Alimentation en liquide de refroidissement et conception de la buse
Lors du processus de rectification, le risque d'un dégagement de chaleur important est toujours présent. Le liquide de refroidissement joue un rôle décisif dans le refroidissement de la pièce à usiner afin de la protéger contre les dommages thermiques et constitue donc un élément important dans le processus de rectification. Découvrez dans ce Motion Blog pourquoi les buses imprimées en 3D augmentent l'efficacité de la lubrification par refroidissement et quels sont les avantages de la lubrification synchronisée.
Conception des buses de refroidissement
Les buses de refroidissement jouent un rôle essentiel dans l’acheminement du liquide de refroidissement dans la zone de rectification pour permettre son nettoyage, sa lubrification et son refroidissement. Dans la construction d'outils, par exemple, il est particulièrement important que la position des buses puisse être ajustée de manière flexible. Cela est dû au fait que différents types de pièces sont souvent usinés en petites séries. C’est la raison pour laquelle les buses composées d’éléments modulaires en plastique sont très appréciées par les industriels. Elles peuvent être positionnées manuellement et adaptées rapidement à de nouvelles géométries de pièces. Cependant, les matières synthétiques au niveau des ouvertures des buses ont tendance à s'endommager, ce qui peut entraîner des turbulences et, par conséquent, une diminution de l'efficacité du lubrifiant-réfrigérant. Les alternatives utilisant des articulations métalliques en acier inoxydable améliorent certes la situation, mais s'avérent être moins flexibles, ce qui compromet l'efficacité globale. Chaque maillon d'un système d'articulation génère des turbulences, et rend donc le système de distribution du lubrifiant-réfrigérant moins efficace. De plus, il existe un risque que la position précédemment ajustée pour la distribution soit involontairement déplacée.
En raison de ces inconvénients, les experts optent souvent pour des buses en acier massif lors de la rectification de haute précision, dans la mesure où celles-ci garantissent une alimentation constante et précise du liquide de refroidissement. Les avancées dans la fabrication additive 3D, telles que la fusion laser sélective (SLM - Selective Laser Melting) ou la fusion sur lit de poudre laser (LPBF - Laser Powder Bed Fusion), ouvrent des voies innovantes pour la production de buses en acier inoxydable. Ces procédés permettent, sur la base de simulations de dynamique des fluides complexes, de produire des buses à jet libre présentant des profils d'écoulement optimaux qui ne sont pas réalisables avec des méthodes de fabrication traditionnelles. L'objectif est de produire un jet uniforme et exempt de turbulences, afin de maximiser l'efficacité du système de refroidissement et de lubrification.
Une buse imprimée en 3D à écoulement optimisé présente une résistance à l'écoulement plus faible qu'une buse standard pour le même débit. Dans certaines applications, les buses disposent même de leur propre axe NC afin de compenser la réduction continue de la meule due à son dressage et de maintenir sa position dans une position idéale. Ce principe est mis en œuvre, par exemple, dans les modèles MÄGERLE MFP 50 ou MFP 100.
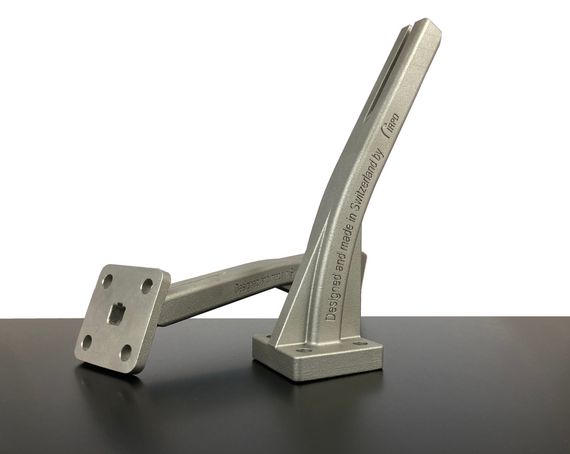
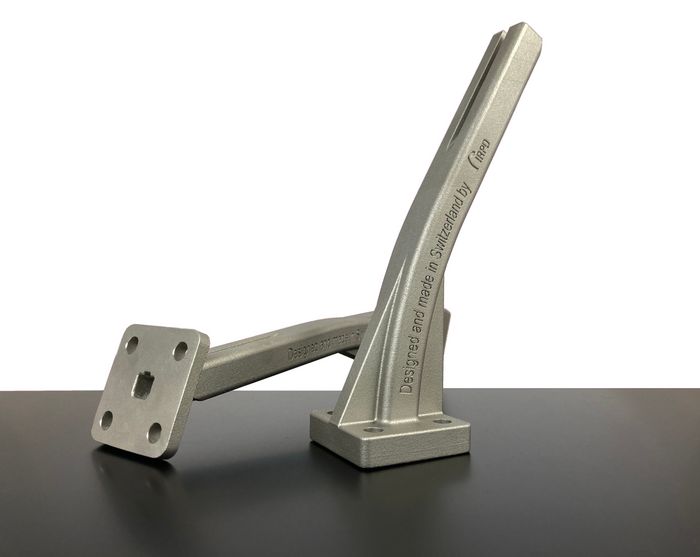
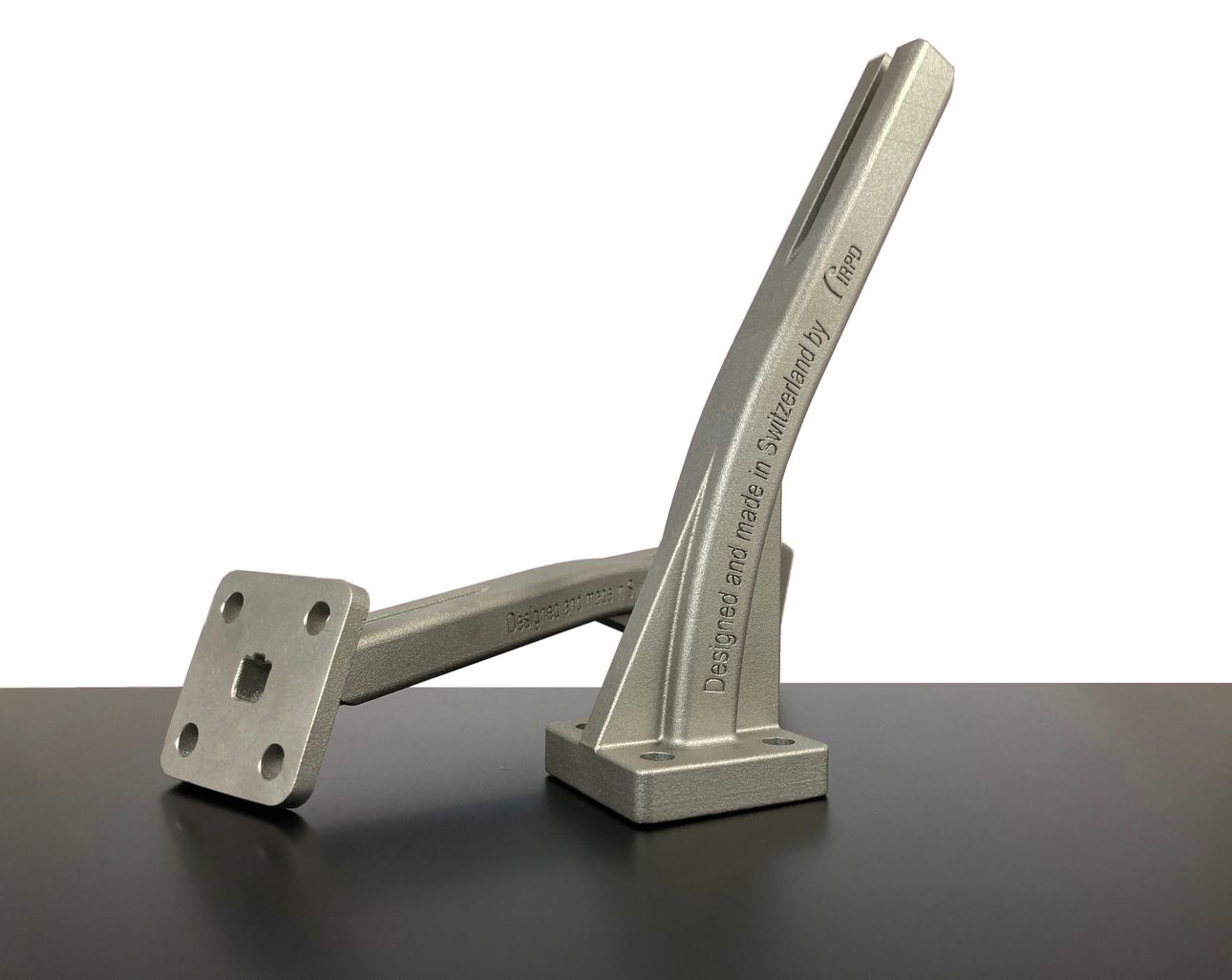
Avantages de la lubrification synchrone
Le principe fondamental réside dans le fait que le jet de fluide de refroidissement est projeté à la même vitesse que la vitesse périphérique de la meule. Cette méthode, connue sous le nom de « lubrification synchrone », a été développée dans les années 1980 par H.W. Ott, un pionnier en matière de rectification en Suisse [1]. Recherches du professeur Karpuschewski [2] à l'IWT de l'université de Brême ont confirmé les thèses d'Otto en 2022. Les études ont été réalisées en utilisant la « rectification de profil de dentures » et ont démontré que l'ajustement de la vitesse du liquide de refroidissement à celle de la meule permet d'atteindre le volume spécifique maximal de copeaux V'w. Le volume de copeaux spécifique définit la quantité de matière enlevée avant que la meule ne nécessite un réajustement, en raison de la perte de profil ou de l'apparition de brûlures de rectification. Il est intéressant de noter que les résultats ont montré qu'une vitesse de jet inférieure se révèle plus efficace qu'une vitesse supérieure par rapport à la lubrification synchrone.
Influence de la vitesse du jet sur le volume d’enlèvement de copeaux
Vitesse périphérique: 35 m/s
Qw: 7,5 à 25 mm3/mm/sec
Source: Prof. Dr Karpuschewski, IWT Brême
Lubrification synchrone dans la pratique
Bien que les vitesses de jet puissent être calculées, cela n'est souvent pas favorable dans le contexte d'un atelier. Pour obtenir une lubrification synchrone de manière pratique, la buse de rectification doit être placée au-dessus de la ligne médiane de la meule. Le jet de liquide de refroidissement doit frapper tangentiellement la circonférence de la meule à un angle de 20°.
Lubrification synchrone selon Ott (Vk = Vc)
buse inclinée à 20°;
impact tangentiel du jet sur la circonférence de la meule;
le jet «adhère» à la circonférence de la meule
Lorsque la vitesse du jet de lubrifiant-réfrigérant correspond à la vitesse périphérique de la meule, le jet adhère à la meule, garantissant ainsi une distribution optimale du lubrifiant-réfrigérant dans la zone de rectification. Dans les applications de rectification exigeantes, telles que celles utilisées dans l’industrie des roulements à billes et de l’automobile, l’alimentation en liquide de refroidissement est adaptée avec précision aux paramètres de processus. En revanche, dans la fabrication d'outils, les résultats sont souvent moins précis, mais peuvent être satisfaisants en ajustant correctement la position des buses. Le réglage du débit de liquide de refroidissement s’effectue à l’aide de la vanne située sur le tuyau d’alimentation la machine. Avant d'introduire le lubrifiant-réfrigérant, retirez la pièce de la meule, positionnez la buse à l'emplacement spécifié et amenez la meule à sa vitesse de fonctionnement. Ensuite, la vanne du liquide de refroidissement s'ouvre progressivement jusqu'à ce que le jet adhère de manière stable à la meule. Cela permet de s’assurer que le liquide circule dans la zone de rectification lorsque la meule et la pièce sont en contact.
Position de la buse de refroidissement lors de la rectification cylindrique
La méthode de réglage de la position de la buse utilisée pour la rectification cylindrique peut également être appliquée pour la rectification plane. Éloignez d'abord la pièce de la meule, positionnez la buse à l'emplacement spécifié et amenez la meule à sa vitesse de fonctionnement. Ensuite, ouvrez progressivement la vanne du lubrifiant-réfrigérant jusqu'à ce que le jet adhère à la meule.
Position de la buse de refroidissement lors de la rectification plane
Résumé
Vue d’ensemble des points les plus importants concernant la configuration des buses de liquide de refroidissement :
- Lubrification synchrone vk = vc
- Impact tangentiel du jet de liquide de refroidissement sur la circonférence de la meule
- Position de la buse avec une distance et un angle d’attaque suffisants (20°)
- Débit compris entre 1,5 et 5 litres par minute et par mm de largeur de la meule
Besoin d’aide ?
Vous êtes intéressé par les buses de refroidissement imprimées en 3D d’IRPD ? Ou avez-vous besoin d’aide pour la conception optimale de votre système de refroidissement ? Contactez-nous. Nos experts se feront un plaisir de vous aider.
Documentation
[1] H.W. Ott & Co., Grundlagen der Schleiftechnik, 1986, auto-édition
[2] Prof. Dr habil. Bernhard Karpuschewski, Bedarfsgerechte Kühlschmierstoff-Versorgung, présenté à l'IWT Bremen lors de la Schleiftagung 2024 à Fellbach