Éviter les brûlures de rectification
Un dégagement de chaleur trop important pendant le processus de rectification peut entraîner des dommages thermiques sur la pièce à rectifier, ce qui entraîne souvent la mise au rebut de la pièce concernée. Découvrez dans ce blog Motion comment se produit ce dégagement de chaleur, et la manière dont il est possible de le détecter et de l’éviter.
Définition d’une brûlure de rectification
Commençons par définir les brûlures de rectification et ses causes. Lors de la rectification d’acier trempé, presque toute l’énergie appliquée par la broche de rectification est convertie en chaleur. Dans des processus de rectification idéaux, cette chaleur devrait être dissipée par les copeaux produits et le liquide de refroidissement. Cependant, si la chaleur ne peut pas être évacuée efficacement, elle pénètre dans la pièce et peut entraîner des modifications de la structure ou des zones marginales, connues sous le nom de brûlure de rectification ou de dommages thermiques. Ces modifications peuvent provoquer des fissures de frottement et des contraintes de traction, qui, si elles sont détectées, conduisent inévitablement à la mise au rebut de la pièce concernée. Cette élimination est nécessaire pour éviter des conséquences graves découlant de composants défectueux dans des applications cruciales telles que des moteurs, des turbines et des machines.
Formation de brûlures de rectification
La brûlure de rectification est un phénomène complexe influencé par une multitude de facteurs. Pour éviter les brûlures de rectification, il est essentiel de sélectionner correctement les paramètres de rectification, d’utiliser des meules adaptées, un refroidissement efficace, de comprendre les propriétés du matériau, de maîtriser la rectifieuse et d’utiliser une technique de rectification dans les règles de l'art. Une surveillance minutieuse du process alliée à adaptation ciblée de ces facteurs contribuent à améliorer la qualité des résultats de rectification et à réduire les risques et les dommages qui en découlent.
Les principales causes sont examinées ci-dessous.
1. Paramètres de rectification
Pour tous les procédés de rectification, la vitesse périphérique vc de la meule, exprimée en mètres par seconde, constitue l’un des paramètres de rectification les plus importants. Une règle fondamentale stipule qu'une meule tournant plus rapidement entraîne des temps de contact plus courts entre la meule et la pièce à rectifier. Dans certains cas, cela peut contribuer à réduire les brûlures de rectification, à condition que le processus soit conçu pour des vitesses élevées avec une capacité de refroidissement adéquate. Cependant, une augmentation de la vitesse périphérique peut également avoir pour effet de rendre la meule trop dure, ce qui la rend plus sujette aux brûlures de rectification. Une compréhension approfondie du processus de rectification est donc essentielle. Souvent, le risque de brûlures de rectification peut être minimisé en réduisant la vitesse périphérique vc de la meule. Des paramètres supplémentaires – s’ils sont sélectionnés trop haut ou trop bas – peuvent avoir un impact sur les brûlures de rectification lors de la rectification cylindrique. Cela inclut le nombre de tours de la pièce à usiner par minute nw et l’avance en plongée vf en millimètres par minute. Pour la rectification cylindrique extérieure longitudinale, cela comprend les paramètres d'avance ae en millimètres par dépassement ainsi que l’avance longitudinale vfa en millimètres par minute.
Lors de la rectification plane ou de rectification à passe profonde, la vitesse de la table en m/min vw et l’avance en profondeur ae par dépassement en mm sont d’autres paramètres clés. Un indicateur éprouvé est le rapport de vitesse qs entre la meule et la pièce à rectifier. Pour la rectification cylindrique et la rectification pendulaire plane, celle-ci se situe entre 60 et 80 et ne doit pas dépasser 120, le risque de brûlures augmentant au-delà de cette valeur. Un rapport des vitesses qs de 80 signifie que la vitesse périphérique de la meule est 80 fois supérieure à celle de la pièce à rectifier. Lors de la rectification à passe profonde, le rapport des vitesses qs doit être au moins supérieur à 1000, mais idéalement commencer à 1500 pour sortir de la zone de danger de brûlures de rectification.
2. Alimentation en liquide de refroidissement et conception de la buse
La vitesse de sortie du lubrifiant réfrigérant Vkss devrait idéalement correspondre à la vitesse périphérique de la meule vc. Cela est couramment désigné par le terme de lubrification synchrone. Les risques de brûlures de rectification sont significativement accrus aussi bien avec des vitesses d'évacuation trop basses que trop élevées. La buse doit être positionnée de manière à ce que le jet de liquide de refroidissement arrive tangentiellement à la péirphérie de la meule, juste avant la zone de contact entre la meule et la pièce à rectifier. Dans la pratique, un angle d'inclinaison de 20° s'est avéré être particulièrement efficace. De plus, l'ouverture de la buse ne devrait présenter aucune courbure ni dommage susceptible de perturber le jet par des turbulences avec l'air à la sortie. L’utilisation de buses en acier par impression 3D, disponibles auprès d’IRPD, est aujourd’hui recommandée. Pour estimer le débit de fluide de refroidissement nécessaire, la directive suivante s'applique : Q kss = env. 1,5 – 5,0 l/min par mm de largeur de la meule en cours d'utilisation. (Selon les indications du Prof. Dr Bernhard Karpuschewski de l’IWT de Brême).
3. Paramètres de dressage
La pratique a montré que des paramètres de dressage mal sélectionnés sont souvent à l’origine de brûlures de rectification, en particulier si la meule a été dressée trop finement. Une meule dressée trop finement augmente la pression de rectification et la friction des grains, conduisant inévitablement à une augmentation de la chaleur du process. Il existe des formules simples pour calculer l'avance de dressage vd des outils de dressage verticaux. On choisit un taux de recouvrement ud de 4, on détermine la largeur active bd (généralement env. 0,8 mm pour une plaquette de dressage) et on applique la formule suivante :
vd (avance de dressage en mm/min) = (ns (vitesse de rotation de la meule/min) x bd (largeur active du diamant en mm) ) /ud (taux de recouvrement)
Pour obtenir une excellente qualité de surface et des taux d’enlèvement de matière élevés, il est impératif de travailler avec de petites avances ad (profondeurs de coupe), c’est-à-dire 0,002 à 0,03 mm par passe de dressage. Pour augmenter la rugosité de la surface et la capacité de coupe de la meule, il convient d'augmenter l’avance de dressage vd et non pas la profondeur de l’avance de dressage a d. Pour les outils de dressage rotatifs, il convient de sélectionner un rapport des vitesses qd de 0,6 à 0,8 pour l’usinage « en avalant ». On obtient ainsi une meule tranchante avec un risque réduit de brûlures des rectification.
qd (rapport des vitesses) = VR (vitesse périphérique de la meule diamantée) /VC (vitesse périphérique de la meule)
4. Spécifications de la meule
Une mauvaise sélection des spécifications de la meule peut également être à l'origine de brûlures de rectification. Plus le grain abrasif est fin, plus la pression de rectification et l’apport de chaleur dans la pièce à rectifier sont élevés. Des meules d'un degré de dureté élevé signifient des proportions élevées de liant, ce qui augmente le risque brûlures de rectification, car il est bien connu que le liant ne rectifie pas et provoque des frictions. Les structures étroites présentent un faible volume de pores, apportant ainsi de faibles quantités de liquide de refroidissement dans la zone de rectification et ne permettant pas une évacuation efficace des copeaux. Dans ce cas, il est préférable que l'utilisateur consulte son fournisseur de meules. En particulier pour la rectification à passe profonde, il faut utiliser des spécifications très poreuses et tendres, à faible liant, sous risque de provoquer inévitablement des brûlures de rectification. Pour la plongée oblique cylindrique extérieure, il convient également d’utiliser des meules poreuses pour les hauteurs d’épaulement supérieures à 7 mm.
5. Manque de main-d'œuvre qualifiée ou d'expertise en matière de rectification
Il est essentiel que les opérateurs de machines aient une compréhension approfondie des quatre premiers points mentionnés et de leurs interactions. Si ce n’est pas le cas, nous serons ravis de vous aider en vous proposant des cours de rectification adaptés.
Méthodes de contrôle des brûlures de rectification
- Inspection visuelle
La pièce peut être examinée à l'œil nu pour vérifier si des décolorations sont apparues sur la surface de la pièce. Cette méthode n’est pas très fiable, dans la mesure où des brûlures de rectification ont pu être générées pendant l’ébauchement, tandis que des décolorations ont pu être éliminées par la rectification de finition.
- Attaque au Nital
L’attaque au Nital est un processus non destructif en plusieurs étapes destiné aux aciers trempés. Cette procédure ne peut pas être utilisée pour les pièces aéronautiques en Inconel et matériaux similaires. L’attaque avec de l’acide nitrique dilué et le blanchiment à l’acide chlorhydrique dilué permettent de faire apparaître les brûlures de rectification sous forme de nuances de gris modifiées.
- Le procédé Barkhausen
Le procédé Barkhausen, un procédé électromagnétique, permet de détecter les différences de dureté et de tensions résiduelles dans les matériaux ferromagnétiques causées par les brûlures de rectification. Le procédé de Barkhausen est totalement non destructif et peut être utilisé directement sur la rectifieuse. Cependant, il nécessite un étalonnage avec une pièce exempte de brûlures de rectification.
- Diffraction des rayons X (XRD)
Cette méthode permet de mesurer les contraintes résiduelles des matériaux, même dans les métaux non ferreux comme l'inconel et d'autres alliages de nickel difficiles à rectifier utilisés dans l'aérospatiale et l'aviation.
Avez-vous des questions?
Si vous avez d’autres questions à ce sujet, n’hésitez pas à nous contacter. Nos experts se tiennent à votre disposition pour vous conseiller.
Exemple de brûlures de rectification
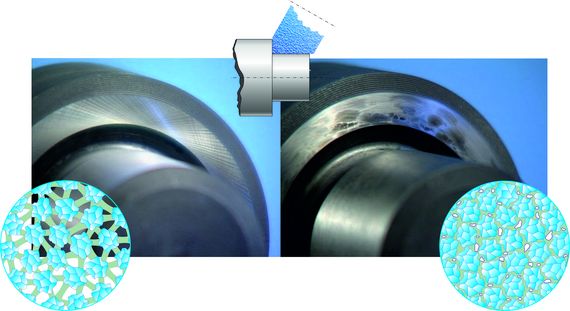
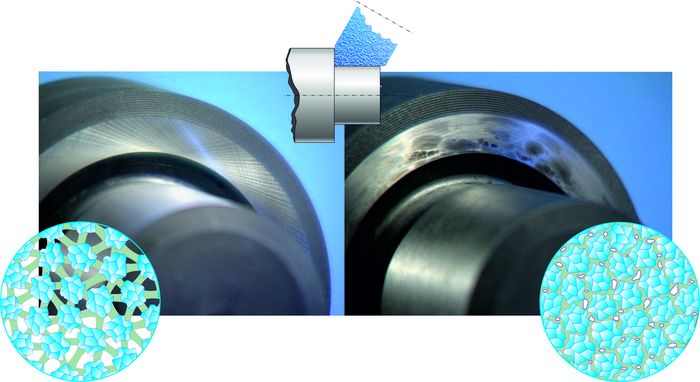
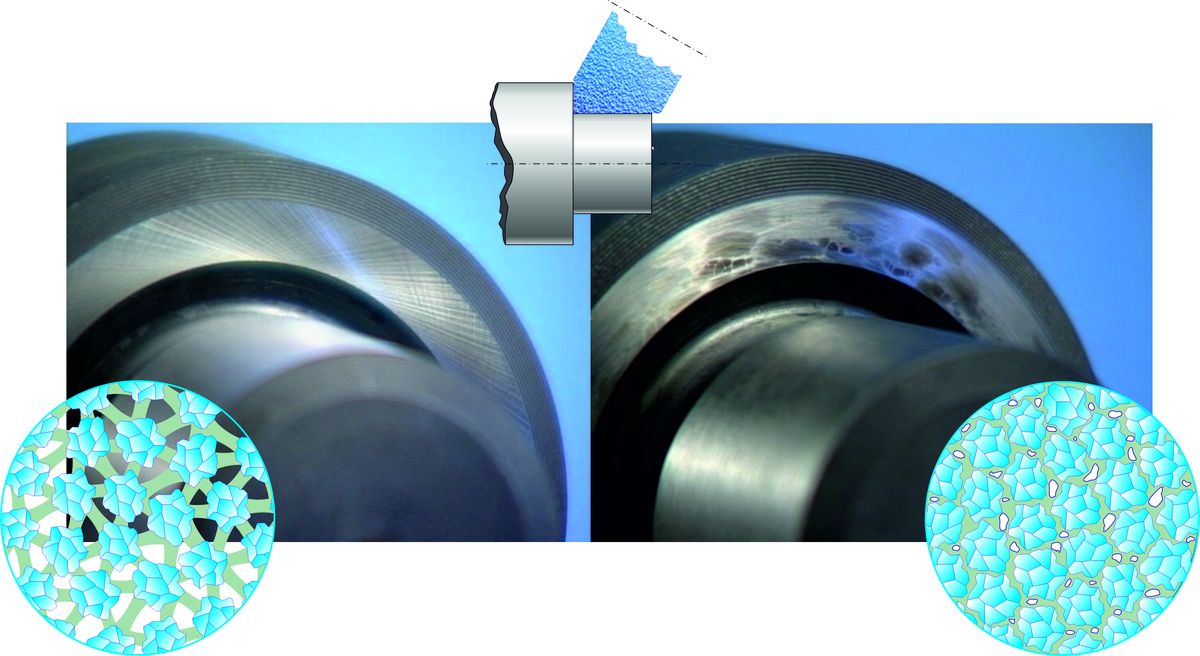
À droite : brûlures de rectification ; utilisation d’une meule fermée