화성으로 가는 길
평범한 회색 상자가화성의 붉은 모래 위에 놓여져 있습니다. 위성 시스템에서 연기가 나옵니다. Alexander Gerst는 우주선에서 Rollin ’Justin 로봇을 제어합니다. 로봇은 화성 지표면에서 시스템을 엽니다. 스모킹 모듈을 식별하고 새 것으로 교체합니다. 우주 비행사는 태블릿을 사용해 로봇이 수행해야 하는 작업 단계를 정의합니다. 완료되었습니다! 화성과의 통신이 확보되었습니다. 솔직히 이것은 단순한 시뮬레이션에 불과합니다. 이 로봇은 독일 Oberpfaffenhofen의 우주 센터에 배치되었으며 Alexander Gerst는 이를 ISS(International Space Station)에서 제어하고 있었습니다. 지능형 로봇은 멀리 떨어진 행성의 발견 및 탐사에서 중요한 요소로 간주됩니다. 그리고 Rollin’ Justin을 비롯한 그의 동료들과 함께 UNITED GRINDING Group의 연삭 기술을 화성에서 사용할 수도 있습니다. 로봇 감속 기어는 로봇 관절에 사용됩니다. 이 감속기는 관절들을 구동하는 모터의 속도를 낮춥니다. 이들이 없었다면, 로봇은 계량된 이동을 수행할 수 없습니다. ETH Zurich의 공작 기계 및 생산 연구소 Konrad Wegener 박사는 "비용 효율성, 효율성 및 기계 품질 조합 면에서 다른 모든 제조 공정보다 우수합니다”라고 말합니다. 로봇 감속기는 다음을 인상적으로 표현한 것입니다. 직경 허용 오차 +/- 3μm (+/- 0.000`12”)의 반원형 홈이 조인트부에 연삭됩니다. 제조는 연중무휴 24시간 동안 이루어집니다. “매년 2백5십만개의 기어를 MÄGERLE 기계로 연삭하고 있습니다.” 제품 관리자인 Viktor Ruh는 추정합니다.
세 가지 기준
기계 가공 공정으로서 연삭은 오래된 기술입니다. 고대 그리스에서 연삭석은 물이나 오일로 냉각되었습니다. 최초의 원통형 연삭기는 1845년에 시장에 출시되었습니다. 그리고 174년이 지난 지금도, 이 제조 공정은 이에 대한 관련성을 전혀 잃지 않았습니다. “이 공정은 최고의 제거율, 짧은 사이클 시간과 최소한의 공구 마모로 차별화됩니다. 다른 기술로는 이를 제공할 수 없습니다.” Harri Rein은 말합니다. Rein은 툴 기술 그룹의 CTO입니다. Daniel Huber는 원통 연삭을, Daniel Mavro는 평면 및 프로파일 연삭을 맡고 있습니다. 이들은 그룹의 최고 기술 책임자 Christoph Plüss와 함께 8개 회사 브랜드의 기술 개발에 대한 지침을 설정하는 CTO 이사회를 구성합니다. 연삭은 로봇 공학뿐만 아니라 마이크로 전자공학에서도 사용됩니다. 전자 부품용 베이스 플레이트로 사용되는 소위 반도체 웨이퍼 또한 연삭됩니다. 혁신적인 기술의 경우 관련 기계 가공 공정에서만 새로운 소재를 사용할 수 있습니다. 예를 들어, 항공우주 산업 내 제트 엔진의 세라믹 합성물은 연삭을 통해 가장 잘 가공될 수 있습니다. “자동차 또는 항공기 산업용 탄소 섬유 강화 플라스틱으로 만든 경량 부품은 처음 연삭 공정을 통과한 PCD 공구로 가공됩니다.” Huber는 설명합니다.
애플리케이션 상의 장점
연삭을 통한 높은 기계적 품질은 산업 분야에서 다양한 이점을 제공합니다. “자동차 부문의 표면 품질이 더 좋아지면 마찰이 적어 엔진 효율성이 높아집니다.” Mavro는 말합니다. “항공우주 산업의 공차 범위를 좁히면, 예를 들어, 냉각 공기 흐름의 손실을 줄임으로써 제트 엔진의 효율성을 높일 수 있습니다.” 예를 들어, 자동차 부문에서 그룹의 브랜드인 SCHAUDT ShaftGrind의 밸런스 샤프트 연삭과 같은 다양한 혁신적인 애플리케이션을 제공합니다. 이는 카운터 주파수를 생성하여 내연 기관 엔진에서의 원활한 주행을 보장합니다. 이들은 직선 또는 원통형이 아니므로 기계 가공을 까다롭게 만듭니다. 또는, MÄGERLE MFP에서 프로파일 깊이가 최대 11mm 이하이며 폭이 최대 300mm인 공작물을 최대 8개까지 단일 클램핑으로 가공할 때, 스핀들 출력 및 전체 기계의 안정성은 매우 까다로운 문제가 되고 있습니다.
측정 및 연삭
실제 연삭 공정은 측정 또는 드레싱과 같은 인접 공정에 연결할 수 있습니다. “연삭기는 측정 기계와 결합하여 셀을 형성하고, 로봇은 이 두 가지 사이의 인터페이스로 로딩할 수 있습니다." CTO Rein은 말합니다. 결과적으로, 타의 추종을 불허하는 제품이나 심지어 “소등 후” 생산이 가능하여 대량 생산이 가능합니다. 생산할 공구의 파라미터는 WALTER내부 측정 시스템(IMS)에 저장될 수 있습니다. 편차가 발생할 시, 시스템은 기계 공정을 조절하거나 허용오차 범위를 초과하면 생산을 정지합니다. “로트 크기가 작거나 개별 가공품일지라도, 공정 중 측정은 필요한 정확도를 즉시 달성하는 것이 중요합니다” Huber는 설명합니다. 드레싱은 연삭 휠 마모를 보상합니다. 이를 통해 전체 생산 사이클 동안 동일한 가공품 공차와 동일한 품질을 보장합니다. “특정 적용 분야에서 세라믹과 같은 보다 단단한 소재가 점점 더 많이 사용되고 있습니다. 여기에는 초연마재가 필요하며, 이는 결국 높은 강도, 즉 연삭 휠의 금속 결합에 대한 필요성을 의미합니다” Wegener는 설명합니다. 금속 결합제가 사용된 연삭 휠의 경우 WireDress® 기술이 가장 적합한 드레싱용 도구입니다. 연삭 휠은 와이어 전기 방전 원리에 따라 비접촉식으로 드레싱됩니다. 그 결과 입자간의 공간을 최대한으로 하고 절삭 성능을 최적화할 수 있습니다. “WireDress®이 금속 결합 연삭 휠의 획기적인 발전에 기여하리라 믿습니다” STUDER와 공동으로 기술을 개발한 Wegener는 말합니다.
인적 요소
연삭 공정의 결과를 정의하는 다른 중요한 요소는 직원입니다. “이들의 풍부한 경험은 매우 중요합니다”라고 CTO Rein은 강조합니다. 따라서 UNITED GRINDING Group의 모든 회사는 직원들의 교육 및 지속적인 교육에 상당한 자원을 투자합니다(36페이지 또한 참조). 직원의 노하우는 추가적인 디지털화 과정에서도 중요합니다. “첫째로, 현재 연삭기 작업자의 노하우는 지원 시스템 및 데이터베이스에 통합해야 하며, 둘째로, 작업자는 향후 더 어려운 작업을 처리해야 할 것입니다” Huber는 말합니다. 그 이유는 다음과 같습니다. "복합적인 가공 셀을 사용하면 작업자가 보유한 것보다 완전히 새로운 수준의 기술이 필요합니다” Mavro는 덧붙입니다. 또한 UNITED GRINDING Group은 두 가지, 즉 기술을 개선하고 직원들을 개선하는 데 이바지했습니다. 결국 둘 다 연삭 결과를 개선시킵니다.
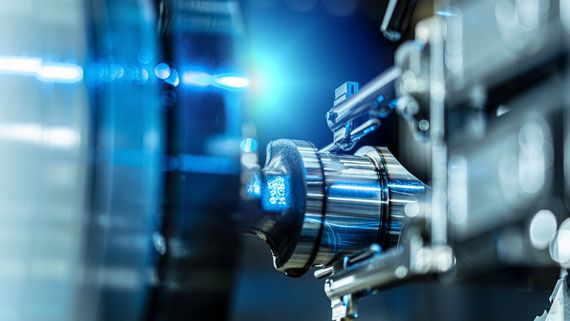
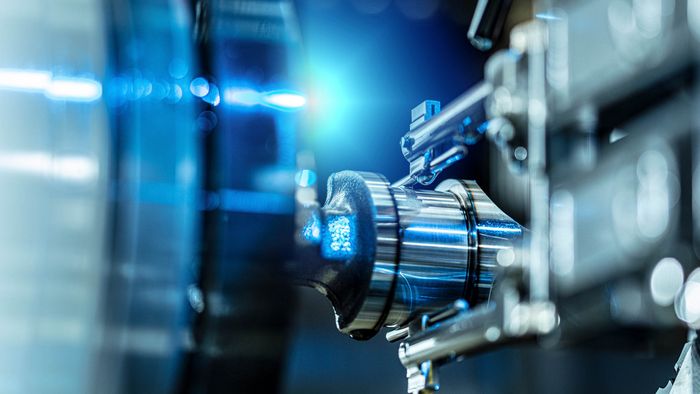
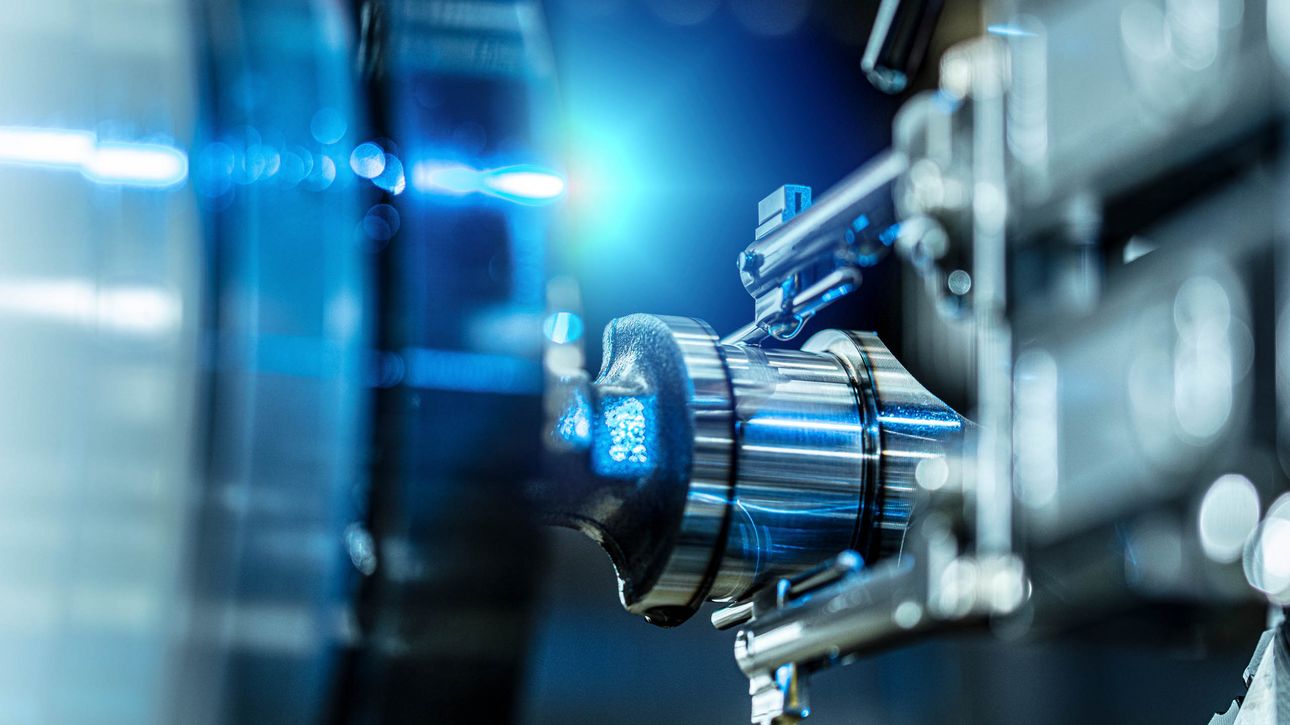