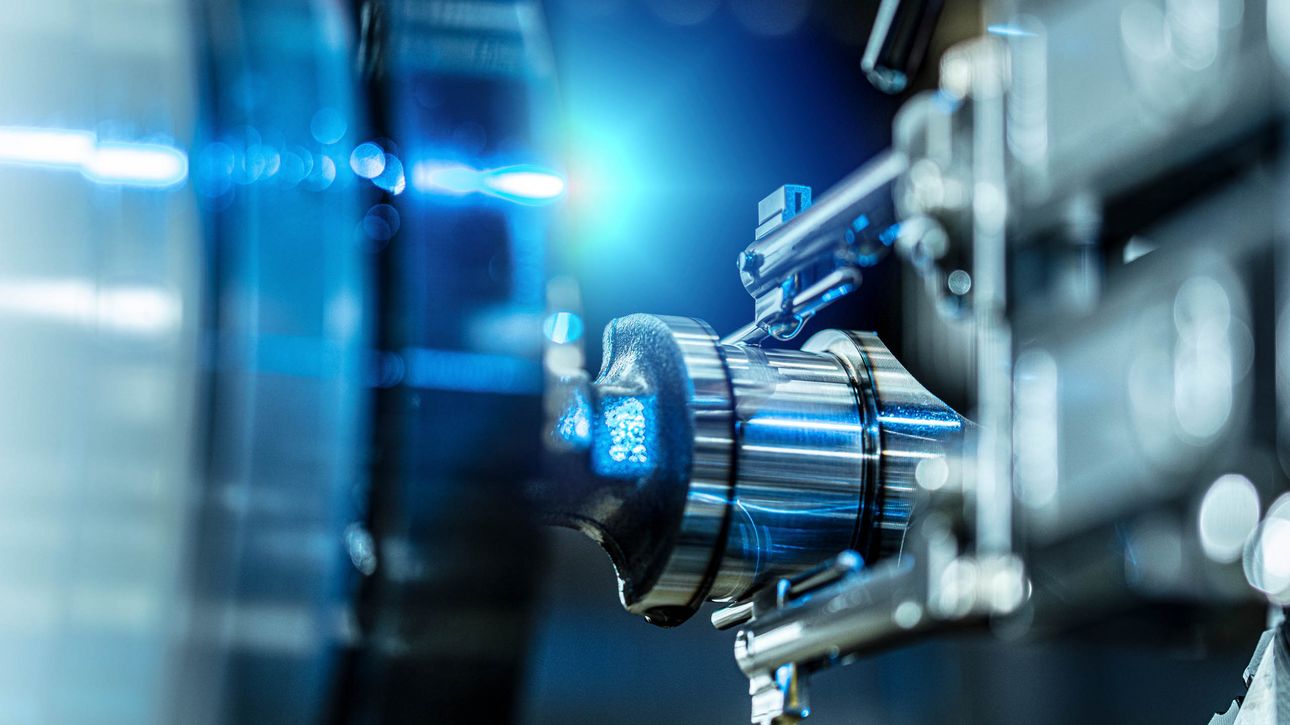
UNE BOÎTE GRISE DISCRÈTE repose sur le sable rouge de Mars. De la fumée s’élève du dispositif satellite. Depuis un vaisseau spatial, Alexander Gerst commande le robot Rollin’ Justin. Il ouvre le système à la surface de Mars. Il identifie le module fumant et le remplace par un neuf. Sur une tablette, l’astronaute décide de l’étape que le robot doit effectuer. Ça y est ! La communication avec la planète rouge est assurée. Certes, c’était juste une simulation. Le robot était en utilisation dans le centre spatial d’Oberpfaffenhofen allemand, Alexander Gerst l’a tout de même commandé depuis la station spatiale internationale ISS. Effectivement, des robots intelligents représentent un facteur décisif lors de la découverte et du développement de planètes lointaines. Et vraisemblablement, avec Rollin’ Justin ou l’un de ses collègues, un morceau de la technique de rectification de UNITED GRINDING Group aurait été utilisé sur Mars. Les réducteurs appelés Robot Speed Reducer Gears ont été utilisés dans les articulations du robot. Ces réducteurs de vitesse réduisent le régime du moteur, qui entraîne les articulations. Sans eux, le robot ne serait pas en position d’effectuer des mouvements dosés. « Cette combinaison de rentabilité, d’efficacité et de qualité d’usinage n’est égalée par aucun autre procédé d’usinage », explique le Professeur Dr Konrad Wegener de l’Institut des machines-outils et de la fabrication de l’ETH à Zürich. Les réducteurs Robot Speed Reducer Gears illustrent cela de façon remarquable : des encoches en demi-cercle avec une tolérance de diamètre de +/-3 μm sont rectifiées dans les articulations. Usinage 24 h/24 et 7 j/7,sans intervention humaine. « Environ 2,5 millions d’entraînements comme celui-ci sont usinés chaque année avec les machines MÄGERLE », estime le responsable produit Viktor Ruh.
TROIS CRITÈRES
La rectification en tant que procédé de fabrication captivant est une technique très ancienne. Déjà en Grèce antique les pierres à aiguiser étaient refroidies à l’eau ou à l’huile. En 1845, la première machine de rectification cylindrique fut commercialisée. Et depuis 174 ans, les processus de fabrication n’ont rien perdu de leur pertinence. « Le processus brille aujourd’hui par des taux de prélèvement matière élevés, des temps de cycle courts et une usure minimale de l’outil. Aucune autre technologie n’offre cela », résume Harri Rein. Rein est le CTO du groupe technologique Tool. Daniel Huber remplit cette fonction pour Cylindrical, Daniel Mavro pour Surface & Profile. Avec Christoph Plüss, Responsable en chef des technologies (CTO) du groupe, ils forment le comité de CTO, qui définit le cadre pour le développement technologique des huit marques du groupe. La rectification intervient non seulement dans la robotique mais également dans la micro-électronique. Les plaques de base, appelées Wafer, semi-conducteurs, pour les composantes électroniques, sont rectifiées. Dans les technologie innovantes, l’utilisation de nouveaux matériaux est souvent d’abord possible par les procédés d’usinage correspondants. Les composites céramiques par exemple dans les groupes motopropulseurs de l’industrie aérospatiale sont le mieux travaillés par la rectification. « Les composants légers en plastique à renfort fibre de carbone pour l’industrie automobile ou l’aviation sont usinés avec des outils PCD, qui auparavant ont subi un processus de rectification », explique Huber.
AVANTAGES LORS DE L’APPLICATION
La grande qualité d’usinage de la rectification présente de nombreux avantages dans les applications industrielles « Les finitions de surface plus fines dans le secteur automobile entraînent une réduction du frottement et donc un rendement moteur plus élevé », ajoute Mavro. « Les tolérances plus étroites dans l’industrie aéronautique et aérospatiale augmentent le rendement des groupes motopropulseurs, par exemple par la réduction de la perte de courant d’air de refroidissement. » Dans le domaine automobile par exemple, les marques du groupe proposent de nombreuses applications innovantes. Par exemple, la rectification des arbres d’équilibrage sur ShaftGrind S de SCHAUDT. Ceux-ci assurent un fonctionnement fluide dans un moteur à combustion, en produisant une contre-fréquence. Ils ne sont ni droits ni cylindriques et représentent ainsi un grand défi pour l’usinage. Ou bien l’usinage de crémaillères de direction sur une MFP de MÄGERLE, sur laquelle jusqu’à huit pièces à usiner dans une seule prise avec des profondeurs de profil allant jusqu’à onze millimètres et des largeurs allant jusqu’à 300 millimètres peuvent être rectifiées, ce qui représente un défi extrême pour les performances de la broche et la stabilité de l’ensemble de la machine.
MESURER ET RECTIFIER
Le procédé de rectification en lui-même peut être combiné avec des procédés annexes comme la mesure ou le dressage. « Ici, une machine de rectification peut être construite comme une cellule avec une machine de mesure, dont le passage de l’une à l’autre est robotisé » explique le CTO Rein. Le résultat est une production sans homme ou également « Lights out » avec laquelle peuvent être réalisées des pièces en grande quantité. Dans le Système IMS (Internal Measuring System) de WALTER, par exemple, les paramètres des outils en production peuvent être enregistrés. En cas d’écart, le système du processus d’usinage régule ou arrête la production, lorsque la plage de tolérance est outrepassée. « Même pour les petits lots ou les pièces à usiner uniques, la mesure pendant le processus est importante, pouratteindre immédiatement la précision exigée », explique Huber. Le dressage permet ainsi de compenser l’usure des meules. Ainsi, tout au long du cycle de production, ce sont exactement les mêmes tolérances de pièces et la même qualité qui sont garanties. « Dans certains domaines d’application, de plus en plus de matériaux durs comme la céramique sont utilisés, qui exigent des super-abrasifs, qui à leur tour demandent un liant métallique particulier de la meule », explique Wegener. Et pour une meule à liant métallique, WireDress® est la technologie de choix pour le dressage. Selon le principe de l’électroérosion à fil, la meule sera ainsi dressée sans contact. Le résultat est un dégagement du grain maximal et une découpe optimale.
« Je crois que les meules à liant métallique WireDress® vont permettre une percée significative », déclare Wegener, dont l’institut a développé cette technologie avec STUDER.
LE FACTEUR HUMAIN
Un autre facteur important, qui détermine le résultat du procédé de rectification, est l’opérateur. « Son expérience est d’une grande importance », souligne le CTO Rein. C’est pourquoi toutes les entreprises de UNITED GRINDING Group investissent fortement dans la formation continue et professionnelle de leurs employés (voir les pages 36 et suivantes pour plus d’informations). Le savoir-faire humain conservera son importance également malgré la numérisation. « D’un côté, l’expérience du rectifieur de nos jours doit être prise en compte dans les systèmes d’assistance et les banques de données, d’un autre côté, les tâches qui incombent à l’opérateur seront à l’avenir plus exigeantes », ajoute Huber. Parce que : « En cas de cellule de fabrication complexe, l’utilisateur a besoin de compétences d’un tout autre niveau », ajoute Mavro. Ainsi UNITED GRINDING Group veut concilier deux choses : la meilleure technologie et les meilleurs employés. Ces deux facteurs entraînent les meilleurs résultats de rectification.