연삭 공정에서 과도한 발열 현상이 나타날 수 있으며, 이로 인해 해당 부품을 폐기해야 하는 경우가 자주 발생합니다. 이 모션 블로그에서 이러한 열 발생 원인과 이를 확인하고 방지하는 방법에 대해 확인하시기 바랍니다.
연삭 버닝의 정의
연삭 버닝의 정의와 연삭 버닝 발생 원인부터 시작하겠습니다. 경화강을 연삭할 때 연삭 스핀들에 의해 가해지는 거의 모든 에너지가 열로 변환됩니다. 이상적인 연삭 공정에서는 이러한 열은 파생되는 칩과 연삭유를 통해 방출되어야 합니다. 그러나 열을 효과적으로 제거할 수 없는 경우, 이 열은 공작물에 침투하여, 연삭 버닝 또는 열 손상으로 알려진 구조 변화 또는 가장자리 영역의 변화를 일으킬 수 있습니다. 이러한 변화는 연삭 균열 및 인장 응력을 촉진할 수 있으며, 이를 발견하면 필연적으로 해당 부품을 폐기해야 합니다. 이는 엔진, 터빈 및 기계와 같은 중요한 적용 분야에서 불량 부품으로 인해 발생할 수 있는 심각한 결과를 방지하기 위해 필요합니다.
연삭 버닝 발생
연삭 버닝은 다양한 요인의 영향을 받는 복합적인 현상입니다. 연삭 버닝을 방지하기 위해서는 적절한 연삭 휠 사용, 효과적인 냉각, 재료 특성에 대한 이해, 연삭기 제어 및 전문적인 연삭기술 수행 등과 마찬가지로 연삭 매개변수의 올바른 선택이 중요합니다. 이러한 요소를 주의 깊게 모니터링하고 적절하게 조정함으로써 연삭 결과의 품질을 향상시키고 연삭 열에 의한 손상 위험을 줄일 수 있습니다.
다음에서는 주요 원인에 대해 언급하고자 합니다.
1. 연삭 매개변수
모든 연삭 공정에서 가장 중요한 연삭 매개변수 중 하나는 초당 미터 단위로 표시된 연삭 휠의 원주 속도 vc 입니다. 기본 규칙은 연삭 휠의 회전 속도가 더 빠를수록 연삭 휠과 공작물 사이의 접촉 시간이 짧아진다는 것입니다. 이는 공정이 적절한 냉각 성능을 갖춘 고속용으로 설계되었다면, 경우에 따라 연삭 버닝을 줄이는 데 도움이 될 수 있습니다. 그렇지만 원주 속도가 높아지면 연삭 휠이 너무 단단하게 작용하여 연삭 버닝을 일으킬 수 있습니다. 따라서 연삭 공정에 대한 심층적인 이해가 필수적입니다. 종종 연삭 휠의 원주 속도 vc를 낮추면 연삭 버닝의 위험을 최소화할 수 있습니다. 원통 연삭 시 연삭 버닝에 영향을 미치는 추가적인 매개변수(너무 높거나 너무 낮게 선택된 경우)에는 분당 공작물 회전 속도 nw, 플런지 공정의 분당 밀리미터 단위의 인피드 vf 가 포함됩니다. 외경 원통 트래버스 연삭의 경우에는 스트로크당 밀리미터 단위의 인피드 ae 및 분당 밀리미터 단위의 종방향 이송 vfa 등의 매개변수가 포함됩니다.
평면 연삭 또는 크립 피드 연삭의 경우에는 m/min 단위의 테이블 속도 vw 및 mm 단위의 스트로크당 플런징 ae 역시 주요 매개변수에 속합니다. 입증된 특성값으로는 연삭 휠과 공작물 사이의 속도 비율 qs 가 있습니다. 원통형 및 평면 진자 연삭의 경우 이 값은 60 - 80 사이이며 120을 초과해서는 안 됩니다. 이 값을 초과하면 버닝 위험이 증가하기 때문입니다. 속도 비율 qs가 80이라면, 이는 연삭 휠의 원주 속도가 공작물 속도보다 80배 높다는 것을 뜻합니다. 크립 피드 연삭의 경우 속도 비율 qs는 최소한 1000 이상이어야 하지만 연삭 버닝 위험 구역을 벗어나려면 약 1500에서 시작해야 합니다.
2. 연삭유 공급 및 노즐 설계
연삭유 분사 속도 Vkss는 이상적으로는 연삭 휠의 원주 속도 vc에 적합해야 합니다. 이는 동기식 윤활이라는 용어로 알려져 있습니다. 분사 속도가 낮거나 높을수록 연삭 버닝의 위험이 크게 증가할 수 있습니다. 노즐의 위치는 냉각수 빔이 연삭 휠과 공작물 사이의 접촉 영역 바로 앞에서 연삭 휠 원주에 접선 방향으로 닿도록 선택해야 합니다. 20°의 접촉각은 실제로 효과적인 것으로 입증되었습니다. 또한 노즐 구멍에는 배출 시 공기 와류로 인해 빔을 방해할 수 있는 곡선이나 손상이 없어야 합니다. 요즘에는 IRPD를 통해 구입할 수 있는 3D 프린팅된 스틸 노즐의 사용이 권장됩니다. 필요한 연삭유 체적 유량을 추정할 때 다음 지침이 적용됩니다: Qks s = 사용 중인 휠 폭의 mm당 약 1.5 - 5.0 l/min. (IWT Bremen의 Dr. Bernhard Karpuschewski 교수에 따른 공식).
3. 드레싱 매개변수
실제로 잘못 선택된 드레싱 매개변수는 특히 연삭 휠이 너무 미세하게 드레싱된 경우 연삭 버닝의 원인이 되는 경우가 많습니다. 연삭 휠이 너무 미세하게 드레싱되면 연삭 압력과 입자 마찰이 증가하여 필연적으로 공정 시의 열이 증가합니다. 고정식 드레싱 툴의 드레싱 피드 vd를 계산하는 간단한 공식이 있습니다. 중첩률 ud로는 4를 선택하고, 유효 폭 bd(타일의 경우 대부분 약 0.8 mm)를 결정한 후 다음과 같은 공식을 사용합니다:
vd (드레싱 이송 속도, 단위: mm/Min) = (ns (휠 회전속도/Min) x bd (다이아몬드의 유효 폭, 단위: mm) ) / ud (중첩율)
탁월한 표면 품질과 동시에 높은 제거율을 달성하기 위해서는 작은 인피드 ad (절단 깊이), 즉 드레싱 패스당 0.002 - 0.03 mm로 작업하는 것이 매우 중요합니다. 휠의 표면 거칠기 및 절삭성을 높이기 위해서는 드레싱 이송 속도 vd를 높이고, 드레싱 이송 깊이 ad는 높이지 않습니다. 회전하는 드레싱 툴의 경우 동기화 시 0.6 - 0.8의 속도 비율 qd를 선택해야 합니다. 이를 통해 버닝 경향이 적은 매끄러운 연삭 휠을 얻을 수 있습니다.
qd (속도 비율) = VR (다이아몬드 롤러의 원주 속도) / VC (연삭 휠의 원주 속도)
4. 연삭 휠 사양
잘못 선택된 연삭 휠 사양도 연삭 버닝의 원인이 될 수 있습니다. 연삭 입자가 미세할수록 연삭 압력이 높아지고 공작물에 열이 유입됩니다. 경도가 높은 연삭 휠은 높은 접착력을 의미하며, 접착력은 연삭하지 않고 마찰을 일으키는 것으로 알려져 있기 때문에 버닝 경향이 증가합니다. 좁은 구조는 기공 공간이 거의 없기 때문에 연삭 구역에 소량의 냉각 윤활제만 공급할 수 있으며 칩도 효율적으로 제거할 수 없습니다. 이 경우 사용자는 휠 공급업체에 문의해야 합니다. 특히 크립 피드 연삭시에는 다공성이 높고 부드럽고 접착력이 낮은 사양을 사용하며, 그렇지 않은 경우 연삭 버닝이 불가피합니다. 외경 원통 앵귤러 플런지의 경우에도 숄더 높이가 7 mm 이상인 경우 다공성 연삭 휠을 사용해야 합니다.
5. 전문 인력 부족 또는 연삭 지식 부족
앞서 언급한 네 가지 사항과 이들의 상관관계는 기계 작업자가 이해해야 합니다. 그렇지 않은 경우, 당사는 적절한 연삭 강좌를 기꺼이 제공해 드리겠습니다.
연삭 버닝 점검 방법
- 육안 점검
공작물을 육안으로 관찰하여 공작물 표면에 변색이 있는지 확인할 수 있습니다. 이 방법은 황삭 시 연삭 버닝이 발생하였지만 정삭 시 변색이 제거되기 때문에 신뢰성이 떨어집니다.
- 나이탈 에칭
나이탈에칭은 경화강을 위한 다단계 비파괴적 방식입니다. 이 방식은 인코넬 및 이와 유사한 소재로 제작된 항공 부품에는 사용할 수 없습니다. 희석된 질산으로 에칭하고 희석된 염산으로 표백하면 연삭 버닝이 회색 색조 변화로 보일 수 있습니다.
- 박하우제 방식
전자기 방식인 박하우젠 소음 테스트는 연삭 버닝으로 인해 발생하는 강자성 재료의 경도 및 고유 응력 차이를 감지합니다. 박하우젠 방식은 전적으로 비파괴적이며 연삭기에서 바로 사용할 수 있습니다. 그러나 이 절차는 연삭 버닝이 없는 공작물을 사용한 교정이 필요합니다.
- X선 회절(XRD)
이 방식을 통해 우주 및 항공 분야에 사용되는 인코넬 및 연삭하기 어려운 기타 니켈 합금과 같은 비철 금속에서도 재료 고유 응력을 측정할 수 있습니다.
질문이 있으십니까?
이 주제에 대한 추가 질문이 있으시면 당사로 문의하십시오. 당사의 전문가가 조언과 지원을 제공해 드리겠습니다.
연삭 버닝 예시
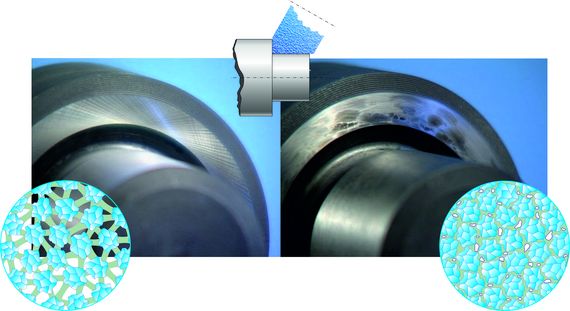
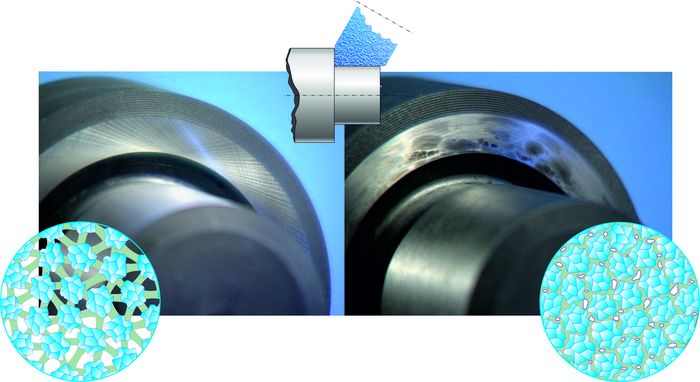
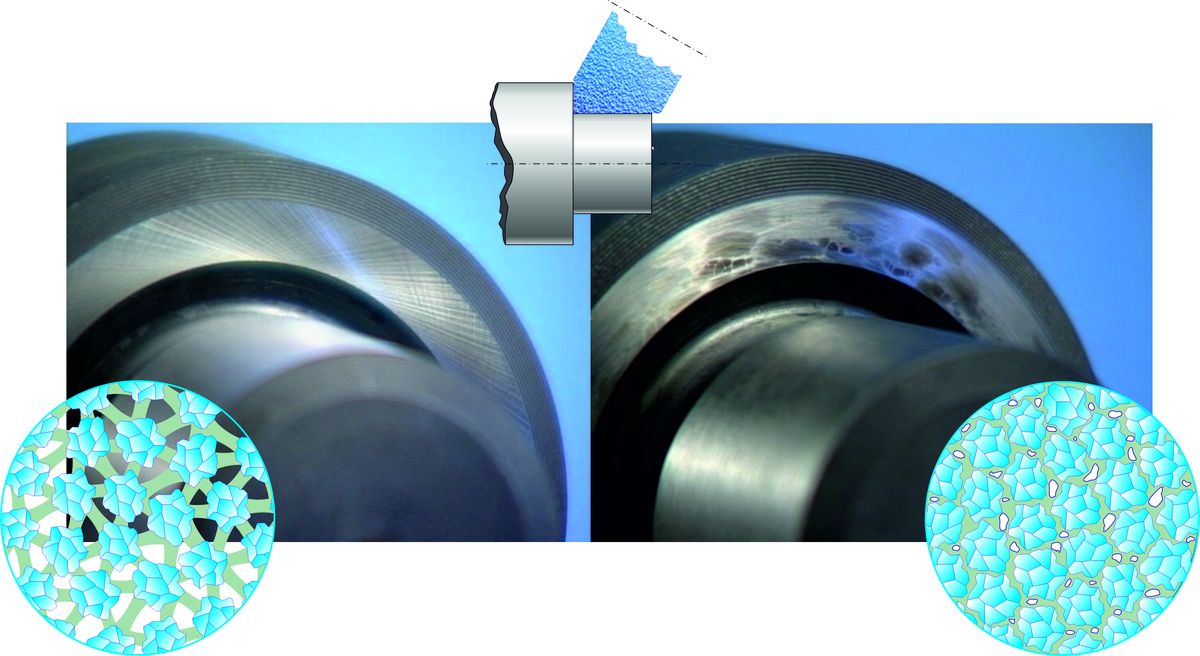
우측: 연삭 버닝, 폐쇄형 연삭 휠 사용